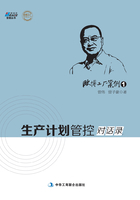
六、第四层觉知:通过检查发现主计划更新不准确的原因
(一)变革前的问题
问题1:产品状态标识不清
现场产品的状态标识不清楚,摆放在车间的半成品属于哪张订单,属于哪个产品,不确定。
:这就导致一个问题,计划员跟进进度的时候,要花很多时间确认每一张订单到底在哪道工序生产。因为订单的前期情况通过报表反馈,如工序交接表、生产日报表,但计划员还要去抽查,确定车间反馈的数据到底准确不准确。如果车间现场的产品标识不清楚,计划员就没有办法确定,当他想去确定的时候就要花很长时间。
问题2:工序无交接或交接数据不准确
不进行工序交接或者有交接但是数据不准确,上工序交给下工序多少,不确定!上车间到下车间多少,不确定!各订单到底在哪个车间、在哪道工序,不确定!
:不进行工序交接或交接数据不准确会导致主生产计划出现错漏。有一家陶瓷厂,它的工序交接很有意思,下工序加工的比上工序交下来的产品还多,这在工序表单有体现。例如,下工序完成了100套,但实际上,上工序只交给下工序95套,还有5套不知道从哪里拿到的半成品,下工序也不管,照做。
:那就说明,交接的时候,交接表上的数量不真实,实际上安排了100套生产任务,但交接表上只反馈了95套,数据写错了。这家公司不重视交接数据,所以PMC更新主生产计划的时候就经常出错。
问题3:车间管理人员不按照计划执行
车间现场管理人员还没有养成按计划生产的意识,不按照计划上确定的任务执行。
:以前的计划模式让车间管理人员、员工养成了不按计划执行的习惯,现在计划准确了,他们还是不按照计划执行。挑订单生产,好做的、单价高的先做,单价低的放到后面再做。
问题4:车间管理人员不愿意做基础管理动作
车间管理人员对现场标识票、看板、交接和5S等动作不理解,执行不到位,理由是觉得这些动作没什么用,浪费时间。
:车间应该做到的事情没有做到,它所反馈的数据就不会很准确,这样就导致计划部门要花大量的时间去确认数据的真实性、去收集车间的真实数据。
:我们开始也提到ZG公司的现场看板很久没更新,没有产品标识,为什么会这样呢?因为那时没有真正实行这种计划模式,但实施了我们这种新的计划模式后,如果还是没有看板的准确填写,没有交接表、标识票的准确填写,就没有办法制订计划,排查的工作量就会很大,就需要对着实物一个个去查。如果现场的看板是很准确的、标识票是很准确的,那么排查的工作量就大大减少了。
在这种计划模式下,标识票、看板和交接单的真实性就显得非常重要。而如果没有这样的计划模式,企业就算有标识票、看板和交接单都没用,这些东西真不真实都没关系,所以很多东西企业做不做与需要不需要是有关系的。
计划不能仅仅局限在计划部的办公室里,计划做出来后,计划部还要到车间做大量的现场排查工作,那么标识票、看板和交接单就应该是车间要做的。对于计划部来说,必须将标识票、看板和交接单纳入管理范围。因为计划部不去管,车间的工人就有可能不认真做了。工人不认真做,计划部的计划就难执行。
在欧博的计划模式里,计划的概念已延伸到了车间现场。所以我们欧博经常提一种概念,就是PMC计划30%的准确性来源于内部,70%来源于现场排查。因为现场排查准确,才能制订出准确的计划,包括仓库物料的排查,甚至包括对采购供应商的生产状况排查。对一切情况的排查是做好计划的前提,排查甚至占了计划70%的工作量,PMC的人员要做好心理准备。
不要把计划当作计算,欧博计划模式的核心在排查。而排查地点不完全在电脑前,不完全在账面,最终的排查点在现场,不管是车间现场、仓库现场,还是供应商的生产现场,总之都在现场。离开现场别谈计划,这是欧博计划模式的一大特色。
抓现场才能够制订计划,这样的计划才能提高准交率,否则制订出来的计划只是一个形式,没办法真正缩短生产周期,不能提高准交率,不能带来数据变化。
我们曾经遇到过这种情况,计划部门什么工作都做了,交期分解、主计划和日计划都做了,但准交率还是没有提高,数据没有改变。后来经检查,发现是现场工作做得不扎实。计划和现场密不可分,这是我们应该树立的新计划思想。
:对中小企业来说,如果计划员从来不下车间,物控员从来不去仓库,那基本可以下一个结论:计划是不真实的,是形式上的,实际的生产绝对不会按照这个计划执行。
(二)变革后的动作
:针对变革前的四个问题,欧博项目组提出了相应的管理动作变革。

针对问题1:产品标识票
:针对问题制订的产品标识票如表1-9所示。
表1-9 产品标识票

:从表1-9中可以看到,产品标识票包含了这些信息:半成品到底属于哪个生产型号,在哪道工序生产,这个部件的名称是什么,要生产多少,生产日期是什么时候,品质是否合格,有没有进行检验等。通过产品标识票,计划员、主管、班组长和员工都能够清楚地知道摆在车间的产品具体信息。
针对问题2:工序交接单
:针对不进行工序交接或者有交接但数据不准确的问题,制订工序交接单(部件流动),具体如表1-10和表1-11所示。
表1-10 ZG公司 工序与 工序半成品交接单

表1-11 ZG公司 工序与 工序物料交接单

:制订车间交接表,通过此表让PMC和车间管理人员了解上下车间的配套情况和交接状况,具体如表1-12所示。
表1-12 ______ 车间______车间交接表

:车间交接表与工序交接表有所不同,不同点在哪里?主要是车间交接表单以产品为最终的交接要求。
例如,实木车间与面漆(涂装)车间交接表上有各个部件的名称,交接日期有3个,什么意思呢?也就是每一次交接,实木车间不可能等整套产品全部做好了才交给面漆车间,第一次交接的有可能是整套产品的5个部分,写明交接时间和交接人,最后品管签字确认,这样分3个批次交接。总之,只有当这个产品的所有部件从实木车间交接给面漆车间之后,车间交接表才算填完,才可以发至PMC以及财务部门。
:车间交接表是控制配套性的一个很好的工具,它的功能相当于一张看板,能很好地控制其他配套动作,不然交接了多少不清楚,交接了哪些产品配件、没交接哪些也不知道。通过这张表能很好地控制,车间不必等完全配套了再往下交接。
:例如,出货排查的时候,看这张表就知道面漆(涂装)车间已经将全部部件交给总装车间了,这些东西还在总装,就不需要到现场核查实物了。
:总之,我觉得PMC的核心工作就是把所有的情况搞清楚,就是觉知。这是制订好生产计划最基本也是最关键的步骤。随时通过看板、交接单,保持觉知,了解情况,是解决问题的关键。
针对问题3:看板管理,频繁检查
:针对车间现场管理人员还没有养成按计划生产的习惯,不按照计划执行的问题,欧博项目组制订了车间整体生产进度看板(如表1-13所示)。车间每天更新,通过看板了解车间整体的生产进度和生产的产品。
:表1-13与计划员使用的主生产计划跟进表内容是相同的,只是在车间形成一张进度看板。车间主管要去关注进度看板,不能仅仅只有计划员在关注,车间主管必须安排车间文员填写进度看板,这样计划员到现场看一下看板就能够大概知道整个进度情况,就能够更新主生产计划跟进表。
表1-13 涂装车间整体生产进度看板日期

制订车间工序进度看板后,车间要每两小时更新一次,通过看板了解各道工序的生产进度和生产的产品。
大家看表1-14中的时间设置,8:00-10:00、10:00-12:00、13:30-15:30和15:30-17:30,为什么要进行每两小时的跟进?因为计划员下到车间之后,他会以两小时的产量评估这两小时的生产有没有异常。假设今日计划数量是100个,每两小时完成25个为正常标准,那么8:00-10:00只完成了十八九个,这样计划员马上就知道车间出现了异常,车间主管也知道这道工序出现了异常,马上就能快速解决。
表1-14 工序生产看板

:这样的看板很多企业都有,但是看板下面的三个要素是很多企业没有注意的。他们有看板、有表单,但没有人监督、检查,没有追究责任。
我们在每一张表单、每一张看板上都有标准、制约和责任,督促员工一定要执行。只要求员工做没有用,还要检查他做了没有,没有做要追究责任,这是贯穿我们欧博整个管理动作的核心思想。
:制订工序滚动日报表(如表1-15所示),让各道工序负责人每天填写,让每天各工序的部件生产情况一目了然。
表1-15 车间生产工序滚动日计划报表

表1-15发到车间之后,车间生产完成就进行填写,填完之后要送至PMC。日报表和日计划表的形式是一样的。PMC根据日报表、工序交接表更新日计划,了解工序每天的生产情况。
制订车间生产日报表(如表1-16所示),让各个车间每天进行填写,让各车间的产品生产情况每天都一目了然。
表1-16 车间生产日报表

:表1-15是工序的,表1-16是车间的。
:对,表1-16与表1-15的区别就是表1-16会统计各种异常时间,如停工待料的时间、设备故障的时间和设备返修的时间等。同时表1-16也统计了生产计划达成率,车间就可依据此表进行考核了。
:还有三要素,即怎么做、谁检查和谁承担责任都清清楚楚。类似的日报表其实很多企业都有,但为什么没有发挥作用呢?因为没有把三要素加进去。
针对问题4:案例分析会,讲解现场推行动作的必要性
:车间管理人员对现场标识票、看板、交接和5S等动作不理解,执行不到位,理由是觉得这些动作没什么作用,浪费时间。因此,欧博项目组的老师针对这种现象,首先组织召开案例分析会,就现场动作与车间管理人员进行集中沟通,讲解现场推行动作的必要性。
这也是我们针对不执行的问题所采取的常规动作,把责任人和整个班组聚到一起,把问题从头到尾梳理一遍。针对某个动作为什么不做进行原因分析,造成了什么损失由责任人自己来讲,要承担什么责任由责任人自己陈述。
这个过程的核心在哪里?让做事情的人觉知自己做事时的状态、心态。有些员工在做事的时候不一定很清楚自己到底做了什么,通过案例分析会,他们能清楚地看到自己是怎么做事的。
我们发现很多管理人员、员工不执行相关动作,不是他们不知道事情的对和错,相反他们知道。例如,知道今天要填这张表单,可不愿意填,问题在哪里呢?在于他的习惯或者是心态,不想做、怕麻烦。通过案例分析会,让他自己觉知一遍自己的问题,下次情况就不一样了。
:很多企业遇到不执行的情况更多的是靠管控、处罚和批判等方式解决,实际上,通过案例分析会可以让每一个犯错、违规的人保持觉知。觉知什么?觉知做这件事情究竟能占用多少时间,让他自己明白,让大家也看清楚这一点。
通过觉知形成压力,让员工自己注意这件事。他不去注意,老是认为很耽误时间,就不愿意填表。所以一说到填表,经常会有人说影响他的收入和效率,其实认真觉知一下,算一下填表的时间就知道根本用不了多少时间。所以,注意和觉知是管理的好方式,因为它能消除对立,找到真相。
:其次,总经理带队进行现场稽核,发现问题及时纠正。稽核员到现场去查看每一个动作的执行情况,发现问题当场要求管理人员改正。每周进行稽核执行率排名,在每周二变革例会上公布排名情况,排名最低的岗位工资扣除100元,连续三周排名最低免除管理职务,这样就能给管理人员形成压力。
通过执行率的排名,让大家知道谁总在执行动作,谁又没执行动作,针对不执行的人进行集中式改变。
通过反复检查,让动作能够落实,解决执行过程中所碰到的问题。