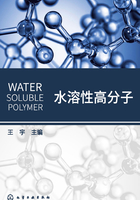
第2章 聚乙烯吡咯烷酮
中文名:聚乙烯吡咯烷酮,聚N-乙烯基丁内酰胺
英文名:polyvinylpyrrolidone,PVP
别 名:聚乙烯基吡咯烷酮、聚维酮、聚N-乙烯基吡咯烷酮
2.1 概述
聚乙烯吡咯烷酮(PVP)是一种非离子型高分子化合物,是一种广泛应用于医药卫生、日用化工和食品等工业领域的水溶性高分子精细化工产品[1]。1938年,德国化学家Reppe首次用乙炔为原料合成PVP。到目前为止,PVP已发展成为非离子、阳离子、阴离子3大类,工业级、医药级、食品级3种规格,分子量从数千至一百万以上的均聚物、共聚物和交联聚合物系列产品,并以其优异独特的性能获广泛应用。PVP作为一种合成类水溶性高分子化合物,不但具有水溶性高分子化合物的一般性质,如胶体保护作用、成膜性、黏结性、吸湿性、增溶或凝聚作用,而且还具有优异的溶解性能及生理相容性。因此,PVP被广泛应用于化妆品、医药、食品加工、纺织印染、颜料、涂料、玻璃纤维、采光、感光材料、彩色显像管和电子工业等众多应用领域中。现在,有关PVP的研究和应用方面的文献年发表量在3000篇左右,充分展示了其方兴未艾的现状和高速发展的前景[2]。
2.2 发展史
PVP及其单体NVP(N-乙烯基吡咯烷酮)最早是由德国巴斯夫(BASF)公司J.Walter.Reppe以乙炔为主要原料合成的,该法称为Reppe法,又叫乙炔法。20世纪50年代,美国GAF公司(后改名为ISP,2011年被美国Ashland公司收购)与德国的BASF公司相继以乙炔法为基础建立了NVP生产线,进而生产出了各种牌号的PVP产品。迄今为止,这两家公司仍然是全世界生产PVP产品的主要厂家[3]。
我国PVP的生产和应用起步较晚,1997年浙江化工研究院、山东东胜精攻集团、上海浦发集团联合成立的上海胜浦新材料有限公司率先实现了500t/a的PVP工业化生产以来,PVP产品的生产开发和应用研究比较活跃,发展速度较快。近年来,国内生产厂家逐渐增加,使我国成为世界上少数几个PVP生产大国之一。特别是随着国内顺酐常压气相加氢和1,4-丁二醇脱氢环化生产γ-丁内酯(GBL)的开发成功和推广应用,使γ-丁内酯的产量逐年增加,同时也为PVP的生产提供了原料基础。
近几年世界PVP总产量中,中国产品占到世界总量还较低,还不到10%,但随着国内PVP生产企业产量的逐渐扩大,产品质量的不断提高,市场占有率在逐年提升,中国PVP产业应该还有很大的发展余地和前景。随着近年来国内1,4-丁二醇、γ-丁内酯的产能不断扩大,为PVP的生产发展提供了丰富的原料,使得进一步开发PVP系列产品成为可能。
经过几十年的发展,PVP已不仅仅是作为一类精细化学品而存在,PVP及其单体NVP的研究和开发工作涉及多门学科、多个领域的知识,已形成自己相对独立的知识体系。随着科学技术的日新月异,PVP及其单体NVP的研究和开发工作具有更为重大的意义和更为广阔的应用前景。
2.3 制备
聚乙烯吡咯烷酮(PVP)的合成包括:N-乙烯基吡咯烷酮(NVP)单体的合成与聚合物PVP的合成。
2.3.1 N-乙烯基吡咯烷酮的合成
目前N-乙烯基吡咯烷酮的合成方法,根据原料的不同可分为:乙炔法、γ-丁内酯法、吡咯烷酮法、顺丁烯二酸酐法(顺酐法)、琥珀酸法等。
2.3.1.1 乙炔法
乙炔法,又叫Reppe法,是德国化学家J.Walter.Reppe在20世纪30年代提出的。该方法以乙炔、甲醛等作为起始原料,经过乙炔与醛的加成、催化加氢、催化脱氢成环、氨解、加成乙炔五步,得到最终产物N-乙烯基吡咯烷酮。其原理反应式如下:
乙炔法的优点在于工艺技术成熟、原料方便易得。但是,该方法反应在高温高压下进行,主要原料乙炔存在爆炸危险;而且,该法反应步骤多,合成路线长,后处理麻烦,设备前期投资大,总收率低,只适合大规模生产而不适合中小规模生产,这也是世界上采用此生产方法的公司如此少的原因。反应中用KOH作为乙炔开环的催化剂,产物中有水分生成,会严重影响催化剂活性,且可能导致吡咯烷酮开环,生成副产物,降低反应收率。尽管美国ISP公司的研究人员用碱金属醇淦代替KOH等方法加以改进,但其反应条件苛刻、步骤多等缺点仍然难以克服,而且实际生产过程会带来环境问题。因此,人们一直在不断努力探索乙炔法之外的新方法。
2.3.1.2 γ-丁内酯法
在除乙炔法以外的NVP新合成方法中,γ-丁内酯法是人们研究得最广泛、最深入的。γ-丁内酯法是以γ-丁内酯和乙醇胺为起始原料,发生氨化开环和闭环缩合反应生成羟乙基吡咯烷酮(NHP),NHP再脱水形成NVP。
根据脱水方式的不同,γ-丁内酯法又分为直接脱水法和间接脱水法。
(1)直接脱水法[4]原理反应式如下:
此方法中脱水催化剂的合成研究是至关重要的部分,催化剂的活性、选择性、寿命直接影响到反应的收率及工程的经济指标。有专利文献介绍[5],采用ThO2、ZrO2作为反应催化剂,收率较低;而稀土氧化物La2O3、Nd2O3作催化剂,转化率和选择性均有所提高。20世纪90年代,有欧洲专利公开了一系列混合氧化物作为N-羟乙基吡咯烷酮脱水催化剂的研究成果,NVP的收率达到80%以上[6]。
γ-丁内酯直接脱水法具有反应步骤少、操作条件温和等特点,但是γ-丁内酯价格昂贵,不适合大规模工业化;而且,很多脱水催化剂在实验室有比较理想的性能,但对于工业化而言仍不够理想。
(2)间接脱水法 间接脱水与直接催化脱水不同的是NHP分子内的羟基被取代,生成中间产物,之后经过分子内消除生成NVP。根据取代基团的不同,目前主要有卤代法和乙酐法两种。
①卤代法[7]。原理反应式:
目前常用的卤代剂为二氯亚砜(SOCl2),但是其反应放热较高,冷却量大,控温不易;且需添加溶剂苯,生成气体副产物SO2,有一定的污染性。也有研究用盐酸作为卤代剂代替传统SOC12,操作简单,不需冷却装置,不需添加溶剂,副产物少,后处理容易,相对传统卤代剂有较大优势[8]。
②乙酐法 原理反应式:
乙酐法需要在高温下进行,容易造成部分NVP产物的裂解,而且中间产物的分离需要高真空条件,收率又不高,因此该方法难以工业化应用。
2.3.1.3 顺酐法
顺酐法采用顺丁烯二酸酐或顺丁烯二酸为原料,加氢制得γ-丁内酯,然后再与氨气反应制得α-吡咯烷酮,α-吡咯烷酮加乙炔生成NVP。原理反应式:
2.3.1.4 吡咯烷酮法
吡咯烷酮法是以α-吡咯烷酮为原料,在催化剂催化下,与羧酸乙烯、环氧乙烷、乙烯基醚等进行加成,之后在加热的条件下经消除反应脱去羧酸、醇、水等小分子得到N-乙烯基吡咯烷酮。原理反应式:
2.3.1.5 琥珀酸法
琥珀酸法是由琥珀酸(丁二酸)和乙醇胺、氢在高温下直接制取NHP,再由NHP脱水得到NVP。原理反应式:
以上NVP合成方法中,除了乙炔法和γ-丁内酯法以外,大部分未实现工业化生产;其他方法,如吡咯烷酮法、顺酐法、琥珀酸法等多是由乙炔法和γ-丁内酯法两种方法演化而来,或者需解决的关键步骤、关键问题相同。
乙炔法原料价格低廉、成本低、收率高,适合大规模大批量生产,且已有广泛应用,技术相对成熟。但其反应需在高温高压下进行,且存在爆炸危险,操作要求较高。γ-丁内酯法操作步骤少,条件温和,且收率高于传统乙炔法,但由于γ-丁内酯的成本价格较高,催化脱水过程在工业上应用时效果差限制了其大规模工业化应用。综上可知,乙炔法和γ-丁内酯法各有优劣,大家在研究应用过程中,可根据自身实际情况进行选择。
2.3.2 聚乙烯吡咯烷酮的合成
N-乙烯基吡咯烷酮可以均聚,也可以和很多乙烯基单体共聚或接枝,生成各种均聚物和共聚物,各自具有不同的性能和不同的用途,各有特色。均聚物PVP的分子量可以1000~1000000不等,可形成不同规格的系列产品,以满足不同的应用要求。NVP很容易用本体聚合、溶液聚合或悬浮聚合方法进行聚合。
2.3.2.1 均聚
(1)本体聚合 NVP可由热引发或引发剂引发发生本体聚合。NVP和过氧化物共热至110℃时,很快发生聚合,反应热不易扩散,导致反应体系温度急剧上升,生成熔融状态的PVP聚合物;冷却后,粉碎即得具有强吸湿性的PVP聚合物粉末。但此法聚合过程中反应体系黏度较高、聚合热不易扩散、局部过热,导致生成的聚合物带有黄色、K值低、残余单体含量高等,不能满足商业产品的要求,很少有工业应用。
(2)溶液聚合 由本体聚合制得的PVP,必须经过提纯,否则不能满足商业产品的要求,因此发展了NVP的溶液聚合。NVP溶液聚合的影响因素主要有溶剂、引发剂、单体浓度、聚合温度、无氧条件、反应体系的pH、聚合时间等几个方面。
①溶剂。NVP可以在很多溶剂,如乙醇、异丙醇、甲醇、乙酸乙酯、苯、水等溶剂中聚合。由于水是最便宜和安全的溶剂,所以一般采用水溶液聚合较多。
由于不同溶剂的链转移常数不同,以及NVP在不同溶剂中的聚合机理不同(在引发剂部分具体介绍),导致链的终止速率不同,得到的PVP聚合物的分子量也各不相同[9]。不同溶剂对PVP分子量的影响见表2-1。
表2-1 溶剂种类对PVP分子量的影响

同时,在不同种类溶剂中,NVP聚合的反应速率也不同。E.Senogles研究了不同种类溶剂对NVP聚合反应速率的影响,测出了不同溶剂中NVP聚合反应的活化能[10],见表2-2。
表2-2 50%NVP溶液聚合的链增长和链终止活化能

②引发剂。NVP单体可以通过化学引发、光引发、辐射引发等方式发生聚合反应。其中,化学引发剂具有方便、价格低廉、无须专门设备等优点,因此工业生产PVP大多采用化学引发剂引发。
NVP聚合反应中常用的化学引发剂主要有以下三大类型。
a.热分解型引发剂,该引发剂在加热时会分解,所产生的活性游离基引发单体聚合。
b.氧化-还原型引发剂,该引发剂先发生氧化作用产生离子,再发生还原反应,将离子还原为活性游离基引发单体聚合。
c.低温游离基型引发剂,多数是过氧化物和偶氮双腈类物质。
按照活性引发离子的种类来分,引发NVP聚合的引发剂主要有以下几类。
阳离子引发剂:BF3。
阴离子引发剂:酰胺的钾盐。
游离基引发剂,有过氧化物类引发剂和偶氮类引发剂两类。
过氧化物类引发剂:过氧化氢、叔丁基过氧化氢、过氧化二苯甲酰、过氧化甲乙酮、叔丁基过氧化新戊酸酯、叔丁基过辛酸盐、叔丁基过苯甲酸等。
偶氮类引发剂:偶氮二异丁腈、偶氮二异庚腈、偶氮二丁酰胺、偶氮二异丁酸二甲酯、偶氮二异丁咪唑啉盐酸盐等。
实际生产过程中,在反应体系中还要加入引发剂活化剂,以提高引发剂引发活性,缩短反应时间。不同的引发剂需要使用不同的引发剂活化剂,如:过氧化氢的活化剂可以使用碱性物质,如浓氨水、胺等;而某些有机过氧化物引发剂的活化剂为Co、Ni、Mn、Cr等金属有机盐。引发剂活化剂的加入有时会改变反应体系的pH,并影响反应的诱导期、反应速度和PVP的分子量。例如,当采用过氧化氢为引发剂时,不同引发剂活化剂对反应的影响见表2-3。
表2-3 不同引发剂活化剂对过氧化氢引发效果的影响

Fikentscher首先发展了NVP的水溶液聚合方法。以过氧化氢为引发剂,以浓氨水为引发剂活化剂,在水溶液中的聚合机理如下。
链引发:
链增长:
链终止:
过氧化氢分解所生成的羟基在产物中转化为端基。由于在链的终止反应中发生吡咯烷酮环的裂解,所以PVP的第二个端基是醛基,而在产物中还会有少量的α-吡咯烷酮。
采用偶氮二异丁腈为引发剂时,在水溶液中的聚合机理如下。
链引发:
链传递:
链终止:
NVP在水溶液中容易被酸催化而发生水解作用,生成α-吡咯烷酮和乙醛。机理如下:
因此采用水溶液聚合制备PVP时,需要注意控制反应体系的酸度不能过高。另外,水溶液聚合过程中,反应体系的pH值会对反应速率造成一定影响,当pH值达到13时,聚合反应几乎停止。
NVP在醇类等有机溶剂中进行聚合反应时,反应机理不同于水溶液聚合。以有机过氧化物为引发剂,在有机溶剂中的聚合机理如下。
链引发:
链传递:
链转移形式的链终止:
采用有机过氧化物作为引发剂聚合时,有机过氧化物产生的烷氧基与溶剂作用生成溶剂自由基。聚合反应过程中的聚合引发剂是溶剂自由基而不是烷氧基。链的终止是通过吸引溶剂分子中的一个质子完成的,得到一个烷基端基和一个溶剂自由基,继续引发聚合。质谱分析证明,用过氧化物作引发剂时,聚合物端基是溶剂自由基和在链转移中生成的氧原子,由于没有发生吡咯烷酮环的裂解,因此所制备的聚合物较纯净,没有醛基端基的产生,在氧化条件下比水溶液聚合更稳定。
采用偶氮二异丁腈为引发剂,在乙醇溶液中的聚合机理如下。
链引发:
链传递:
链终止:
因此,即使其他条件相同,而溶剂不同,所生成的PVP的K值也不相同。
工业上选择引发剂的主要依据是考虑引发剂的分解温度、半衰期、安全性、经济费用等因素。但是,无论选用哪一种引发剂,都需要考虑引发剂用量对PVP分子量的影响。
以偶氮二异丁腈为引发剂,在相同的反应条件下,随着引发剂用量的增大,PVP的分子量减小。因为偶氮二异丁腈引发NVP聚合的反应属于游离基链式聚合,根据链的引发、链的传递和链的终止原理:当引发剂的能量相当于引发剂分子中弱链的链能时,引发剂分解为初级游离基;初级游离基再与不饱和的π键反应,生成σ键,形成单体游离基;单体游离基再与单体反应,形成增长游离基;增长游离基之间相互反应,生成高分子化合物。在其他条件相同时,反应体系的引发剂浓度越高,则生成的游离基越多,结果使链的传递反应不易进行,而链的终止反应则容易进行。PVP分子链来不及增长到足够长时就发生了链的终止反应,使聚合度减小,产物的K值变小。
以过氧化氢-氨(5mL 30%过氧化氢与10mL浓氨水)混合溶液为引发剂时,结果与偶氮二异丁氰为引发剂时相同:PVP的分子量随着引发剂用量的增大而减小,用量在0.5%~2.0%时,PVP分子量随引发剂用量的变化明显;而当引发剂的用量超过2.0%时,PVP分子量随引发剂用量则无明显变化。
引发剂用量对聚合反应的诱导期、反应速率和产物PVP的K值的影响见表2-4。
表2-4 引发剂用量对聚合反应的诱导期、反应速率和K值的影响

一般条件下,引发剂用量大于0.3%时聚合反应可很容易地进行,但制得的PVP分子量较小。若要制得K值在50~100的PVP聚合物,则要进一步降低引发剂的用量。但引发剂用量太小,则难以引发聚合反应。此时,可以通过进一步提纯NVP除去微量的阻聚物,在无氧条件下聚合,使聚合反应得以被引发。另外,采用辐射活化,聚合反应在较低温度下也可进行。即使用一般纯化的NVP,不在无氧条件下,制得的聚合物K值也可增大到50~100。例如,30%NVP水溶液加入0.006%的引发剂,在310~410nm的紫外线下照射,几个小时内即可完成聚合反应,制得K值为100的PVP聚合物。然而相同情况下,引发剂用量为0.6%时,PVP聚合物的K值只有32。
③单体浓度。Karaputabze等研究了NVP在光辐射条件下的聚合机理,发现NVP的浓度主要影响聚合速率,对K值基本没有影响。当NVP单体浓度低于30%时,聚合反应速率随NVP单体浓度的增大而增大;当NVP单体浓度在30%~60%时,聚合反应速率基本保持不变;当NVP单体浓度大于60%时,聚合反应速率随NVP单体浓度的增大而减小。在相同条件下,100%含量的NVP不聚合。这一现象可用水与NVP的氢键缔合作用对聚合的影响来解释。可见在NVP的聚合中,水是非常重要的因素。研究同时发现,K值不随NVP浓度变化而变化,这和一般聚合不同。NVP单体浓度对K值、聚合反应速率的影响如图2-1所示。

图2-1 NVP单体浓度对K值、聚合反应速率(PG)的影响
Woodhams则认为NVP聚合反应速率很大程度上取决于引发剂和NVP的浓度。当NVP单体浓度为低于50%时,聚合反应速率与浓度呈正比关系;当NVP单体浓度大于60%时,则聚合反应速率下降。
另外,崔英德研究发现,NVP的浓度过高时,生成的PVP在反应体系中的浓度提高,反应体系的黏稠度也就提高,反应产生的热量不容易扩散,则反应变为类似于本体聚合了。因此,溶液聚合时NVP单体的起始浓度一般为30%~60%(反应物料体积比)比较合适。
④聚合温度。聚合反应的温度主要影响聚合反应速率和PVP的分子量。与大部分聚合反应一样,聚合温度越高,NVP聚合速率越快。
由于只有在供给一定的热能之后,引发剂才能发生作用而引发反应聚合,所以在反应开始之时,需要给反应体系加热。而在聚合反应进行之时,由于放出大量的反应热,则需要控制一定的条件保持聚合温度恒定,否则温度过高,PVP的分子量不易控制;同时,反应产生的热量不易扩散,容易导致PVP变色。
由于聚合反应中各个基元反应的活化能不同,所以聚合温度变化时,引发剂的热分解速率、链的引发速率、链的增长速率和链的终止速率的反应速率常数的变化不同,使引发剂的热分解速率、链的引发速率、链的增长速率和链的终止速率发生变化。而引发剂的热分解速率、链的引发速率、链的增长速率和链的终止速率的变化,又会使聚合物的分子量发生变化。
同时,不同溶剂体系的活化能差别较大。50%NVP溶液聚合时链的增长活化能和链的终止活化能见表2-2。
一般来说,采用化学引发剂引发NVP聚合时,聚合温度越高,PVP的分子量越大。这说明随着聚合温度的升高,链的终止反应受到抑制,而链的增长反应速率则加快,所以能够表现出聚合物的分子量随着聚合温度的升高而增大。不同聚合温度下所制得的PVP分子量见表2-5。
表2-5 聚合温度对PVP聚合物分子量的影响

①乙醇为溶剂,偶氮二异丁腈为引发剂。
②水为溶剂,偶氮二异丁腈为引发剂。
③水为溶剂,过氧化氢-浓氨水为引发剂。
⑤无氧条件。氧气具有阻聚作用,能够降低聚合反应速率,加快链的终止反应,降低聚合物的分子量。因此,在NVP聚合反应过程中,通常会向聚合反应体系中通入氮气,以排除聚合体系中的氧气,使聚合反应在无氧条件下进行。实验发现,其他条件相同时,通氮气制得的PVP的分子量远大于不通氮气制得的PVP的分子量。
⑥反应体系pH。NVP在酸性水溶液中易水解生成α-吡咯烷酮和乙醛,因此聚合反应体系的酸度不宜过大,一般保持中性或碱性。同时,反应体系起始pH对诱导期、反应速率也有一定的影响,但对K值无太大影响,见表2-6。有研究表明,pH在7~12对聚合速率影响不明显,pH大于12时聚合速率明显减慢,pH大于13时反应几乎停止。
表2-6 起始pH对诱导期、反应速率和K值的影响

综上,影响分子量(K值)有多种因素:过氧化物类引发剂多用于制备低分子量PVP,偶氮类引发剂多用于制备高分子量PVP;引发剂用量大,K值低;用支链溶剂比用直链溶剂或未取代芳香族化合物溶剂得到的聚合物K值低;对于低分子量PVP的聚合,仲醇是较好的溶剂;降低反应温度,一定程度上也可降低K值;投料方式也对分子量有一定影响。在采用溶液法聚合生产制备PVP时,可根据需要,对溶剂、引发剂、聚合温度等因素进行选择调节。同时,适量控制足够的反应时间,保证聚合反应完全,可大大降低PVP产品中残余单体的含量,从而满足各领域应用要求。
(3)悬浮聚合 NVP的悬浮聚合报道比较少见。美国国际特品(ISP)公司(2011年被Ashland收购)曾报道一种NVP的悬浮聚合工艺,即采用庚烷为连续相,以一种叫GentexV-516的表面活性剂为分散剂,将NVP和少量水一起分散呈油滴状,悬浮于庚烷中,再用偶氮二异丁腈在25℃下引发聚合,可制得平均分子量高达67万的PVP聚合物。
上述悬浮聚合中加入二乙烯苯等双官能团乙烯基单体进行共聚成交联型PVP,具有高吸水性能,但不再溶于水和其他溶剂。GAF公司报道了多重交联PVP的制备技术。不溶性PVP还可用离子型催化剂的聚合技术制得,使NVP聚合成交联的不溶性聚合物。
2.3.2.2 共聚
NVP单体的分子结构中含有乙烯基结构,极容易与其他含有乙烯基结构的不饱和单体发生共聚反应,生成具有NVP结构单元和其他共聚单体结构单元的共聚物,这种共聚物的性能可以综合PVP与其他聚合物性能的优点。
(1)共聚单体 许多具有乙烯基结构的不饱和化合物都可以与NVP单体发生共聚,举例如下。
①酯类:乙酸乙烯酯、乙酸丙烯酯、二乙酸丙烯酯、二甲基氨基乙基甲酸丙烯酯、异丁烯酸酯、甲基丙烯酸甲酯、丙酸乙烯酯、丙烯酸异丙烯酯、乙烯基丙烯酸酯、丙烯酸异辛酯等。
②醚类:乙烯基苯基醚、乙烯基异丙基醚、乙烯基环己基醚、乙烯基丁基醚等。
③酰胺类:N-乙烯基苯亚酰胺、丙烯酰胺、乙烯基己内酰胺等。
④烃类:乙烯、苯乙烯、十六碳烯等。
⑤卤代烃类:氯乙烯、三氯乙烯等。
⑥醇类:丙烯醇等。
⑦聚合物类(接枝共聚):聚丙烯腈、纤维素、尼龙、明胶等。
⑧双官能团类(交联聚合):亚甲基双丙烯酰胺、二乙烯基苯等。
⑨其他类:丙烯腈、马来酸酐、乙烯基三甲基硅烷、乙烯基三甲氧基硅烷、乙烯基咪唑等。
此外,NVP也可以与两种不饱和单体共聚(三元共聚),得到三元共聚物,如:NVP/DMAPMA/乙烯基聚二甲基硅氧烷三元共聚物。
(2)共聚方法 NVP的共聚反应可以采用本体聚合、溶液聚合或者乳液聚合,溶剂可以使用水、甲醇、乙醇、异丙醇、苯、甲苯、丙酮、乙酸乙酯、己烷等。最常用的引发剂是偶氮二异丁腈,它具有反应速率快、转化率高、用量少的优点。
由于共聚物中各个聚合单体的组成不同,共聚物的性能也不相同。所以NVP共聚物合成中的关键问题,是控制一定的共聚反应工艺条件,使共聚物的组成保持在一定的范围之内。一般说来,在聚合工程中,有两种方法来控制聚合物的组成,使其保持恒定:一是控制转化率法,即选择一个合适的反应单体配比,在共聚反应进行到一定的程度时,将聚合终止。这种方法适用于共聚物组成与转化率的关系曲线比较平坦的体系。第二种方法是分批加入单体法,即将反应比较快(竞聚率比较大)的单体分批补加或者连续补加到反应比较慢(竞聚率比较小)的单体中进行聚合反应。这种方法适用于共聚物组成与转化率的关系曲线的斜率比较大的体系。所以,在研究NVP的共聚反应时,了解各个单体的竞聚率非常重要。常见可共聚不饱和单体对NVP(M1)的共聚参数见表2-7。
表2-7 不饱和单体对NVP(M1)的共聚参数

接枝也是共聚的一种方法,接枝共聚一般采用先预辐射处理待接枝的聚合物,再用NVP单体处理的方法,也可以采用在偶氮类引发剂或者过氧化物引发剂的存在下直接接枝的方法。通常被NVP接枝的聚合物有:聚丙烯腈、纤维素、尼龙、聚丙烯酰胺、明胶、黄原胶等。采用接枝共聚可以克服PVP在使用时与某些高分子化合物相溶性差的缺点,以及改善某些聚合物的手感、吸湿性等。
(3)几种NVP共聚物介绍
①NVP/乙酸乙烯酯共聚物。NVP/乙酸乙烯酯共聚物,简称PVP/VA,根据不同的NVP/乙酸乙烯酯(VAc)单体组成比,有PVP/VA73、PVP/VA64、PVP/VA55、PVP/VA37等商品牌号。它是一种无色透明的固体,微溶于水(溶解性可通过NVP与VAc组成比调整),可溶于异丙醇、乙醇、乙酸丁酯等有机溶剂,无毒,不容易燃烧。除了溶解性,PVP/VA的黏性等也可以通过调整NVP与VAc的组成比来调整。
PVP/VA分子结构单元中既含有NVP结构单元,又含有乙酸乙烯酯结构单元,因此具有PVP和PVAc(聚乙酸乙烯酯)的某些性能特点。PVP/VA的某些性能和特点与PVP类似,它既保留了PVP作为功能高分子的功能,与各种低分子,如多酚、偶氮染料、多重金属阳离子以及各种高分子以及生物大分子,如蛋白质等有很强的络合能力,又克服了PVP价格昂贵等缺点。
NVP和乙酸乙烯酯在共聚之前都需要进行预处理,蒸馏提纯以除去阻聚剂。引发剂一般使用重结晶处理过的偶氮二异丁腈。具体来说,将纯化的NVP和乙酸乙烯酯投入带搅拌的反应器中,以乙醇为溶剂,加入重结晶处理过的偶氮二异丁腈引发剂后加热,一般3h内即可完成反应。在该反应过程中,反应温度越高,引发剂的分解速率也就越快,共聚反应速率越快;溶剂对共聚反应速率也有一定的影响:当使用乙醇为溶剂时,乙醇的含水量越高,反应速率越快,且PVP/VA的K值也随乙醇含水量的增加而增大。另外,两种单体NVP和VAc的投料比例对单体转化率和共聚产物有很大的影响。其他反应条件相同时,投料比中乙酸乙烯酯的比例越低,则单体转化率越高,PVP/VA中NVP结构单元的含量也越高。这主要是因为NVP/VAc共聚体系中,NVP的活性比VAc高。
PVP/VA具有各种优良特性,在食品、化妆品、医药等诸多领域具有良好的应用前景。当前,PVP/VA主要应用于化妆品和医药领域。
PVP/VA具有很好的成膜性,可以形成透明光亮的薄膜,用作发型保持剂的成膜树脂PVP/VA克服了天然胶和聚丙烯酰胺成膜树脂柔韧性不足的缺点,并且所形成的薄膜的耐候性和再梳理性好,富有弹性和光泽,容易洗去。自20世纪70年代开始,PVP/VA在国际上被广泛用作发型保持剂。
在医药领域,PVP/VA可用作防止药物对皮肤刺激的防刺激剂、药物的赋形剂、防结晶剂和黏合剂等。
除此之外,PVP/VA还可以用作口香糖基、啤酒澄清剂、防污染剂等。其中,用PVP/VA配制的防污染剂,具有很好的防污染能力,并且在水洗阶段和退浆阶段都有很好的使用效果。
PVP/VA在不少领域有取代PVP的趋势,日益受到人们的重视,成为研究最活跃、最成熟的一种NVP共聚物。
②NVP/二甲胺基乙基甲基丙烯酸酯(DMAEMA)共聚物[11]。NVP/DMAEMA共聚物一般为20%的黏稠水溶液或50%的黏稠乙醇溶液,pH范围5~8,是优良的成膜树脂和调理剂。主要用于化妆品中,对头发和肌肤有柔和的亲和作用,而且不会积聚,能增加头发的干梳和湿梳性能,令秀发更加滑爽、光亮、丰满和增添丝般柔滑感觉。与醇系、多种化妆品添加剂、增稠剂和气雾产品的推进剂配伍性好。
③NVP/甲基丙烯酰氧乙基三甲基氯化铵共聚物[12]。NVP/甲基丙烯酰氧乙基三甲基氯化铵共聚物,可作为一种新型的阳离子型絮凝剂,由于在产物中引入了乙烯基吡咯烷酮基团,使得共聚物的水溶性得到提高,可用作水处理剂。
这种共聚物分子量比较大,在悬浮液中长链大分子伸展开,可同时吸附两个或以上的微粒,像纽带一样将各个粒子联合起来成为大粒子,从而使粒子沉降速度大大增加;并且重复单元中含有带电基团,这些带电的官能团可以强烈地吸附细微颗粒,并中和其表面电荷,在微粒和微粒之间形成架桥作用,使细微分散的悬浮颗粒和胶体物质聚集成为大絮体,从而使颗粒沉降速度大大提高,溶液变得澄清。
④NVP/二甲胺基乙基甲基丙烯酸酯季铵化共聚物[13]。NVP/二甲胺基乙基甲基丙烯酸酯季铵化共聚物一般以20%含量的高黏度水溶液形式呈现,它是阳离子型的水溶性聚合物。在化妆品中应用较多,对头发有较好的亲和作用,抗静电;能形成透明、无黏性、连续的薄膜,令头发更易梳理、有光泽、平整,并能提供调理和坚挺的效果,积聚极少,可与非离子、阴离子及两性表面活性剂配伍。
⑤NVP/二甲胺基丙基甲基丙烯酰胺共聚物[13]。NVP/二甲胺基丙基甲基丙烯酰胺共聚物一般为10%水溶液,能够形成透明、不黏的连续膜。在化妆品中应用较多,在较低的用量下达到较高的定型能力。甚至在极潮湿的气候下也能具有持久的卷曲保持和硬度增强能力。其具有假阳离子性,能够提供调理和丰满有型的感觉,并提高秀发亮度、整理性和清洁感。
⑥NVP/苯乙烯共聚物[12]。NVP/苯乙烯共聚物在水溶液中呈低黏度乳液,粒子是亚微细粒。乳液具有极佳的冰冻融化性能以及剪切稳定性。对pH值及盐浓度适应性宽,仅稍微引起乳液凝聚。由于它在高pH值下的稳定性,所以在碱性冷烫液、定型液、香波、浴制品中应用极有利。配方中用量一般在1%以下,使用安全。
综合相关报道,已经开发的NVP共聚物的种类及其应用领域主要如下。
a. NVP/乙酸乙烯酯:化妆品、医药、印染助剂、食品添加剂。
b. NVP/乙酸乙烯酯/丙酸乙烯酯:化妆品。
c. NVP/丙烯酸特丁酯/甲基丙烯酸:化妆品。
d. NVP/明胶:感光材料。
e. NVP/三烯丙基异腈尿酸酯:亲水性大孔吸附树脂。
f. NVP/甲基丙烯酸羟乙酯/苯乙烯:亲水、透气性材料。
g. NVP/季铵盐:化妆品。
h. NVP/顺丁烯二酸/甲基丙烯酰胺:阻垢分散剂。
i. NVP/丙烯酰胺:固定化酶。
j. NVP/苯乙烯:调理剂、遮光剂(化妆品)。
k. NVP/十六碳烯:调理剂、防水剂、颜料分散剂(化妆品)。
l. NVP/甲胺乙烯异丁烯酸酯:调理剂、定型剂。
m. NVP/乙烯基丙烯酯:发型保持剂的硬化剂和成膜剂。
n. NVP/乙烯基己内酰胺/二甲胺乙烯甲基丙烯酸甲酯:发型保持剂的成膜剂和发型固定剂、染发剂、可剥离面膜。
o. NVP/三丁基丙烯酸酯/丙烯酰胺:发型保持剂。
p. NVP/丙烯酸异辛酯:悬浮聚合的分散稳定剂。
q. NVP/(部分水解的)聚丙烯酰胺:吸水剂、油田降水剂。
吸水性NVP共聚物由于具有良好的吸水、保水性能,透氧性能,生物相容性好,无刺激性,在国外被用于人造角膜和隐形眼镜材料、医药缓释剂等。吸水性NVP/聚丙烯酰胺共聚物替代聚丙烯酰胺作为采油助剂,可以改善聚丙烯酰胺热稳定性差、在高离子强度盐水中物理性能差等缺陷。
综上可看出,NVP共聚物在医药、化妆品、采油、农业、卫生用品等领域有着广泛的应用前景。
2.3.2.3 交联聚合
NVP在特定条件下发生交联聚合反应,生成一种不溶于水、强酸、强碱以及一般有机溶剂的交联聚合物——交联聚乙烯吡咯烷酮,又称交联聚维酮(PVPP)。交联聚维酮为白色至乳白色、细分散、自由流动、几乎无味、无臭或稍有气味的吸湿性粉末,不溶于水、乙醇、乙醚等所有常用溶剂。分子式为(C6H9NO)n,化学结构与PVP相同。在结构上,交联聚维酮可以看作是具有线型分子结构的聚乙烯吡咯烷酮(PVP)分子链通过物理方法或者化学方法相互交联而成,故又可将交联聚维酮称作交联的PVP或不溶性PVP。因此,交联聚维酮除了具有PVP所具有的吸附络合性、生理相容性等优良特性外,还具有水不溶性、吸水保水性等性能。
采用不同的制备方法生成的交联聚维酮在水中具有不同的溶胀能力,呈现出的形态多种多样,有软凝胶、白色粉末或多孔粒子,可满足不同的需求。根据交联度的不同,PVPP的表现形式也不同:低交联度的PVPP表现为超强吸水性树脂,具有很强的吸水、保水能力;其吸水能力可达自身重量的数倍,甚至数十倍;中等交联度的PVPP为吸水凝胶;高交联度的PVPP不溶于水,吸水能力也差。
PVPP的合成方法有:PVP交联法、NVP自交联聚合法(爆米花聚合)和NVP单体与多个不饱和基化合物(如双官能团交联剂)交联共聚法。
(1)PVP交联法 PVP交联法有PVP自交联和PVP交联剂交联两种方法。其中,PVP自交联是采用过硫酸盐、过氧化氢等对PVP进行处理,得到软凝胶状态的低交联度PVPP;PVP交联剂交联是在过氧化物存在下,用α,ω-二烯烃交联剂处理PVP,可得到低交联度PVPP。
(2)NVP自交联聚合法(爆米花聚合) 爆米花聚合(增殖聚合)可以得到高交联度PVPP。如:在碱金属氢氧化物存在下,NVP加热到100℃以上发生反应,生成双官能团化合物,自交联为高交联度PVPP。该方法合成的PVPP交联度比较高,不溶于水,吸水能力也比较差。
有研究指出,爆米花聚合的机理实际上是,NVP单体在碱金属氢氧化物的存在下,首先相互反应,生成少量双官能团化合物,这些双官能团化合物起到交联剂的作用,再由这些双官能团交联剂与NVP单体共聚生成PVPP。
(3)交联剂与NVP交联共聚法 该方法通常是在氮气保护条件下,水溶液中的交联剂与NVP在引发剂(如偶氮二异丁腈)的引发下发生共聚反应,生成PVPP。常用到的交联剂为双官能团化合物,主要有二乙烯基苯、N,N'-亚甲基双丙烯酰胺、α,ω-二烯烃等。该方法可以通过控制与NVP共聚的双官能团交联剂的种类及其用量(即交联度)来达到控制PVPP的性能及其应用领域要求的目的。
很多研究表明PVPP没有任何致畸、致突变和致癌作用,对皮肤和黏膜有很好的耐受性。结合PVPP的上述优良性能,使其被广泛地应用于医药、食品、化妆品等众多领域。
2.4 性质
聚乙烯吡咯烷酮(PVP)是由N-乙烯基吡咯烷酮(NVP)线性聚合而成的水溶性高分子化合物。PVP不仅具有水溶性高分子的一般性质,如胶体保护作用、成膜性、黏结性、吸湿性、增稠性、凝聚作用以及与某些化合物的络合能力等,而且以优异的溶解性和生理相容性,受到人们的重视青睐。在合成的高分子产品中,像PVP这样既溶于水,又溶于大部分有机溶剂,毒性极低,生理惰性,相容性好的品种十分少见。
PVP因其优异的性能,受到了人们越来越多的关注,并在医药、食品、化妆品、水处理、纳米技术等这些与人们健康、科技发展密切相关的领域中获得越来越多的应用。下面将就与PVP应用密切相关的物化性质简要概述。
2.4.1 基本物理属性
市售PVP是白色、乳白色或者略带黄色的固体颗粒粉末。PVP具有良好的水溶性,其在水中的溶解过程是一个放热的过程,溶解热为-4.8×103J/mol。PVP固体的密度为=1.25,折射率
=1.53。
PVP的堆密度与其分子量及生产工艺过程中的干燥方法有着密切的关系。一般来说,对于市售的固体PVP颗粒,其堆密度与分子量、干燥方法、颗粒大小有关,一般的堆密度可以通过式(2-1)计算:
(2-1)
式中,dV为PVP的堆密度,g/mL;M为PVP的质量,g;Vp为PVP的堆体积,mL。
PVP的分子量通常用K值来表示,据德国BASF公司报道:当K值<30时,其堆密度为0.4~0.6g/mL,当K值大于90时,其堆密度为0.11~0.25g/mL,不溶性PVP则为0.28~0.38g/mL。美国ISP公司报道,其PVP当K值为30时的堆密度为0.3g/mL。由此可见,当生产工艺及干燥方法改变时,PVP的堆密度会有较大的变化,不同厂家之间的同分子量PVP在堆密度方面也会存在一定的不同。另外,测定方法的不同也会导致PVP堆密度数据的差异。
但总体上可以看出,随着PVP分子量的增大,其堆密度减小,这是因为PVP分子量越大,其接枝程度越高,分子链越长,PVP分子堆积在一起时相互之间的空隙就越大;反之,分子量越小,PVP分子堆积在一起时相互之间的空隙就越小,进而使其有较高的堆密度。颗粒大小对PVP的堆密度也有着直接的影响,颗粒越大,颗粒间空隙越大,一定质量下的PVP堆体积就越大,由式(2-1)可以看出,颗粒越大,PVP的堆密度就越小。
2.4.2 PVP分子量测定及其表征
分子量分布特性是高分子聚合物的一个重要性质,从图2-2所示的PVP凝胶色谱图可见,PVP与其他自由基聚合的产物一样有典型的Schulg-Flory分子量分布[2]。

图2-2 PVP的凝胶色谱图
从图2-2中可以看到,PVP的分子量遵循Schulg-Flory分布,并且高分子量的聚合物分布曲线较宽,而低分子量的聚合物分布较窄。这是因为分子量越大的聚合物,形成的分子链越长,在分子链形成的过程中就越有可能在某些部位因为接枝而形成侧链,接枝程度越高,则分子量的分布越宽。另一方面,在自由基聚合的链增长过程中随时都会发生链终止反应,对于相同的聚合物而言,最终形成的聚合物平均分子量越大,其聚合物的分子量最大值就越大,而无论聚合物的平均分子量大小如何,其分子量的最小值是相等的,所以平均分子量越大,不同分子量的聚合物数量就越多,也就意味着分子量的分布越宽。
成品PVP按分子量大小分成若干等级,一般用Fikentscher公式的K值来表示,K值是通过测定一定浓度的PVP水溶液的相对黏度,采用Fikentscher公式计算得到的,是不随PVP溶液的浓度而改变的常数。测定K值的常用方法是乌氏毛细管黏度计法测得PVP水溶液的相对黏度η,通过Fikentscher公式计算K值如下[14]:
(2-2)
或
(2-3)
式中,K0为Fikentscher常数;K=1000K0;C为100mL溶液中溶解的PVP质量(g),通常为5g/100mL,1g/100mL或0.1g/100mL;η为PVP水溶液的相对黏度。
K值与相对黏度的关系见表2-8,通过测得相对黏度,即可从表中查得K值,进而确定分子量。
表2-8 PVP的相对黏度与K值

为了更明确地掌握PVP水溶液的相对黏度随K值的变化关系,对PVP水溶液相对黏度与K值关系作图,如图2-3和图2-4所示。

图2-3 相对黏度与K值(85~95)的关系

图2-4 相对黏度与K值(10~35)的关系
在式(2-2)中,当C→0时,,则式(2-2)变为下式:
(2-4)
[η]定义为PVP的特性黏度,它只与分子量或K值有关系,而不随PVP溶液的浓度而变化,它直接可由式(2-4)近似计算得到,也可用外推法得到,即测定不同浓度下的PVP的相对黏度,作相对黏度-浓度曲线,然后将曲线外推到C=0时曲线上对应的相对黏度值即为PVP的特性黏度。特性黏度随PVP的分子量的增大而增大,[η]随PVP分子量变化的关系如图2-5所示。

图2-5 特性黏度与分子量或聚合度的关系
利用特性黏度[η],即可按Mark-Houwink公式计算黏均分子量,即:
(2-5)
式中,a,b均为常数,a=1.4×104,b=0.7。
由式(2-4)、式(2-5)可以得出下式:
(2-6)
由上式可以看出PVP的K值与分子量之间并没有显著的函数关系,如图2-6所示。

图2-6 K值和分子量的关系
同样也可以将相对黏度与分子量直接相关联作曲线,结果如图2-7所示。可以在直接测得相对黏度后,直接从曲线上读出PVP的分子量。

图2-7 相对黏度与分子量的关系
从上述论述中,我们可以发现,PVP的K值、特性黏度[η]、分子量有着一一对应的关系,它们之间的具体关系见表2-9。
表2-9 PVP的K值与特性黏度[η]和分子量之间的关系

重均分子量是通过测定分子质量的方法测定的,例如用超滤法或光衍射法测定的;数均分子量
使用测定分子数量的方法测定,如渗透压法和端基分析法确定。同时我们用
来表征分子量的分散程度,即为分散系数,系数越大说明分子量的分布越宽,越分散。PVP的重均分子量、数均分子量与K值的关系见表2-10。
表2-10 不同K值PVP的分子量对照

表2-10中的K值对应的黏均分子量与表2-9中所列有一定的区别,这是因为上述数据都是以市售产品为样品而测得的,与推导公式时的实验室样品有一定的差异。某一标示K值的商品PVP,其实际分子量大都分布在其名义值两侧的一定范围内。此外,聚合方法的不同,乃至某一条件的细微改变、产品纯化方法、干燥工艺、分子量的测定方法和条件的不同都会导致测定结果的不同。
2.4.3 玻璃化转变温度
许多长链的聚合物在加热时表现出特性的系列变化。所有线型聚合物在低温时都是玻璃态。当温度升高达到某个温度,聚合物由玻璃态变为橡胶态,聚合物由玻璃态转变为橡胶态,这个转变温度就为玻璃化转变温度(Tg)。物质的化学结构、分子量和分子量分布、分子间的相互作用等等都会对物质的玻璃化转变温度有影响。
Sugiura和Fujii[15]通过测定PVP的三个品种PVP K15、PVP K30、PVP K90在10~100℃的比体积,并对每个品种,将比体积对温度作图,均可得两条直线,相交于玻璃化转变温度点,比体积与温度的关系可用式(2-7)表示如下:
(2-7)
式中,V为任意温度时PVP的比体积;V0为0℃时的PVP的比体积;α为PVP的热膨胀系数;t为温度。
每条直线所代表的V0和膨胀系数α见表2-11。
表2-11 PVP的比体积V0、密度ρ、热膨胀系数α

Sugiura等测得三个品种的PVP的玻璃化转变温度Tg为(86±1)℃,且随着PVP中含水量的增加,Tg急剧下降,含水10%时为64℃,含水20%时为20℃。但BASF公司的F.Haaf等对玻璃化转变温度的报道与Sugiura等的结果有着很大的区别,认为PVP的玻璃化转变温度Tg随着PVP的分子量的增大而递增。在分子量达到1000000时,达到最大值在175℃左右,低分子量的PVP的Tg在100℃以下,如图2-8所示。

图2-8 玻璃转变温度与分子量的关系
另外,PVP中的水分含量对其玻璃化转变温度有着明显的影响。Sugiura和Fuji对不同含水量的PVP的玻璃化转变温度进行了研究,当PVP中的含水量增加时,玻璃化转变温度急剧下降,当含水10%时降至64℃,含水20%时降至20℃。Tan等人也系统地研究了PVP的玻璃化转变温度[16,17],随着含水量的不同,PVP的玻璃化转变温度在54~175℃变化,并推导出了PVP玻璃化转变温度与含水量的关系:
(2-8)
式中,W为体系中PVP的质量分数;W'为体系中水的质量分数;TgPVP为纯净PVP的玻璃化温度;为水的玻璃化转变温度。
从上述论述中,可以看出水含量对PVP的玻璃化转变温度有显著的降低作用,主要是因为一方面水在体系中引入了自由体积,为溶质分子链段运动提供了所需空间;另一方面,水使得聚合链间极强的氢键被破坏,减弱了分子间力,从而使分子链有更大的活动性和更有效的堆砌,使分子和分子链全部冻结所需的温度即Tg降低[18]。
PVP玻璃化转变温度较高,热塑性较差,不利于热塑性加工,这主要是由于构成PVP分子链的结构单元是强极性的,PVP分子之间存在极强的偶极间吸引力,正是强吸引力作用使得PVP分子聚集体表现为刚性而缺少柔性,加热温度达不到玻璃化转变温度时,都主要表现为玻璃态的刚脆而无法进行热塑性加工。但当温度超过玻璃化转变温度时,PVP转变为熔融态,表现出较高的熔融黏度,同样难以进行热塑性加工。如果需要对其进行热塑性加工时,只有通过共聚或增塑剂改性后进行。
2.4.4 光谱特性
Simonelli及其合作者,和Sekikawa及其合作者都对PVP的X射线衍射结构做了研究,结果所得的散射角2θ分别为10°~26°和10°~40°,这些数据都表明PVP的结构是无定形非晶态结构,这一结论在目前被较为普遍地接受。但Tadokoro及其合作者们对PVP薄膜的X射线衍射发现其结晶度为0.18。这是因为两者的检测对象有一定的区别,Tadokoro的X射线衍射对象为PVP的薄膜。而当聚合物浇注成薄膜或挤出成纤维时,通常会形成一定的微晶结构,但微晶数目很少而且相互之间无规取向,因此对物质的结晶度的提升也很微弱。
PVP的红外光谱可以通过两种方法测得,一是采用KBr压片,二是将PVP水溶液洒在AgCl圆盘上形成PVP的薄膜,然后测定。各种方法得到的PVP红外光谱大同小异,只是当PVP含杂质太多或含有可以与PVP分子发生相互作用的分子时,PVP的红外光谱可能会出现较大的偏差。另外,共聚PVP和交联PVP红外光谱,由于共聚单体的不同或者交联剂分子结构的不同而不同。均聚PVP的红外光谱如图2-9所示。

图2-9 PVP的红外光谱(KBr压片法,为10000)
由图谱可见,PVP的红外吸收峰较多,从500cm-1波数左右到3500cm-1波数都有吸收峰,其特征吸收带为—CO伸缩振动跃迁产生的谱带,这一谱带的中心位置为1660~1680cm-1,根据PVP的分子量大小等因素的变化,这一谱带的中心位置会存在不同程度的差异。另一方面,从PVP的红外谱图可以看出,—C
O伸缩振动谱带宽度约为30~35cm-1,数值偏大,说明—C
O与—C—N—酰胺键之间存在很强的作用力,相互之间发生了较强烈的耦合作用。在光谱图上,1300cm-1左右处为PVP分子的—C—N—的伸缩振动谱带,由此峰可定量推算PVP的含量。而在3000~3500cm-1的强而宽的吸收带被公认为PVP中水分的吸收峰,这类水分是被PVP分子吸附的水分。此处峰值往往超过与其临近的在2900~3000cm-1的—C—H—伸缩振动谱,这正好与具有吡咯烷酮环的其他低分子化合物如NVP、乙基吡咯烷酮等相区分,后者不具备吸收水分的性质。利用这一点可以通过红外吸收光谱来定性或半定量地判断NVP的聚合反应转化率或者PVP溶液与NVP。
PVP的紫外吸收光谱如图2-10所示。

图2-10 PVP紫外光谱图
由PVP的紫外光谱图可知,在210nm附近有PVP的最大吸收峰,在210~220nm可以得到较精密的PVP紫外光谱。当PVP的浓度小于0.002%时,其最大吸收峰移至210nm以下。另外,pH对PVP的紫外光谱有影响。这是因为在极低pH(pH<1)时,溶液为强酸性,分子中的吡咯烷酮环上的N原子带正电荷,相应地降低了羰基CO双键上的电子密度。另一方面,当pH>13时,溶液为强碱性,PVP分子的羰基转变为烯醇结构,这两种情况都会导致PVP的紫外吸收峰发生位移。
2.4.5 PVP溶解性和溶液特性
物质在不同溶剂中的溶解性与其结构有着很大的关联。PVP的分子基团中既有亲水基团,又有亲油基团,所以它可以与许多溶剂分子具有亲和力,使其既能与水互溶,又能溶解于很多的醇、羧酸、胺类、卤代烃等有机溶剂中。PVP在水中的溶解度只受溶解后形成溶液的黏度的限制,室温下PVP在其中溶解度超过10%的有机溶剂如下。
醇类:甲醇、乙醇、丙醇、异丙醇、丁醇、异丁醇、戊醇、环己醇、乙二醇、丙二醇、丁二醇、甘油。
醚类:甲基丁基醚、冠醚。
醇醚类:乙二醇醚、二甘醇、三甘醇、1,6-己二醇、聚乙二醇200、聚乙二醇400、硫醚。
羧酸类:甲酸、乙酸、丙酸、丙烯酸。
内酯类:γ-丁内酯。
酯类:乳酸乙酯、乙酸乙烯酯。
酮类:甲基环己酮、环己酮(热)。
卤代烃类:二氯甲烷、氯仿、1,2-二氯乙烷。
胺类:丙胺、正丁胺、乙二胺、环己胺、苯胺、吡啶、乙醇胺、二乙醇胺、三乙醇胺、2-氨基-2-甲基丙醇。
内酰胺类:2-吡咯烷酮、N-甲基吡咯烷酮、N-乙烯基吡咯烷酮、N-乙基吡咯烷酮。
其他:硝基甲烷、硝基乙烷。
常温下能溶解PVP,但溶解度低于1%的有机溶剂如下。
烃类:苯、甲苯、二甲苯、石油醚、戊烷、己烷、环己烷、庚烷、溶剂油、煤油、矿物油、甲基环己烷。
醚类:二乙醚、二甲醚、甲基乙烯基醚、异丁基乙烯基醚、四氢呋喃、聚乙二醇600、乙基乙烯基醚。
卤代烃类:四氯化碳、氯苯。
酮类:丙酮、2-丁酮、环己酮。
酯类:乙酸乙酯、乙酸异丁酯。
从上面列出的PVP在有机溶剂中的溶解情况可以大致得出一般性规律:PVP在极性较强的有机溶剂中溶解能力较好,相较难溶于弱极性或非极性有机溶剂中。
PVP的分子量对溶解度也有一定的影响,PVP K15、K30、K60在水、乙醇、己烷中的溶解度见表2-12。
表2-12 不同分子量PVP在不同溶剂中的溶解度 单位:mg/mL

由表2-12中数据可以看出,在水中或极性有机溶剂中PVP的溶解度远远大于在弱极性或非极性有机溶剂中的溶解度。在极性较强的有机溶剂中PVP的溶解度随分子量的增大会有一定的下降,在较低分子量下,随着分子量增大溶解度改变不明显,但随着分子量逐渐变大,对PVP在极性溶剂中的溶解度有了显著的影响。但在非极性溶剂(环己烷)中PVP的溶解度很小,而且分子量的变化对其溶解度并无显著影响。
PVP在某些混合溶剂体系中的溶解情况对于考察PVP的溶解情况和应用研究有着重要的意义。相关研究表明[19],在水/二氯甲烷混合溶剂体系中,PVP几乎全部进入水相,而PVP在这两种溶剂中的溶解度都很大,可见,PVP在水/二氯甲烷混合溶剂中水相和二氯甲烷相的分配情况并不是由它在这两种溶剂中的溶解度大小来决定的。另一方面,PVP的单体NVP在水/二氯甲烷两相混合溶剂体系中又几乎全部进入二氯甲烷相。在一些其他混合溶剂体系中PVP的分配情况也有类似的现象。在水/戊醇体系中,PVP全部进入水相,在水/苯酚体系中,PVP更多地倾向于进入苯酚相中,在丙三醇/异戊醇体系中,PVP全部进入丙三醇相。
上面讨论的是两相混合溶剂,其中至少有一种溶剂能完全溶解所加入的PVP的量,是一种理想情况。实际的情况往往不会如此简单,PVP在两相混合溶剂体系中的分配和溶解情况是随它们的组成而变化的。另外,PVP在两相溶剂体系中的溶解、分配情况随分子量的不同也会有所不同,PVP在丙酮/水两相体系组成的三相体系PVP/丙酮/水的相图如图2-11、图2-12所示。

图2-11 PVP/丙酮/水三相图(25℃)

图2-12 PVP/丙酮/水三相系统的不溶性和K值的关系
由相图可以看出,由于丙酮对PVP几乎不溶,所以随着体系中水相的减少和丙酮量的增多,PVP会逐渐随丙酮沉淀出来,形成两相,利用这一性质可以分离出溶于水中的PVP。同时,三相共溶点的位置随着K值的减小而向丙酮比例增大的方向移动,即对于某一分子量分布的PVP而言,当向其水溶液中加入丙酮时,首先沉淀进入丙酮相的是分子量较大的部分。如果已知各分子量(K值)PVP与丙酮/水两相体系的共溶点位置,就可用分级沉淀的方法分离不同分子量的PVP,进而得到PVP分子量分布情况。同样,可以通过向PVP水溶液中滴加丙酮的方式来测定PVP的K值和分子量,PVP的K值越小,出现浑浊时所需的丙酮量越大。
2.4.6 PVP溶液的流变特性
PVP在常规的应用中多数以溶液的状态存在,所以对PVP某些溶剂形成溶液后表现出来的一些特殊的性质做深入的了解和探讨研究具有很重要的实际意义。由于PVP的玻璃化转变温度较高,其熔融态黏度高且涉及化学变化,非常难以处理,故本节涉及的流变特性是指PVP溶液的流变特性,主要是指PVP溶解后形成的溶液的黏度和其在一定溶液中的增溶稳定效果。
PVP溶液的黏度与PVP的分子量、溶剂种类、溶液浓度、pH值、温度等因素有关[14,19,20],前文已经提到,通过测定PVP水溶液的相对黏度测定PVP的分子量及K值的相关原理就是依据PVP水溶液的黏度与PVP分子量之间的相互影响而达到目的的。PVP水溶液和PVP乙醇溶液黏度随浓度变化的情况如图2-13、图2-14所示。

图2-13 PVP水溶液黏度与浓度的关系

图2-14 PVP K30乙醇溶液不同浓度下黏度关系
由图中可以看出,PVP水溶液和PVP乙醇溶液的黏度随着PVP浓度的增加而增大,而且两者之间有着近乎线性的关系。对于PVP水溶液来说,随着分子量的增大,溶液黏度也增大,PVP醇溶液也有着相似的情况。不同分子量的PVP在乙醇及异丙醇中的黏度关系见表2-13。
表2-13 不同分子量PVP在醇中的黏度关系 单位:mPa·s

注:溶液中PVP的浓度为5%。
从上述图表中可以发现,不论在水中,还是在乙醇或异丙醇中,K值在30以内时,PVP溶液黏度随K值变化的幅度不太大,但当K值达到90时,PVP溶液的黏度随K值的变化幅度增大。PVP在其他有机溶剂中的黏度变化范围较大,一些溶剂溶解PVP K30后的黏度值见表2-14。
表2-14 PVP K30在不同溶剂中的黏度

在某些有机溶剂中,如丙三醇、壬基酚,PVP溶液的黏度远远大于其他溶剂中,这可能是由两方面的因素造成的:一是它们的分子极性更强,偶极矩更大,与PVP分子内酰胺基团的偶极间相互作用更为强烈;二是PVP溶于这些溶剂中并与这些溶剂混合后会发生凝胶效应,形成部分凝胶后分散于溶液中,进而大大增大了溶液的黏度。
PVP溶液的黏度除了与PVP分子量、PVP浓度及溶剂种类有关外,受温度的影响也很明显,PVP溶液的黏度随温度的变化关系如图2-15所示。
图2-15 PVP K30水溶液黏度与温度的关系
从图2-15中可以看出,不同浓度的PVP K30水溶液的黏度随温度的变化关系,基本一致,呈直线状,直线斜率为负数,说明不论浓度大小,PVP K30水溶液的黏度都随温度的升高而下降,而且溶液黏度随温度变化减低的速率不受浓度的影响。PVP水溶液的黏度随温度的升高而降低,原因在于,温度升高,分子运动更加剧烈,分子间的剪切力增大,溶液的流动性增大,从宏观上表现出来就是溶液的黏度下降。PVP其他K值水溶液也有类似的情况,如表2-15所示为PVP K90的水溶液黏度随温度的变化,只是由于分子量的增大,会不同程度的受结构黏度的影响,故而表中的数据有一定的偏差。
表2-15 PVP K90水溶液黏度与温度的关系 单位:mPa·s

一般情况下,pH对PVP溶液的黏度无显著影响,但在强酸性或者强碱性的情况下,pH对PVP溶液黏度有较大的影响。浓盐酸中,PVP溶液的黏度会明显增大,而高浓度的强碱则会使溶液中溶解的PVP沉淀出来。pH对PVP黏度的影响见表2-16。
表2-16 pH对5%PVP K30水溶液黏度的影响

2.4.7 PVP的表面活性
从PVP的单体N-乙烯基吡咯烷酮(NVP)结构单元来看,其含有一个极性较大的内酰胺基,有较强的亲和极性基团的能力,同时在其分子结构单元环内及分子主链上又有非极性的亚甲基(—CH2—),使其又具有一定的亲油性。另外,具有较大偶极矩的内酰胺基团的两端所处的环境也不相同,从其分子结构看氧原子是裸露的,而含N原子的一端则处于甲基和亚甲基的包围之中。正是这种结构,使PVP具有表面活性,虽然PVP降低表面或界面张力的能力比小分子表面活性剂小,渗透能力也相对较弱,但其对固体表面的吸附作用和亲水性能所形成的立体屏蔽能力,使PVP对固体粒子具有优良的分散稳定性。作为高分子化合物,PVP具有广泛的调节分散体或溶液流变特性的能力。此外它与许多有机、无机化合物的氢键络合能力又使其具有优良的凝聚或增溶作用,而增溶作用则广泛地应用于共沉淀制备药物固体分散剂,以提高难溶药物的生物利用率。
PVP的增溶性是PVP的一项非常重要的表面活性特性。PVP的增溶性行为主要表现为,对某一溶解度很小的物质溶于溶剂时,向溶液中加入一定量PVP,可以显著地提升该物质在溶剂中的溶解度。有研究报道[21~23],PVP对很多物质在水中的溶解度有提升,如PVP的存在,使烷基硫酸盐水溶液增溶苏丹红、OB黄等染料的能力大于醇表面活性剂烷基硫酸盐的水溶液,其中对OB黄的增溶效果从表面活性剂加入就起到一定效果。碘在水中的溶解度为0.034%,而在PVP的水溶液中碘的溶解度增加到0.58%,提高了数十倍。
正是以上这些表面活性的综合特性使PVP成为高分子表面活性剂的主要品种之一。
2.4.8 PVP的成膜性、吸水性及相容性
PVP的另一个非常重要的性质是它的成膜性,PVP可以从水、甲醇、乙醇、氯仿或者二氯甲烷的溶液中浇注或涂布成膜。PVP的薄膜是无色透明的,硬而光亮,由于PVP膜是通过溶液浇注或涂布而成,克服了固体PVP塑性差的不足。PVP薄膜可以根据涂布物任意成型,溶剂对形成的PVP膜无影响,利用PVP的成膜性可以用于很多方面。
PVP具有很强的吸湿能力,但其吸湿性较CMC弱,较PVA要强。PVP在空气中的吸水率与空气的相对湿度有关,其在不同相对湿度下的吸水率如图2-16所示。

图2-16 PVP在不同相对湿度的空气中吸水曲线
从PVP在不同湿度下的吸水曲线可以看出,PVP在空气中的吸水率随着相对湿度的增大而增大,当PVP薄膜吸水达到一定程度(从相对湿度大于70%的空气中吸收水分)时,就会有一定的黏性。PVP吸湿平衡后水分含量大约为相对湿度的三分之一。热化学研究表明,每一个NVP结构单元大约可缔合0.5mol分子的水分,这与蛋白质的吸水性相似。作为商品储存的PVP,随着储存时间的延长而逐渐从大气中吸收水分,其水分含量往往会超过质量标准的要求(一般小于5%),所以应注意把PVP商品储存在干燥的环境中,并尽量使之密封保存,尤其是使用者应注意,不用时要密封保存好。
图2-17是PVP和PVP/VA在不同相对湿度下的吸水率。由图中曲线可以看出,PVP与疏水单元VA共聚产物的吸水能力大约是均聚PVP的三分之一。PVP不仅具有较强的吸水性,还有良好的保湿性,而且在实际应用中PVP的保湿性比吸水性显得更重要,如利用PVP的保湿性,将其用于高级化妆品中,特别是用在摩丝中可赋予其良好的保湿性,使头发显得柔顺亮泽。

图2-17 PVP与PVP/VA共聚物的吸水率曲线
PVP作为一种功能性高分子精细化学品,大多数情况下是作为助剂和辅料,很少单独使用,而且往往与其他化学物质配合使用。因此,无论PVP是以固体还是溶液形式使用,PVP与其共同使用的物质的相容性或者相溶性是非常重要的。
本文所说的相溶性是指PVP在其他有机溶剂中的溶解性,而相容性是指PVP与其他化学物质同时使用时有利于其他物质的使用性能的协调和改善,或者至少不会抑制其他物质发挥应有的功能,也不会相互发生反应以致使某一方失去应有的功能。相容性包括相溶性,因为PVP溶液具有很多固体PVP不具有的功能和性质,其中一个比较明显的特征就是PVP溶液可以任何形态成膜,而PVP固体粉末无论怎么样处理也难以成膜。但是相容性又有别于相溶性,例如PVP不溶于某些表面活性剂,不具有相溶性,但可以与其他物质一起形成均一的乳状物而用于化妆品中,所以与这样的表面活性剂已具有相容性。
PVP用于不同的用途时,对其使用时的形态要求也不同,如作为增稠剂或胶体保护剂,一般要求使用时要配制成均匀的溶液;作为染发剂、定发剂或药物的包衣时,则要求能形成良好的无黏性的膜。加入某些天然或合成的高分子聚合物或者有机化合物可以有效地调节PVP膜的吸湿性和柔软性而不影响膜的光泽性和透明度。也可以通过加入一些物质来减少或增大PVP的吸湿性进而达到控制PVP黏度的目的,可以作为黏度控制剂加入PVP中的物质有羧甲基纤维素、羟甲基纤维素、乙酸纤维素、乙酸丙酸纤维素、虫胶、邻苯二甲酸二甲酯、乙二醇、甘油、二乙二醇、山梨醇、聚乙二醇400、尿素等。其中,前5种化合物可以减少PVP的黏性作用,后面几种对PVP的黏性有提升效果。加入10%某磺酰胺-甲醛树脂可以使PVP在空气中基本无黏性。
有时需要PVP薄膜具有一定的弹性,而通常PVP膜多表现出硬而脆的特性,此时可以加入增塑剂来提升其可塑性,效果较好的增塑剂有10%二乙二醇、10%甘油、10%聚乙二醇400、25%山梨醇、25%邻苯二甲酸二甲酯,适当的含水量也是一种增塑剂。在实际使用中,往往需要同时加入两种或者两种以上的增塑剂才能得到满意的效果。在PVP用于固发胶时,羊毛脂衍生物是比较有效的增塑剂和黏度控制剂。
PVP与大部分无机盐、许多天然或合成树脂以及表面活性剂都有很好的相容性,见表2-17。
表2-17 PVP与一些化合物的相容性

与PVP相容性好的化合物,能在一定溶剂和浓度下,形成透明澄清的溶液(或有浅色),用其浇注的薄膜也是均匀透明的。在这些聚合物和大分子中,有聚乙二醇、乙酸纤维素、EVA、聚丙烯腈、PVC、PVA、聚乙烯醇缩甲醛、聚乙烯醇缩丁醛、甲基纤维素、乙基纤维素、羧甲基纤维素、虫胶、松香树脂、鹿角胶、海藻酸钠、糊精、蜂蜡、羊毛脂等。在表面活性剂中有:十二烷基硫酸钠、烷基磺酸酯、烷基酚聚氧乙烯醚硫酸铵、十二烷基苯磺酸钠,以及几乎全部阳离子表面活性剂。还有一些化合物可以在低浓度溶液中与PVP互溶,但成膜后却不能成为均匀的薄膜。
2.4.9 络合性
物质结构决定物质的性质,PVP特殊的分子组成和结构赋予了它很多的优良性能,其中络合特性就是其中较鲜明的性能之一。PVP分子结构具有强极性和能接受氢键的酰胺基团,这使它能结合一些极性小分子,同时,PVP分子内的O原子、N原子是典型的配位原子,使其具有与许多物质生成络合物的能力,特别是含羟基、羧基、氨基及其他活性氢原子的化合物生成固态络合物,如碘、β-胡萝卜素、甲基磺丁脲、苯妥英、阿吗啉、利血平及多种磺胺类药物。
相关研究表明,这些络合物实质上是无定形的,是小分子组分以分子状态分散于聚合物的无定形基体之中,它们因此也可以被称为无定形固体络合物或无定形固体溶液。
与PVP发生络合作用的小分子物质热力学活性降低,相应地提高了其热力学稳定性。例如碘在通常情况下是很容易升华挥发的物质,而碘与PVP络合后,其挥发性降低到其蒸气压几乎忽略的程度,同时也不会被氯仿等有机溶剂萃取。并且由于这些物质以分子状态分散,其溶解比结晶状态容易得多,进而很大程度上增加了它们的溶解性。如后文中要介绍到的PVP-碘是碘从不溶于水变成完全的水溶状态。因此,络合性使得PVP得到更为广泛的应用,尤其是在医疗卫生领域,许多不溶性药物在与PVP络合后成为可溶性药物。
另一方面,与PVP络合形成的另外一些络合物因分子量进一步增大,或络合作用较强,以致在中性或酸性条件下沉淀。例如,PVP水溶液与某些多元酸,如聚丙烯酸、单宁酸及甲基乙烯基醚与马来酸的共聚物形成不溶性络合物,进而可达到分离或者除去这些物质的目的。这些沉淀虽不溶于于水,但用碱中和后,络合反应逆向进行,质谱研究表明它们是氢键络合物,与蛋白质的络合性质很相似。PVP与酚类物质形成的络合物也有类似的情况,通常不溶于水。
某些染料特别是直接染料、酸性染料、硫化染料也能与PVP结合,使PVP可作为剥色剂和防染剂。
近年来,PVP与金属形成络合物的研究越来越受到关注,PVP与许多金属都能形成固体络合物,其中对过渡金属和重金属的研究较多,如PVP与Fe、Mn、Co、Ni等过渡金属均可生成络合物。这些络合物是由PVP与相应的金属羰基化合物[M(CO)x]反应而获得的,例如PVP与Fe(CO)5反应生产Fe(C6H9NO)5,说明反应过程是PVP分子链上的羰基取代Fe(CO)5中的全部5个配价羰基。
2.4.10 化学稳定性
在通常情况下,固体PVP很稳定,在100℃的空气中加热16h无变化。若在空气中加热至150℃,或者在有引发剂(过硫酸钾、过硫酸铵等)的情况下加热到90℃,则可能发生自交联反应,转变为不溶性的交联PVP。在有偶氮类化合物、氧化剂如过氧化氢、重铬酸盐存在时,用紫外线、γ射线照射PVP,则交联成为稳定的凝胶。
另一方面,长时间的研磨会导致PVP降解,PVP K90在氮气气氛中研磨100h后,平均分子量从1000000下降到400000~450000,200h后,下降至100000左右,PVP分子量下降速率与研磨时间的关系如下式。
氮气气氛:
(2-9)
空气气氛:
(2-10)
式中,M为PVP的分子量;t为研磨时间,h。
PVP的水溶液在通常情况下也很稳定,若不含其他杂质,PVP水溶液加热到100℃均无明显的变化,但温度继续升高并加热一定的时间,会使PVP溶液变成轻微的淡黄色,而且随着PVP浓度的增高,随加热温度的升高和加热时间的延长,会发生沉淀现象。这是由于PVP溶液在加热的条件下发生了自交联反应而生产了交联或高分子量PVP,因为PVP的溶解度是随分子量的增大而减小的。另外,在PVP水溶液中加入某些含多价阴离子的盐类(如偏硅酸钠、三聚磷酸钠等),也会发生沉淀现象。
酸碱性对PVP稳定性也有影响,尤其是对于PVP水溶液更为明显,在明显的酸性或碱性条件下加热PVP水溶液,部分吡啶烷酮环会开环破坏PVP的分子结构,如在碱性条件下,发生如下的变化:
因此,对PVP产品的pH有严格的要求,一般都在3~7。同时,在常温长期存放的高分子量PVP,也会有一定的降解现象。对于粉末状的PVP K30在通常存放条件下,质量稳定期不超过两年;PVP K90不超过一年;PVP的水溶液稳定期限则更短。
2.4.11 生理安全性
PVP最早被发现是由于它是优良的人造血浆增溶剂,迄今为止,PVP在医药及医疗卫生领域的应用一直是优异性能的重要体现,因此PVP对人体及其他生物的生理安全性的研究就具有十分重要的意义。
PVP具有良好的生理惰性,不参与人体新陈代谢,同时又具有良好的生物相容性,对皮肤、黏膜、眼等部位和器官不形成任何明显的刺激。从生物学观点来看,PVP的分子结构中的酰胺基团类似于简单的蛋白质模型分子中的氨基酸官能团,使得它的一些性质与蛋白质相似,例如水溶性、对某些小分子物质的络合能力以及能被一些蛋白质沉淀剂如硫酸铵、单宁酸和酚类所沉淀,PVP水溶液加热会形成沉淀的性质也类似于蛋白质的变性。也正是这些性质,使PVP具有良好的生理惰性和相容性,使其广泛应用于医药及医疗卫生领域等方面。
PVP用于医药辅料尤其是用作注射剂直接进入人体血液的场合时,分子量的大小是一个重要的因素。一方面PVP分子量过大会导致在人体内溶解不完全,发生沉积,积蓄在人体内;另一方面,PVP在水溶液中不像蛋白质那样保持原有的紧密结构,而是像通常具有柔性链的聚合物那样在水中以散乱的螺圈构型存在,这种螺圈的尺寸依赖于分子量。PVP的分子量达到一定数值,即使在人体内完全溶解,但在经过人体肾脏排除时,也会因为不能通过人体肾脏毛细管排放而沉积在肾脏内。人体肾脏毛细管的内径约为7nm,也就是进入人体血液循环的PVP的分子尺寸应小于这个数值,与此相应的PVP分子量小于30000时才能顺利地经肾小管排出体外。生理盐水中PVP的尺寸、分子量、K值与通过毛细血管的情况如图2-18所示。另外,由于PVP是游离基均聚的产物,其分子量分布遵循Schulg-Flory分布,为了保证作为注射剂的PVP不含分子量大于30000以上的组分,其平均分子量需更小一些,大约在25000。
图2-18 生理盐水中PVP的分子尺寸与K值、分子量的关系
PVP具有优良的生理惰性及生物相容性,故而广泛地应用于食品、化妆品和医药产业中,在医药工业中主要作为医药辅料使用。对所有的应用方式,其急性毒性都是较低的,在正常剂量下长期用药,也未发生有影响的组织损坏。PVP对皮肤、眼睛无刺激或过敏。对人不具有抗原性,也不抑制抗体的生成,人体可从消化道、腹下、皮下及静脉途经接受,未发现对人有任何的致癌作用。PVP不被肠道吸收。在非肠胃医药中低分子量的PVP很容易从肾系统排出,而高分子量PVP排出较慢。
(1)口服毒性 选用健康的天竺鼠和小鼠采用100g/kg的剂量给药,观察2周而无反应。对于大鼠,用分子量为30000的PVP给药,观察7d,测定LD0>25g/kg。
不同分子量的PVP的急性口服毒性结果无显著差别,见表2-18。
表2-18 不同分子量PVP急性口服毒性结果

实验表明,PVP的急性口服及腹腔注射LD50>10000mg/kg,属于实际无毒级。药理研究证明,PVP对中枢神经系统、呼吸系统、血液循环系统都无影响。
积蓄毒性:选用NIH纯种健康小鼠进行积蓄毒性实验。按剂量递增法经口染毒,实验动物食欲正常,无其他明显反应,连续染毒20d,实验动物死亡未达半数,染毒总剂量已达一次LD50的5倍以上,即积蓄系数大于5,按积蓄系数评价标准,PVP属于弱积蓄毒性级。
对人体进行临床口服实验表明,一次给药3~50g都没有发现组织损伤。
联合国世界粮药组织和世界卫生组织食品添加剂联合专家委员会在1983年第27次会议上,暂时规定PVP的ADI值(每日摄入量)为0~25mg/kg。
(2)皮肤刺激性 在进行皮肤刺激性实验时,选用健康的成年豚鼠为实验对象,按GB 7919—1987《化妆品安全性评价程序和方法》中规定的多次皮肤刺激实验方法进行。实验表明,实验侧与对照侧皮肤比较未见异常反应,多次皮肤刺激实验刺激为0,按评价标准评定PVP对皮肤无明显刺激性。
(3)非肠胃道毒性 对中等分子量以下的PVP进行静脉注射途经的急性毒性实验,实验结果如下:
兔子 LD>1g/kg
大鼠 LD>15g/kg
由于具有良好的局部相容性,非肠胃道给药没有发现有中毒迹象,小分子量的PVP几天内便可以完全从尿液中排除。较高分子量的PVP在体内缓慢地积蓄,主要在网状内皮组织细胞内,特别是在脾、肝、淋巴结、骨髓及肾中暂时贮积,但是这种贮积并没有造成受试动物组织形态或功能上的损坏或伤害作用。做肠胃道给药的研究证明,PVP无致癌作用,部分实验甚至观察到PVP有一定的抑制肿瘤作用。
(4)吸入毒性 由于PVP及其共聚物在化妆品中的应用不断扩大,吸入毒性的研究显得比较重要。大量的动物和临床实验证明,没有发现PVP对肺部造成病理变化。美国FDA宣布,含有PVP的气溶胶型的喷发胶,在正常使用下没有损害健康的危险性。
2.5 应用
PVP具有诸多优良的物理化学性质,使其在问世70多年来在医药、化妆品、日化、食品、饮料、保健品、生物工程材料、水处理材料等许多与人类健康密切相关的行业领域得到广泛的研究和应用。此外,PVP由于具有水溶性好、安全无毒,能与多种高分子、低分子互溶或者络合,并且具有优良的吸附性、成膜性、黏结性以及热稳定性等特性,在全球提倡绿色环保的大背景下,PVP在传统行业如纺织印染、涂料、颜料、造纸、电子、能源等领域也有新的应用和发展;在新材料领域如膜分离、纳米材料制备、光伏电池、高吸水性接触镜片、智能传感器、3D打印、喷印墨水等产品中的应用研究正方兴未艾。
2.5.1 在医药中的应用
PVP最早于20世纪30年代被用于血浆增溶剂使用而被发明,在医药医疗领域中使用至今,已有70多年的历史,是迄今为止应用最为广泛的领域。利用PVP良好的溶解性、增溶性、生理相容性、黏结能力及络合能力等性能,在医药医疗卫生领域中,可用作黏结剂、赋形剂、包衣剂、崩解剂、助溶剂、杀菌消毒剂、增溶剂、缓释剂、胶囊外壳、分散稳定剂、成膜剂等。PVP在医药医疗卫生领域的应用异常活跃,发展至今,它与纤维素类衍生物、丙烯酸类化合物一起成为当今三大主要合成药物辅料,在全世界范围内得到广泛的应用。作为药用辅料,PVP已经广泛收载于中国、美国、欧洲、日本、英国、德国、印度等国家和地区的药典中,几乎被世界各国卫生行政部门所接受。不同型号及不同分子量的PVP产品在各国家和地区药典的情况见表2-19。
表2-19 不同规格PVP收载于国家药典的情况

注:“+”表示有收载,“-”表示未收载。
第二次世界大战期间用于血浆增溶剂的PVP产品商品名为“Periston”,其组成为3.5%的PVP(分子量为25000~30000)等渗盐水,经静脉注射可起血浆增溶的作用,对于治疗急性大量失血或者烧伤性休克有显著作用,并且与受药者的血型无关。曾在第二次世界大战的战场上抢救了超过20万的生命,后来其他欧美国家也纷纷采用。“Periston”的配方如下[24]:
其制备方法:先将20%PVP加入70kg的50℃蒸馏水,然后依次投入盐酸盐,溶解;再将Na2CO3溶解于6~7L蒸馏水中后慢慢加入到盐酸中,待CO2完全逸出后,将此溶液加入到PVP与盐酸盐的溶液中;在消毒条件下,将上述混合液加入到剩余的蒸馏水中稀释成含3.5%PVP的制剂溶液;最后将上述溶液用经蒸汽消毒过的过滤器过滤,装瓶后在100~120℃下消毒,在35℃下存放3周,如无沉淀析出则可供临床使用。
在第二次世界大战末期,大约有超过100万的病人接受了PVP等渗盐水的治疗,没有造成对人体损害的副作用。在朝鲜战争中,PVP等渗盐水仍然被美国作为紧急状态下的血浆增溶剂。近年来,作为血浆增溶剂,PVP已经被羟乙基淀粉、右旋糖酐、缩合葡萄糖、琥珀明胶等替代。但是由于PVP的优异性能,自20世纪60年代开始,它在医药其他方面的应用异常活跃。到目前为止,全世界约发表1万余篇有关应用研究的专利及文献,且继续以每年数百篇的速度增加,显示了人们对于PVP的浓厚兴趣。在一些发达国家,如美国、德国、日本等,PVP在医药卫生领域的应用约占PVP消费总量的40%~55%。
PVP在我国是20世纪80年代开始应用于药物生产的。1985年浙江化工研究院与杭州民生制药厂合作研发出新型杀菌消毒剂PVP-I,并于1987年顺利投产,其后PVP-I在国内得到持续开发和应用;1988年前后,上海施宝贵制药公司、无锡华瑞制药厂、西安杨森制药公司等均采用进口PVP作辅料生产片剂;1992年浙江省化工研究院与河南焦作开源药厂合作研制PVP;1995年3月,原国家卫生部正式批准聚维酮K30(PVP K30)为新辅料,并颁发了新药证书和生产批准文号,从此国产药用级PVP的生产、供应成为现实,国内PVP在药物制剂中的应用研究和新产品开发日趋活跃。目前PVP在医药医疗卫生领域中的用量及作用见表2-20。
表2-20 PVP在医药中的应用

在药用辅料方面,PVP的功能主要是:作为难溶药物的共沉淀剂,注射剂的助溶剂、分散稳定剂,片剂、颗粒剂的黏结剂,包衣成膜剂,药物延效剂、缓释剂,胶囊助流剂,眼药助剂,药物崩解剂,缓控释剂等,分别介绍如下。
(1)共沉淀剂 有许多疗效好的药物,由于在水中的溶解度很小,致使其生物利用度降低。提高这类微溶、不溶于水药物的溶解度和溶出速度是药剂研究和生产必须解决的问题。
采用某些水溶性载体与药物共沉淀,可以提高药物的溶解度和溶出速度,提高疗效,减小使用剂量。这种共沉淀物是高分子(载体)对小分子(客体)的包合物,是一定形状、大小合适的小分子药物填充于一定形状、大小和结构的大分子(多为聚合物)空间而形成的“固溶体”。
PVP可作为药物共沉淀剂的主要原因是利用PVP分子中的羰基O与难溶药物分子的活泼氢原子以氢键结合在一起,药物分子成为无定形的状态进入PVP大分子,并且不会改变PVP易溶于水的性质,从而抑制了难溶或不溶药物分子的结晶的生成和生长,而成为过饱和状态,从而大大提高了难溶或不溶药物的溶解度。PVP作为药物共沉淀剂的研究始于19世纪60年代,Tachibana首先报道了用PVP制备β-胡萝卜素水分散液,以提高β-胡萝卜素的溶解速度。随后灰黄霉素、利血平等药物与PVP的共沉淀物提高溶解度、溶解速度、吸收速度的研究报道屡见于文献。
难溶药物在人体内溶解度的提高也相应地提高了药物的生物利用率。例如苯妥英是一种微溶药物,通常不能达到有效的血液浓度(10~15μg/mL)但当与PVP形成1∶5的共沉淀物后,在pH=1.2的溶解介质中其浓度提高了2.3倍,在服用后不到2h就可以达到有效的血液浓度,而且其可达到的最大血液浓度也提高了2倍以上。
改变PVP与药物的质量比可以调节共沉淀物的药物溶解速率。利血平的溶解速度受其晶体粒度的影响很大,当使用PVP与其共沉淀时,可以使粒径变得更小,从而增大其溶解度和溶解速率。而且PVP的比例越大,越有利于利血平的溶解,1∶3的共沉淀物与1∶6的共沉淀物的溶解速率分别是利血平的15倍和200倍,其溶解半衰期则分别为7min、0.5min和106min。PVP与甲氧苄氨嘧啶(TMP)的共沉淀可以提高TMP的溶出速度,实验表明,PVP∶TMP为3∶1的共沉淀物溶出最快。吲哚类生物碱阿吗啉在水中30℃时的溶解速率常数为0.023min-1,但是与PVP形成1∶5的共沉淀物后不但在10min内使其溶解度提高38倍,而且其溶解速率常数提高了130倍,达到了2.99min-1。乙酸环己脲与PVP的共沉淀体系中,必须使PVP的含量达到70%以上时才能保证其无定形分散,达到快速溶解的目的,否则该药物会形成结晶,使其溶解速率降低。
改变PVP的聚合度也可调节共沉淀物的药物溶解速率。一般来说,当PVP的聚合度增大时,药物溶出速率下降。例如以苯乙烯(ST)、磺胺甲恶唑(SMZ)和磺胺异恶唑(SIZ)分别与PVP K15、PVP K30、PVP K90形成共沉淀物,他们的溶出速度V遵循VK15<VK30<VK90的规律。此外,双氢氯噻嗪、磺胺噻唑、氯霉素、地高辛、氯噻嗪、氢化可的松、泼尼松等与PVP形成的共沉淀物也遵循此规律,而硝苯吡啶和苯妥英则是例外。
PVP与某些难溶药物共沉淀物的药物代谢动力学实验结果见表2-21。
表2-21 PVP与难溶药物共沉淀物的药代动力学实验结果

在制药工业上,固溶物的制备通常采用混合物熔融挤出、混合工研磨、共沉淀、载体表面制粒或者是喷雾包埋等方法实现。利用PVP的作为共沉淀剂,可以发展一系列新的高效口服药剂。通常使用PVP K25和PVP K30作为共沉淀剂。
(2)助溶剂或分散稳定剂 低分子量的PVP(K值为12、15、17)可在注射液中作为助溶剂或者结晶生长抑制剂,这种助溶作用主要是药物和PVP的缔合作用产生的。
如文献[25]报道了用PVP K12为增溶剂制备磺胺/甲氧苄啶针剂的配方(pH=7):
针剂或者液体制剂中采用PVP作助溶剂或者分散稳定剂的还有:土霉素、睾酮、黄体酮、磺胺噻唑、强力霉素、呋喃它酮、己烯雌酚、脱脂大豆卵磷脂、别嘌呤醇、二苯基海因、环己烷氨磺酸盐等。
在口服或者外用药物制剂中,PVP起助溶和分散稳定剂的例子也很多。例如用PVP K25增溶制备扑热息痛糖浆,可减轻其苦味;PVP可提高蛋白酶的稳定性,防止口服液中糖类从液体中结晶析出。
在粉针剂中,美国默克、夏谱、陶氏公司的利福平,辉瑞公司的强力霉素都加入PVP。此外,在一些药物如布洛芬、苯妥英、甲氧苄啶、磺胺类以及抗生素类药物中通常也加入PVP作为分散稳定剂。
(3)黏结剂 药物片剂应有一定的机械强度以使其经受住在生产、运输、分装过程中碰撞、摩擦时不致破碎;同时,在服用后还需要迅速在消化道中崩解,释放药物。解决这一问题的关键就是要选择理想的黏结剂。由于PVP人体相容性好、无毒、黏结能力强、溶解性好,无论是湿法制粒后压片,还是干法制粒后压片或者直接压片工艺,PVP都能够满足以上两点要求,因此,目前已为各种药品片剂的生产所采用。PVP在片剂中的用量一般为1%~5%,使用浓度一般为0.5%~5%。由于PVP具有优异的水溶性,也可以溶解于乙醇等有机溶剂中,因此在绝大多数处方中都适用,特别是对于一些热敏、水敏及易挥发药物,利用PVP的醇溶液造粒,既解决了稳定性问题,保证了药品质量,又降低了干燥温度,缩短了干燥时间,提高生产效率。这方面的典型例子,如阿司匹林(achidum acetylsalicylicum)、氯地黄体酮(chlormadinone acetate)、硝酸甘油(nitroglycerinum)等。
如硝酸甘油舌下含片采用如下配方[26]:
按照上述配方制成的颗粒压片,片重差异小,组成均匀,药物溶出快,因而药效快。
又如一种阿司匹林片,以PVP K30作黏结剂效果良好,其配方为:
又如一种口腔用复方止痛咀嚼片,以PVP的50%乙醇溶液作黏结剂,其配方为:
采用PVP与淀粉、羟丙基纤维素、蔗糖、微粉硅胶、羟丙基甲基纤维素、乙基纤维素等可制成用于直接压片的黏合剂浆料,但是要注意水分含量,避免水分含量过高而导致黏结力过大,造成粘冲等使压片难以进行。此外,也常用聚乙二醇、木糖醇、甘露醇等作为增塑剂以提高压片效果及药片的机械强度。
在泡腾片的制备中,PVP的应用也得到广大制药研究者的重视。泡腾片是含有碳酸氢钠和柠檬酸(也可用酒石酸等)作为主要泡腾剂的一类片剂,制备过程中不允许水分存在,但使用性上又要求应用水溶性的黏结剂,因此既溶于无水乙醇又溶于水的PVP就成了理想的黏结剂之一。
一种午时茶泡腾片,以PVP作为黏结剂制备,其配方为:
又如一种扑热息痛泡腾片[27],以PVP K25作为黏结剂制备,其配方为:
用PVP作黏结剂制备泡腾片,具有可压性好、药片崩解溶解迅速、发泡作用强烈等优点。此外,在PVP基础上还开发出了PVP/VA共聚物,其继承了PVP的优良黏结性、可压性,同时又克服了PVP易吸潮的缺点,是目前制备泡腾片的最佳黏结剂,其使用量一般为2%~5%,使用浓度为5%~10%。
PVP溶液黏度低,易喷雾,因此也尤其适合于喷雾造粒、流化床造粒,能够快速生成硬度高且无粉尘、粒度均匀的颗粒。在喷雾造粒时可先将干组分与PVP粉混合,再喷入其他液体组分;也可先制成PVP与其他组分的悬浮液,再进行喷雾干燥。这两种方式可以根据具体药物的特性,进行选择使用,最后得到可以直接用于压片的颗粒。
国外用PVP作黏结剂的片剂品种很多,常用的有:阿司匹林、复方阿司匹林、阿司匹林VC泡腾片、扑热息痛、羟基保泰松、萘普生、维生素C、维生素B、复合维生素、二甲基四环素、青霉素V、头孢立新、心得舒、心得静、心得平、胰酶、己酮可可碱、潘生丁、胺碘酮、咪康唑、信地米松、氯地黄体酮、复方泼尼松、二氯苯胺苯乙酸、复方硫酸亚铁、延效苯螺旋酮、苯磺酰胺、异搏定、阿米替林、复方茶碱等。
下面根据制备片剂方式不同,分为直接压片和干法制粒压片以及湿法制粒压片两个方面来具体介绍PVP作为药物片剂制备用黏结剂。
①直接压片和干法制粒黏合剂。粉末直接压片以及干法制粒后压片具有较明显的优点,如工艺过程简单,不必干燥,产品崩解或者溶出快,产品质量稳定,在国外已经有约40%的片剂采用此方法生产。
许多药物对湿、热不稳定,如头孢克肟遇湿、热易变色,效价降低;维生素C具有还原性,易被空气氧化,以致颜色变黄,含量下降,特别是受水分、温度和金属离子影响时,更易变质;氨茶碱遇湿、热均易分解、变色,放出强烈氨臭;利福平对湿、热也不稳定,含量下降,溶出度不合格;盐酸甲氯芬酯极易水解。这些药物若采用常规的湿法制粒,在生产过程中与黏合剂中的溶剂成分接触,并经高温干燥,必然会对产品质量产生影响。而采用粉末直接压片或者干法制粒后压片工艺,所制得的片剂表面光滑,无裂片和粘冲,片重差异小,溶出快,稳定性好。
直接压片以及干法制粒后压片制备药物片剂的关键是选择合适的干黏结剂。干黏结剂通常是由可压性较好的填充剂或者填充黏结剂组成。干黏合剂不但能改善活性成分的黏合能力,还在一定程度上起着崩解剂的作用。特别需要注意的是,在直接压片时黏合剂必须磨细并且需要具有特别优越的流动性,以确保分散较为理想。
在PVP基础上发展而来的共聚维酮PVP/VA64是直接压片和干法制粒工艺中高效的干黏合剂。其具有流动性好、玻璃化转变温度低等优良性能,使得它能与片剂中其他组分混合得非常均匀,受挤压时能够与其他相邻颗粒黏结在一起。并且在受压过程中还能产生良好的塑性形变,所得的片剂和颗粒无回复应力,因此具有长期的稳定性。
以用PVP/VA64作干黏合剂直接压片制备氢氯噻嗪片为例说明。黏合剂PVP/VA64的不同加入量对片剂质量的影响如图2-19所示。

图2-19 氢氯噻嗪直接压片配方中PVP/VA64的作用
由图2-19可见,在压片力一定时,随着配方中PVP/VA64加入量的增加,所制备的药片的硬度增大。因此,加入PVP/VA作黏合剂使直接压片制备氢氯噻嗪片剂更容易。
表2-22为用作干黏合剂的PVP/VA64的特点及其优点的介绍。
表2-22 用作干黏合剂的PVP/VA64的特点及优点

②湿法制粒黏合剂。湿法制粒黏合剂使处方具有“黏合性”,从而改善它的可压性和流动性。对片剂的物理性能、生物利用度和疗效都具有重要的作用。PVP系列产品是湿法制粒的首选高效黏合剂,PVP K25、PVP K30、PVP K90以及PVP/VA64等都可用于湿法制粒的黏合剂。其中,尤其以PVP K30最为通用,因其黏度低(其典型黏度为2.5mPa·s),使用方便,在水及所有经批准的药用溶剂中均易溶解。表2-23概括了PVP K30用作湿法制粒黏合剂的主要优点。
表2-23 PVP K30用作湿法制粒黏合剂的特点及优点

在多数情况下,如果需要较强的颗粒和片剂或者处方有脆碎和裂片的倾向时均可增加PVP K30的用量增加黏合力。在增加PVP K30用量黏合力仍不足的情况下,可使用分子量更大的PVP K90达到更强的黏合效果,但是重要的是要注意黏度会相应增大(见图2-20)。当需要黏合剂量较多及工艺条件限制所用的黏合黏度时,PVP K25更具优越性。虽然其分子量较低,但并没有显著影响其黏合能力(见图2-21)。

图2-20 PVP K90和PVP K30的黏度与浓度关系
(注:用Brookfield LVT黏度计,以60r/min与25℃测定)

图2-21 各含5%PVP K25或PVP K30乳糖空白片硬度与压力的关系
③黏合剂的选择。黏合剂的选择需要结合制备颗粒或者药片的工艺条件,以及片剂的性能要求进行。一般情况下,可以按照图2-22中的步骤进行筛选。

图2-22 黏合剂的选择流程
(4)包衣成膜剂 PVP具有优良的黏结性、分散性以及成膜性,可以增强包衣对药物基材的黏着力;增加包衣悬浮液的稳定性,以避免色素的重聚和迁移;还可以防止药膜包衣在干燥过程中以及干燥环境中长久储存而产生裂纹或者破碎。因此经常被用作固体药物的包衣成膜原料。一般被用来作为包衣成膜剂的PVP产品主要是PVP K25、PVP K30以及PVP/VA64这几类。需要注意的是,PVP K25、PVP K30具有易吸湿性,包衣时易产生黏结现象,成膜后也有吸湿软化的倾向,因此不能作为单一的包衣成膜剂使用,而应与纤维素醚类、丙烯酸树脂类成膜剂配合使用。此外,与聚乙二醇600合用可以增加弹性,加入适量的乙酰单甘油酸酯可以适当减小吸湿性。
很多包衣制剂需要加入色素来改善制剂的颜色,为了提升色素的分散效果,通常可以用虫胶和PVP来制备色素分散液,在喷雾和流化床涂膜设备中可以得到色泽均匀的涂层。如EudragitL30D-55肠溶包衣水分散液中,用PVP作色素分散剂,可以有效地防止分散相的聚集沉淀,避免色素迁移,使着色均匀。又如,借助于PVP的良好醇溶性,可以用10%PVP醇溶液作为水敏性片芯的内涂层。
下面举例介绍用PVP改进制备的药膜包衣液配方。
①一种有色包衣液配方。
制备时,首先将甲组分与乙组分混合调浆研磨,然后在搅拌下加入剩余的甲组分,即可得到色素包衣悬浮液。
②无色包衣液配方。
由于PVP/VA64继承了PVP的一些优良的性质,比如溶解性、成膜性等,而且其玻璃化转变温度比PVP K30低,吸湿性小,因此近年来,PVP/VA64在作为成膜剂使用的功能性添加剂中的应用越来越得到重视。例如在低黏度的HPMC膜中加入PVP/VA64,可以提高HPMC膜的塑性,增加膜的弹性和它与片芯的黏合性。且增加PVP/VA64的用量,还能达到改善物理性质的同时增加包膜光泽的效果。PVP/VA64作为成膜剂添加使用的良好性能总结见表2-24。
表2-24 用作成膜剂的PVP/VA64的特点及性能

不同相对湿度条件下,PVP K30和PVP/VA64的吸湿性比较如图2-23所示。从图中可以看出,后者的吸湿性更小,因而使膜更富有弹性,储存期内也更为稳定。

图2-23 PVP K30和PVP/VA64的吸湿性比较
(5)延效剂、缓释剂 药物的可控释放是延长药物的作用时间、控制药物的作用强度的技术。PVP由于具有独特的生物相容性、无毒性、生物活性以及络合性,可与很多药物分子间产生缔合作用,因此被广泛地作为新型药物载体应用在缓释给药系统中。PVP的分子量及使用浓度可以影响其对药物分子的缔合程度,进而影响药物的延效和缓释效率。例如,通过研究PVP对扑热息痛的延效缓释作用发现,扑热息痛的溶解随溶液黏度的增大减少,PVP的分子量和浓度都会影响溶液的黏度。采用PVP K17、K30、K90分别制备1∶9的扑热息痛分散体,PVP K17的溶解速度最快,而PVP K90的溶解速度最慢。
有关研究指出,利用辐射聚合制备的两亲性马来酸化邻苯二甲酰化壳聚糖-PVP对油溶性药物吲哚美辛具有良好的负载作用,且随着两亲性马来酸化邻苯二甲酰化壳聚糖-PVP浓度的增加,吲哚美辛的负载量增大,最后趋于稳定;药物在聚合物载体中的释放明显慢于纯药物的释放。
PVP能够降低胆固醇的溶解性,且降低值与PVP的浓度成正比;而对于激素类药物如睾丸甾酮、孕甾酮、二乙胺己烯雌酚等,随着PVP浓度的增加,其溶解性增加。
除了对上述药物具有延效、缓释作用外,PVP溶液对青霉素、胰岛素、可的松、氯霉素、水杨酸钠、对氨基苯甲酸、普鲁卡因、苯巴比妥、磺胺噻唑等都有延效作用。
(6)胶囊助流剂 胶囊剂可掩盖药物的不良气味,易于吞服;能提高药物的稳定性及生物利用度;还能定时定位释放药物,并能弥补其他固体剂型的不足,应用广泛。为了保证胶囊在胶囊充填机中顺利充填,在制备过程中通常要加入改善其流动性的助流剂。比如,对于一些质轻、堆密度低的粉末药物,通常可以加入1%~2%的PVP乙醇溶液制粒,改善其流动性。目前,国内外药物制剂领域中,采用PVP作助流剂制备胶囊剂的有环扁桃酯胶囊、丙吡胺胶囊、乙基罂粟碱长效胶囊等。
(7)眼药助剂 PVP具有亲水性,还有一定的润滑作用,其溶液有一定的黏性,但黏度又相对于其他增稠剂低,因此常用于眼药制剂中,可以适当增加眼药水剂的黏度,延长药物在眼内的停留时间,同时还可以减轻药物对眼的刺激性。
在隐形眼镜中,PVP可作为接触眼镜的成分,增加其亲水性;此外,当前市场上销售的隐形眼镜消毒剂、润滑剂、清洗剂中一般也都含有PVP,用以减轻对隐形眼镜的磨损。PVP也可以用作水液性人工泪液眼药水的主要成分,举例如下:
(8)崩解剂 交联聚乙烯吡咯烷酮(PVPP)由乙烯吡咯烷酮单体在特定条件下交联聚合而成,是一种性质优良的高分子精细化工产品,也是近年兴起的一种新型药用辅料。
PVPP在医药工业中被称为片剂的三大“超级崩解剂”之一。可用作丸剂、颗粒剂、硬胶囊剂的崩解剂。片剂的崩解大多是由膨胀作用、毛细管作用及片剂中空隙引起的。PVPP具有高毛细管活性和优异的水化能力。加入PVPP片剂能够迅速地将水吸收到药片中,使内部溶胀压力超过药片的强度而迅速崩解。PVPP之间有着折叠分子链,当水或者水溶液渗入时迫使其伸长并分离。因此,PVPP是一种性质优良的高效崩解剂。
一般情况下,PVPP在用作崩解剂时的添加量为1%~5%(质量分数)。并且为了控制片剂及其组成颗粒具有良好的崩解速率,可以在压片前的任何阶段加入PVPP。PVPP作为崩解剂的优点见表2-25。
表2-25 PVPP作为崩解剂的优点

(9)缓控释剂 以PVP作为致孔剂与不溶性聚合物一起可制成骨架型缓释片,调节PVP的用量,并采用合适的制备工艺可以得到最优化药物溶出模式。目前已用PVP作为致孔剂制成了茶碱、吲哚美辛、硫酸锌、硝酸甘油、布洛芬等缓释片。
例如,硝酸甘油缓释片的配方如下:
其制备方法为:将PVP溶解于硝酸甘油乙醇溶液中,加入微粉硅胶混匀,加入硬脂酸和十六醇,水浴加热到60℃,使溶解;将微晶纤维素、乳糖、滑石粉的均匀混合物加入上述熔融物中,搅拌1h;将上述黏稠混合物平摊于医用白色瓷方盘中,室温放置30min,待干燥成团时,用16目筛制粒;于30℃下干燥,整粒,然后加入硬脂酸镁,压片。
在透皮吸收膜剂的制备中,由聚合物形成的微孔性或无孔性控释膜对药物有一定的渗透性。常用的聚合物包括羟乙基纤维素、羟丙基纤维素、PVP和聚乙烯醇等。控制聚合物种类、聚合度、比例和黏度就可以控制药物释放量。例如,以聚乙烯醇、PVP和甘油形成的膜作为氯曲来通马来酸盐的透皮吸收的聚合物基质的研究表明,增大PVP的浓度或增塑剂的量可增加药物的透皮吸收量。
2.5.2 在消毒产品中的应用
PVP在消毒产品中的应用是其应用最成功的一个例子。I2作为杀菌消毒活性成分在水中的溶解度很小,I2的水溶液达不到杀菌消毒的效果。PVP具有优异的络合小分子的能力,生成的络合物具有一定的物理、化学稳定性,在一定条件下,这种络合物与原化合物(或元素)之间存在着一定的化学平衡关系。聚维酮碘(英文简写PVP-I)是碘和聚乙烯吡咯烷酮的络合物,为黄棕色或者红棕色无定形固体粉末,在水或乙醇中能够完全溶解,其水溶液即聚维酮碘溶液,杀菌效力和杀菌谱与碘相当,对细菌、病毒、真菌、霉菌以及芽孢都有较强的杀灭作用,而且杀菌快速、稳定、持久、可靠,克服了碘溶解度低、不稳定、易产生过敏反应、对皮肤和黏膜刺激性强等缺点。自20世纪50年代PVP-I问世至今,它已经成为当今世界首选的含碘杀菌消毒剂,广泛应用于外科手术、预防术后感染,以及烫伤、刀伤、溃疡、口腔炎、阴道炎等疾病的治疗,并且进一步在食品工业、餐饮业、畜牧业、水产养殖业以及日用化学品中得到推广应用,目前已经基本取代了碘酒等杀菌消毒剂。
2.5.2.1 聚维酮碘的合成
目前国内外制取PVP-I的方法主要有四种:溶剂法、固体研磨法、固相络合法和微波加热络合法。前两者是传统主流的制备方法,第三者是当前的主流方法,最后者是近几年才兴起的一种方法。
(1)溶剂法 溶剂法是使PVP与碘在有机溶剂中,于一定温度下反应,然后除去溶剂得到固体PVP-I。该方法主要为德国BASF公司、美国ISP公司(已被Ashland收购)及国内少数企业所采用。溶剂法的关键是溶剂选择,所选用的溶剂必须满足两个条件:①PVP在其中有较好的溶解性;②碘在其中有一定的溶解度。通常可供使用的溶剂为乙醇、氯仿等,以氯仿为例,其制备过程如下:取PVP K30粉末10g,溶于50~60mL氯仿中,加热至50~60℃;另取研磨粉碎的药用级精碘,溶解于约30mL氯仿中,搅拌、加热到60℃左右,直至碘全部溶解。将溶解后的碘溶液缓慢加入到PVP溶液中,保持温度55℃左右,搅拌反应2h,蒸去溶剂,60℃下减压干燥3~4h,粉碎处理后,过筛,即得红棕色固体PVP-I。
(2)固体研磨法 固体研磨法是将PVP(一般为PVP K30)与碘混合,加入特定的助剂,进行研磨制备。具体实施过程:称取100g PVP K30、25g医用级精碘以及5g NaCl,置于球磨机中,开动球磨机研磨4h,即得红棕色固体粉末PVP-I。
(3)固相络合法 固相络合法是将PVP K30与碘加入特定的具有加热供能的保温反应釜,加热到一定的反应温度下,搅拌混合,从而得到成品。这种方法是当前生产聚维酮碘的主流方法。具体制备过程:称取100g PVP K30、18.75g医用级精碘加入三口玻璃反应釜中,保持密闭状态,逐渐升温至70~95℃,控制搅拌转速为200~300r/min,保温反应15~25h,即得红棕色固体粉末PVP-I。
(4)微波络合法 微波络合法是将PVP K30与碘加入特定的微波容器中进行微波加热。利用碘蒸气与PVP K30进行络合,从而得到成品。具体的实施过程:称取100g PVP K30、经过研磨粉碎的20g碘放入玻璃反应釜中,密封后避光搅拌混合均匀;然后转移到微波辅助萃取仪中,控制微波的功率为500W,辐射反应90min,即得红棕色PVP-I粉末。
这四种制备工艺各有优缺点,其对比结果见表2-26。
表2-26 不同制备工艺的对比

2.5.2.2 聚维酮碘的结构和性质
采用红外光谱、紫外光谱及质谱分析可以确认在PVP-I中,碘主要以HI3的形式与PVP结合,其反应机理[23]和反应过程如下:
(2-11)
(2-12)
(2-13)
(2-14)
从上述反应可以推测,PVP和H2O的存在促进反应不断向正反应进行,直至全部的元素碘转化为HI3,与PVP结合为PVP-I。
比较PVP和PVP-I的红外光谱,PVP-I的羰基吸收峰N—CO发生了一定的红移,这可能是由于羰基与HI3中的H+形成氢键后,削弱了羰基双键所致,这种现象符合络合物的特征。由于PVP-I中PVP对碘的分子比大约为20,所以这种红移不是很显著。
由质谱图可推测的碎裂反应也证实在将残余I2反复萃取掉后的PVP-I中存在着与PVP相结合的HI3。
H.U.Schenck等人《Structure of Polyvinylpyrrolidone-Iodine》(1979)一书中,对于上述推理提供了佐证,其推测的聚维酮碘络合物分子结构为[20]:
此结构式表示,在PVP-I中,只有一小部分聚合物单元是与碘结合的。在商品PVP-I中,这个比例大约是18∶2,即吡咯烷酮环∶I2∶HI=20∶1∶1,在20个吡咯烷酮环中,有两个环通过各自羰基氧原子与一分子HI3结合,而其余的18个环是自由的,正是这18个自由的聚合单元,赋予了PVP-I的化学稳定性及良好的水溶性。
PVP-I大大改变了碘的物理性质和化学稳定性。在PVP-I中自由碘(游离碘)含量极小,极大部分碘以络合态存在,从而使碘的稳定性大大提高,毒性大大降低。表2-27概括了碘的饱和水溶液、碘酊、Lugol's碘液及PVP-I的性质。
表2-27 各种碘制剂的比较

注:1.有效碘为用硫代硫酸钠可滴定的碘;自由碘为从碘的溶液制剂中可用乙烷萃取出的量;总碘即为有效碘和碘化物之和。
2. PVP的急性毒性:大白鼠,静脉给药LD50>15g/kg;小白鼠,口服给药LD50>10g/kg。
①在敞口容器中,于室温下存放20h后有效碘的损失。
②在密封棕色容器中,于42℃下存放32d有效碘的损失。
③大白鼠,用2.5%溶液口服给药。
④用淀粉试纸置于敞口容器中。
⑤Lugol's碘液含碘1g,KI 2g。
PVP-I的稳定性,即有效碘储存过程中损失,除了与环境因素及配方密切相关外,还与PVP的分子量有关。不同聚合度的PVP-I稳定性不同的原因在于PVP链的端基为—OH或—CHO,两端可与碘反应。但是PVP-I的水溶液与碘的水溶液、酒精溶液相比,则稳定性大大提高,特别是固体PVP-I可以在室温下保存三年而有效碘损失小于0.5%。
2.5.2.3 聚维酮碘的作用原理
在水溶液状态下,由于PVP对细胞膜的亲和作用,能将碘直接引到细菌的细胞表面,这对提高碘的抗菌活性有意义,碘的进攻靶是细菌细胞膜和细胞质膜,在几秒钟内就立即杀死细菌。因为当巯基化合物,肽类、蛋白质、酶、脂质和核酸等微生物生存所必需的分子与PVP-I接触后,立即被碘氧化或碘化,使之丧失活性,造成各种细菌、病菌、真菌、滴虫不能生存、繁殖而死亡,达到较长时间的杀菌作用且不形成抗菌药性。
PVP-I水溶液用于杀菌的最大优点是形成的活性络合物不易挥发。另一方面,PVP与活性组分之间的结合是通过类似于氢键的比较弱的作用,当与皮肤或黏膜接触时,PVP-I就缓慢地释放出这些有效成分而起到杀菌消毒的作用。在PVP-I水溶液中,主要发挥作用的是游离的活性成分,这些活性成分主要包括I-、I2、、(
),
、(I2)PVP、(
)PVP、(
)PVP,活性成分的消耗促进PVP-I释放出游离碘,就是这样的一个动态平衡保持了PVP-I长时间而稳定的杀菌效果。
PVP-I的杀菌效果与PVP-I的浓度有关。当PVP-I浓度低时,游离碘的浓度会增加;若PVP-I的浓度进一步降低到小于0.1%,则游离碘的浓度又会减少。PVP-I产品通常配成质量分数5%或者10%的水溶液。0.1%~1%PVP-I溶液能在15s内杀灭实验细菌,而10%PVP-I溶液则要120s。但是对于稀溶液PVP-I溶液含有效碘少,导致杀菌效果减弱丧失,特别是当杀菌过程中遇到高浓度血清蛋白或者其他有机物时会导致有效碘的严重损失。因此,在不同的使用环境或需要杀灭的病菌不同时,要根据实际所需的浓度稀释。
PVP-I对大多数细菌、真菌和病毒都有抑制和杀灭作用,而且对于不同细菌的抑菌浓度和杀菌浓度也不一样。PVP-I对一些常见的细菌抑菌浓度(MIC)、杀菌浓度(MBC)见表2-28。
表2-28 PVP-I的抑菌、杀菌效果

2.5.2.4 聚维酮碘的应用
由于PVP-I具有杀菌广谱、杀菌速度快、无刺激和过敏反应、易溶于水、不黄染、作用持久、无抗药性、储存时间长等优异特点,30余年来被发达国家推荐为首选的医用含碘杀菌剂,不仅能用于皮肤消毒而且广泛用于外科、妇科、口腔科、皮肤科、烧伤科、耳鼻喉科、眼科等消毒及治疗;不仅能外用,而且适合于口腔、胸腔、腹腔、阴道、肛门、创面及内脏的杀菌、消毒;不仅能用于临床,还可用于医疗器械、病房、衣物用具、卫生洁具、餐饮具、食品卫生设备、养殖场、游泳池、天然水源等方面的杀菌消毒或疾病预防。
为预防可能潜伏的月球细菌对人类的威胁,美国太空总署特选PVP-I为阿波罗11、阿波罗12、阿波罗14号飞船返回地球时的杀菌消毒剂,可见欧美医疗界对PVP-I优点的认可。
在国内,PVP-I在1986年临床试验获得成功的基础上,于1988年5月正式应用于临床。浙江医科大学附属第二医院24439例PVP-I术前快速刷手浸泡消毒结果表明,用5%PVP-I快速刷手1min后再以0.5%PVP-I溶液浸泡1min,其灭菌效率为97.2%,且无过敏反应;5%PVP-I溶液用于普外、肿瘤、骨、烧伤、整形、五官、口腔七科的择期手术区皮肤消毒共3003例,切口达到甲级愈合3000例,感染率仅为0.1%,且无过敏病例发生。首都医院用10%PVP-I做锁骨下中心静脉管进皮点消毒,总插管时间778d,最长一例为241d,平均39d,结果无一例感染,解决了完全胃肠外营养支持治疗中由静脉管引起感染的难题。
霉菌性和滴虫性阴道炎各30例,用10%PVP-I涂抹两遍,每日一次,连续3d。分泌物源体转阴率分别为80%和90%。对53名用其他治疗方法无效的顽固性阴道炎患者改用PVP-I栓剂或者棉球,24h后用0.3%PVP-I溶液清洗。大多数患者经过数周治疗后痊愈,总有效率达98.1%。
在治疗二度烧伤时,在清创后外涂10%PVP-I或覆盖PVP-I溶液纱布,每1~2d上药一次,直至创面干燥,5~14d后愈合,22例中无一例感染。
用0.1%PVP-I 1000mL冲洗严重腹腔感染者的腹腔,80例只有一例感染,最大安全用量相当于10%PVP-I 2.5mL/kg体重。
用10%PVP-I做牙根管充填前消毒,58例中总有效率为95.2%。另外,在拔牙等口腔手术前后用0.5%PVP-I溶液漱口,或用10%PVP-I涂擦患处,可减少毒血症等细菌感染。
PVP-I与蔗糖组成的复合剂可治疗各种创伤和溃疡面,其优点是创面干燥快、无脓、无刺激、不疼痛、敷料与创面不粘连,因而换药方便,新组织生长快而不结痂,515例创面无一例需植皮,而常规治疗中154例中有62例需植皮。108例皮肤和黏膜受细菌或霉菌感染病例用PVP-I溶液治疗后,36h治愈率为96.8%。
最近还有报道PVP可在棉纤维上接枝聚合,然后再络合碘,用这种棉纤维纺织成的织物能制作烧伤病人的无菌衣,敷料。
最近研究表明,将聚维酮碘溶液直接涂抹于冠状沟上下1.5~2cm,连续用药7~8d,可以明显提高患者ILET,用于治疗男性早泄。
PVP-I在医疗卫生中部分使用浓度及使用方法见表2-29。
表2-29 PVP-I在医疗卫生中的使用

PVP-I优异的杀菌消毒能力及其生理相容性,显示其对人体无刺激性和过敏反应,使它在食品保鲜、餐饮业消毒等方面也有着广泛的用途,在某些方面更显示出独特的优点,如每周一次用0.1%PVP-I溶液喷洒冰箱,可保证冰箱内长期无异味。PVP-I在食品、餐饮卫生行业中的使用浓度和使用方法见表2-30。
表2-30 PVP-I在食品、餐饮卫生行业中的使用

PVP-I在养殖业中的应用是近年来才开发出来的,目前正在进一步扩大使用范围,随着我国养殖业的进一步发展,作为养殖业杀菌消毒剂的PVP-I具有广阔的前景。PVP-I为广谱消毒剂,对大部分细菌、真菌和病毒等均有不同程度的杀灭作用,用于治疗鱼类、贝类、虾类、蟹类疾病的预防与治疗;在畜禽养殖的消毒和疾病治疗也有明显的效果。PVP-I在养殖业中的使用浓度和方法见表2-31(浓度为1%的聚维酮碘溶液)。
表2-31 PVP-I在养殖业中的应用

注:1亩=666.67m2,下同。
以上只是散见于国内外文献的PVP-I应用的一小部分。从中可以看出PVP-I的发明与广泛应用是继PVP在第二次世界大战中作为血浆增溶剂后其在医学上的最重要贡献之一。
国内浙江省化工研究院与民生药厂、浙江医科大学第二附属医院等完成PVP-I新药研制并于1988年正式投产并收载于1990年中国药典;据不完全统计,国内已经有十多家企业获准生产PVP-I原料药,年产能力超过1000t;已经有近百家企业获准生产PVP-I的各种制剂。目前,国内生产的聚维酮碘还主要是用于出口。
纵观全球,无论发达国家或发展中国家,PVP-I的消费量都在迅速增长。进入21世纪,PVP-I的消费量已经达到6000t以上;即使如印度、埃及、伊朗、土耳其等发展中国家每年的消费量亦有200~500t。由此可见,我国的PVP-I的应用和消费与世界先进国家尚有较大差距。随着经济增长和人民生活水平的提高,随着PVP-I应用范围的扩大以及医疗保健事业的发展,可以预期PVP-I在我国的应用会有更迅速的发展。
2.5.3 在日用化工中的应用
PVP具有优异的表面特性、成膜性以及对皮肤无刺激性、无过敏反应等特点,在日用化工尤其是化妆品、护肤品、护发品及洗涤用品方面有着极广泛的应用前景。
2.5.3.1 PVP在化妆品中的应用
近年来,水溶性高分子的良好特性,使其在化妆品领域获得了广泛的应用,很多的化妆品中都有水溶性高分子化合物的添加。水溶性高分子化合物在化妆品工业中的消耗仅次于在造纸、纺织、食品、黏合剂而居第五位。在20世纪50年代之前,人们主要使用天然高分子、诸如黄蓍胶、阿拉伯胶、明胶、酪朊胶等,由于其来源及其质量不稳定,以及其易受微生物污染的缺点,20世纪60年代开始逐渐为半合成高分子如纤维素衍生物和合成高分子如乙烯基吡咯烷酮聚合物[28,29]所代替。由于化妆品的特殊要求,PVP系类聚合物的高安全性、高稳定性,与其他诸多化合物的相容性,以及其独特而优良的溶解性能使其成为化妆品工业中应用的水溶性合成高分子的主导产品。在PVP的消费结构中,在化妆品工业中的应用占其他消费量35%左右,每年的使用量达到16000t。
PVP在化妆品中有多重功能,主要是对乳液、悬浮液等分散体的稳定(胶体保护作用)及增黏作用,护发定型产品中的成膜作用,凝胶类产品中的凝胶化作用,护肤类产品的润滑、保湿及成膜作用(面膜类),泡沫类产品的稳定泡沫作用,以及在各类化妆品配方中的作为色素稳定剂,除臭、保香剂,温和剂(减少某些组分对皮肤的刺激性作用)等,见表2-32。
表2-32 PVP聚合物在化妆品中的应用

2.5.3.2 PVP在护发产品中的应用
20世纪50年代,PVP就开始用作头发的定型树脂。随着PVP的出现,头发定型市场开始迅速发展起来。PVP及其共聚物大量用于护发用品——香波、发乳、发胶、定型液、发膏、喷发胶。在欧美,PVP在化妆品行业应用中,其在护发用品的使用量占其全部供应量的90%。含有PVP聚合物的发型保持剂能在头发上形成富有弹性和光泽的薄膜,起到定型的作用,不沾灰尘,不易剥落,但极易清洗。但是,由于PVP均聚物吸湿性较强,弹性欠佳,不适宜于潮湿气候,它逐渐被PVP与乙酸乙烯酯(VAc)的共聚物PVP/VA所代替。PVP/VA中,PVP(亲水单体)与VAc(亲油单体)之间的比例可以任意调节,从而可以改变其吸水性,以适应不同的气候和不同的定型效果的需求。VAc的含量越高,其吸水率越低,则适宜于较潮湿的气候条件。同时由于分子链中VAc单元的存在,使PVP/VA形成的薄膜更具有弹性。因此虽然新的定型树脂品种不断在市场上出现,但PVP/VA仍是欧美护发用的主流树脂品种。不同规格PVP/VA,其单体组成、性质及用途见表2-33。
表2-33 PVP/VA共聚物的溶解性及主要用途

由于非离子共聚物的功效有一定的局限,在20世纪80年代,市场上开始推出带有阳离子特性的定型树脂,其中最主要的产品就是NVP与丙烯酸类季铵盐的共聚物。如德国BASF公司的PQ-11和美国ISP公司的GaFquaf755(NVP与甲基丙烯酸二甲氨乙酯共聚物的季铵盐)等,还有如BASF公司生产的NVP与乙烯基咪唑啉的共聚物,后者具有弱阳离子特性。由于这类阳离子型NVP聚合物带有正电荷,因此它的薄膜与头发有更持久的结合,使产品有良好的干、湿梳理性,特有的泡沫强度,兼具定型和调理功能。NVP阳离子共聚物的出现是20世纪80年代“摩丝”成功销售的关键因素。同时,由于这一类阳离子聚合物可与阴离子表面活性剂配伍,所以它可在香波香皂中应用,使香波香皂除了净洗功能之外,还兼具调理、定型和柔发的功能。又由于其在碱性条件下,仍能保持对头发的亲和性,使其还适合于在高pH值的冷烫精中应用。NVP的阳离子共聚物几乎全部用于定型产品。PVP共聚物在化妆品中的应用见表2-34。
表2-34 PVP共聚物在化妆品中的应用[30]

PVP及其共聚物在护发产品中的使用更是拥有其独特的优点,头发的主要成分为蛋白质,而PVP的分子结构也类似于蛋白质,所以可以作为头发的营养成分的补充,长期使用含有PVP及其共聚物的洗发护发用品,可以使头发乌黑亮泽,减少发梢分叉现象。
2.5.3.3 NVP聚合物在护肤产品中的应用
NVP的聚合物在化妆品行业的第二位应用是在护肤产品中,这是由于PVP具有形成不闭塞性膜和润湿的作用,结构又和蛋白质结构相似,因此它与皮肤、发须有很好的亲和性,使其在护肤用化妆品中得到广泛的应用,大大改善了护肤用化妆品的感受和功效。例如,PVP的成膜作用在使其在防垢膏(barrier cream)无水净洗剂和防晒膏(anti-flash cream)中得到应用。又如PVP的络合作用使其在护肤类化妆品中作为温和剂,以减轻或消除产品中活性物质对皮肤、眼睛的化学刺激作用,广泛用于唇膏、护肤乳、香波、剃须液、去臭剂等制剂中。其中,已经作为治疗消化道疾患的极细粒度PVPP,当用于护肤制品时,它的作用大大优于以往所用的任何药物,它对皮肤发炎、红斑和痤疮有明显作用,尤其是镇痛和减少刺激。下面是一种晚霜配方:
用此配方制作的晚霜对5名痤疮患者中的4名进行有规律的使用,一个月后,使用者部分痤疮消失。PVP的成膜作用和胶体保护作用,使其用于面膜和其他许多需要稳定的乳液、分散液、悬浮液中,防止分散体系凝聚和分层。
2.5.3.4 PVP在其他日用化学品中的应用
PVP优良的表面活性使其作为一些洗涤用品的成分也具有很好的效果。PVP的去污效果实验见表2-35。PVP的络合能力及分散能力,在添加至牙膏中时,不仅可以增加牙膏的去污能力,还有一定的消炎、镇痛功效。
表2-35 PVP的去污效果实验

PVPP的消炎、镇痛作用,可以应用到牙膏配方中,举例:
每天两次用此牙膏刷牙,不仅能清洁口腔,而且6例牙龈炎患者有4例得到好转。
PVP的亲染料性及对头发的亲和力的结合,可使染发剂得到均匀的颜色。调节PVP与染料的比例,可以制备有不同染色牢度染发剂,使后者成为永久性的染发剂或暂时性的染发剂。PVP含量越高,染发效果就越暂时。其他染色化妆品如指甲油、唇膏等,PVP也可起到上述作用。
PVP的丙烯酸共聚物用于浴液不仅具有分散稳定剂、去污剂的作用,还有杀菌消毒的功能,尤其是作为药皂、香皂成分在夏天使用具有良好的效果。PVP既亲油又亲水的性质使它在清洗衣物特别是在清洗宾馆、饭店桌布用的清洗剂中具有特殊的功效。
PVP可以稳定过氧化物漂白香波,据相关研究报道,PVP可以有效提升过氧化氢水溶液的稳定性。为此,BASF公司和ISP公司都开发并生产出PVP-H2O2络合物,以提高过氧化氢在日化用化妆品和药品中应用时的稳定性,并减轻其对皮肤的刺激性。
表2-36列出了由BASF公司和ISP公司生产和销售的与化妆品有关的NVP聚合物,并对其性质和用途进行了介绍。
表2-36 不同NVP聚合物性质和用途

综上所述,PVP在日用化工产品中的功能主要表现在以下几个方面:①分散稳定性功能,常见的护肤品、膏霜及其他一些化妆品大多是乳液和悬浮液,要使其能长期放置而不产生沉淀变质,使其分散为均一的体系并具有一定的稳定时间十分重要,PVP在化妆品中的重要功能便是分散稳定功能;②去污洗涤功能,PVP及其共聚物由于其特定的分子结构,一方面具有亲油性,可以脱掉衣服、头发及皮肤的油污、汗渍等污染物,另一方面又具有良好的亲水性,这样容易洗去衣物及皮肤的污染污渍;③成膜保湿特性,这是PVP在化妆品中最普遍的功能,广泛用于头发护理品、护肤品等;④杀菌、灭菌功效,主要用于洗涤产品中。
2.5.4 在食品饮料中的应用
2.5.4.1 在酿酒方面的应用
PVP及不溶性的PVPP在酿酒、饮料工业中可作为啤酒、果酒、果汁的澄清剂和稳定剂,在世界上已有近40个国家获得法律许可在生产中应用。以大麦、玉米、酒花、葡萄等植物性原料酿造的低度酒,富含多种蛋白质及多酚类物质。这些蛋白质及多酚类物质以胶体微粒存在于酒中,当长期放置或温度低于0℃、高于20℃就可能产生絮凝沉淀,致使酒液变浑浊,影响其风味,某些多酚类物质是致癌物,在酒液中也对人体有害。除上述的胶体微粒絮凝而引起的浑浊外,还有由于某些生物性杂质引起的酸败而产生的浑浊现象。而啤酒在冷藏时还会产生冷浑浊,当温度升高到20℃以上时浑浊又会消失,如果20℃仍不消失则称为永久浑浊。不论何种浑浊的产生都将影响酒的稳定性,使质量变差。这些都是酒类生产过程中必须解决的技术问题,否则酒难以保证质量。
容易使啤酒等酒类产生非生物浑浊并影响其质量的多酚类[31]主要是花色苷、儿茶酸、黄酮类多羟基衍生物和酚酸类衍生物等。在空气中这些物质或氧化为醌类,或聚合成更易沉降的聚合体,再通过分子中的酚羟基与蛋白质分子的酰胺键以氢键络合沉淀,这些沉淀就是影响啤酒稳定性、色泽、风味的原因所在,要解决这一问题,就要去除产生絮凝沉淀现象的前驱体——多酚类、高分子蛋白质,使其与啤酒分离。
在生产中,解决此类絮凝沉淀的方法有吸附过滤法、沉淀分离法、蛋白酶分解法等。交联聚乙烯聚吡咯烷酮(PVPP)用于啤酒中正是利用它与蛋白质结构相似,可以与多酚类络合而沉淀或吸附分离出来,从而达到澄清、稳定的作用。交联PVP(PVPP)是N-乙烯基吡咯烷酮(NVP)在特定条件下聚合而成的不溶于水、强酸、强碱以及一般有机溶剂的聚合物,所以能够很容易地通过过滤除去而不残留在啤酒中。PVPP与花色苷的吸附是一种氢键络合,其原理见图2-24。

图2-24 PVPP与花色苷的络合
不同量的PVPP处理啤酒后的花色苷含量和啤酒特性变化见表2-37。
表2-37 PVPP不同添加量的吸附效果

①1b=0.453592kg,下同。
从上面的结果可以看出,PVPP可以有效除去花色苷提高啤酒稳定性而又保持了啤酒应有的特点和风味,诸如酒质、风味、泡沫稳定性等基本品质。
PVPP用以处理啤酒等酒类的另一个优点是可经过再生后重复使用,重复使用5次以上的PVPP对总多酚和花色苷的吸附率降低不到5%,每次再生的损失率根据处理工艺及过滤设备的不同而不同,一般在6%左右。而PVPP对总多酚和花色苷的吸附率与初始含量高低有关,一般来说,初始的总多酚和花色苷含量越高,PVPP对其吸附率越高,反之亦然。除此之外,吸附率的高低与PVPP的加入量也有关,从表2-37也可明显看出。再生PVPP对多酚及花色苷的吸附率见表2-38。
表2-38 再生PVPP的吸附效果

PVPP处理对啤酒理化指标的影响,具体指标见表2-39。
表2-39 PVPP处理后的啤酒的理化指标

上面的实验结果证明,PVPP对啤酒中多酚和花色苷的吸附率比较强,再生后的PVPP仍然具有较好的吸附能力,对多酚的吸附率在25%~30%,对花色苷的吸附率在50%~60%。处理后啤酒的浓度、酒精度、总酸、双乙酸、浊度、泡沫等理化指标基本上没有变化。值得注意的是,啤酒的色度和苦味质略有下降,这对淡色啤酒有利,经品尝,由PVPP处理过的啤酒比对照品口感稍好,爽口。啤酒经PVPP处理后,保质期明显延长。
由于PVPP的优异特性,全世界各国相继采用PVPP吸附过滤法作为啤酒稳定化处理、延长其保质期的主要方法。20世纪80年代以来,国内先后有广东、浙江、北京、上海、山东、湖北等地采用进口PVPP和进口PVPP过滤机,取得良好的经济效果。但是进口设备和助剂价格昂贵,大部分啤酒厂难以承受。浙江省化工研究院自1986开始,先后完成PVPP的合成小试和中试研究,并先后与上海华光啤酒厂、杭州啤酒厂等厂家合作,采用国产PVPP完成了工业化应用试验。
2.5.4.2 PVP在非酒类饮料中的应用
PVP不仅在啤酒等酿酒工业中作为稳定剂的应用得到肯定,而且在茶饮料中应用在国外及国内也早已经有很多报道。
过去,茶叶只是作为一种家庭生活用品,经开水浸泡后饮用;现在,人们逐渐认识到可用一些生物、化学技术人为地改变茶叶浸出液的口感和味道,制成各种口味的茶叶饮料。茶叶中影响茶叶浸出液味道的主要成分有三种物质:氨基酸赋予茶饮料香味,糖类赋予甜味,单宁赋予其苦或涩味,调节三种成分的配比即可得到不同口感的饮料。这三种物质的溶出度不同,氨基酸与糖类溶出的温度较低,为40~60℃,而单宁需要80℃以上的温度才溶出。多数情况下需要尽量多的抽出茶叶中的氨基酸等成分而要控制茶饮料中单宁的浓度。
日本专利特开昭 62-61569[32]公开了由颜色较深的红茶制出无色或者浅色的茶饮料的方法。具体方法是通过加入聚乙烯、聚胺类、聚乙烯吡咯烷酮等高分子树脂,从红茶浸出液中吸附掉多酚类物质从而达到脱色的目的。这种方法对于多酚含量太高、颜色太深的饮料能够达到脱色的目的,但不能改善茶饮料的口味。
日本专利特开平 9-220055[33]公开了用PVPP处理茶叶浸出液,任意调节茶饮料中单宁的浓度,从而任意调节茶饮料口味的方法。该方法适用于绿茶、红茶、乌龙茶等。用70℃以上的水浸泡茶叶,充分浸取出其中的氨基酸、单宁类物质,使之与PVPP接触,搅拌使吸附其中的单宁类,吸附结果如表2-40所示。
表2-40 PVPP对茶饮料中成分的吸附情况

注:处理温度为30~40℃;PVPP浓度为质量分数。
从表中数据可以看出,PVPP不吸附氨基酸,而当PVPP浓度达到4000×10-6(0.4%)时,对单宁的吸附率就达到87.5%。要达到充分吸附的要求,一是通过增加PVPP的用量,二是可以对茶叶浸出原液进行多次吸附。吸附时间通常30min就够了,吸附完全后经过滤即可得到清液,专利介绍了配制不同氨基酸、单宁比例(0.3~2)茶饮料的途径有两条:一是通过控制加入PVPP的量直接得到不同单宁浓度的茶饮料;二是得到单宁浓度很低的清液,然后根据需要与浸出原液按比例调配得到。用PVPP处理过的茶饮料可使其长期保持澄清透明,改善茶饮料口味而本身不会残留于茶饮中。PVPP已从各方面被证实对人体无害。另外,PVPP经回收再生后可重复利用,这使得它虽然价格昂贵但使用成本并不高,主要是因为PVPP不溶于水,经再生后损失很少。
采用NVP与N,N-亚甲基双丙烯酰胺聚合的交联PVP对福建铁观音(二级)浸取液进行了吸附研究[3],重点对处理温度和再生后PVPP的吸附性能进行了比较,吸附温度对吸附效果的影响见表2-41。
表2-41 PVPP吸附效果与吸附温度的关系

注:单宁起始浓度为211.3mg/110g;PVPP浓度为质量分数。
从上表可以看出,在20~30℃,PVPP对单宁的吸附率无明显变化,继续升高温度,PVPP对单宁的吸附率随之下降,温度升高到60℃时,吸附率下降为30%左右,PVPP对茶饮料中单宁类吸附处理的温度控制在20~30℃比较适宜。
再生PVPP(再生方法与处理啤酒后的PVPP相同)对茶饮料的处理效果见表2-42。
表2-42 再生PVPP对茶饮料中单宁的吸附效果

注:1.单宁初始浓度为272.8mg/100g。
2.每次茶饮料处理量均为100g。
3.处理温度为30℃,处理时间为30min。
4. PVPP浓度为质量分数。
可以看出,即使经过5次再生使用的PVPP仍有明显的吸附茶饮料中单宁的能力。除茶饮料外,PVPP对其他饮料,如橙汁、果汁等饮料也有澄清、稳定、延长保质期的作用。
PVP对过氧化物有着一定的稳定作用。H2O2作为一种杀菌消毒剂,兼具漂白剂、活性氧释放剂的作用。它可用于饮用水的杀菌消毒,用于化妆品可以使皮肤增白,用于洗涤剂中具有漂白、灭菌的作用,还可作为酒类、饮料的消毒剂。近年来,它还被配制成活性氧的释放液,以代替氧气,具有长效、方便的特点。另一方面,H2O2的不稳定性和易分解性给它的使用带来诸多难题。H2O2对pH、温度、溶液杂质都很敏感,pH较高、温度稍高或者含有微量金属离子及其他杂质时,H2O2都很容易分解,即使在较理想的条件下,放置时间稍长也会有H2O2从溶液中溢出或分解。市售的过氧化氢一般为30%或35%的H2O2水溶液,只有极少量适用于特殊用途的高浓度H2O2溶液。
美国专利5587191[34]报道了用PVP作为稳定剂配制稳定性活性氧释放液,加入的PVP包括PVP K15、K30、K90,根据它们与H2O2形成络合物的稳定性不同,可保证它们在使用过程中缓慢地释放出活性氧,以满足人们的需要。配制PVP-H2O2溶液的方法如下:用蒸馏水按1∶1稀释35%的H2O2原液,得到17.5%的H2O2溶液,把该溶液冷却至5~8℃并保持该温度,边搅拌边依次加入PVP K15、K30、K90,使完全溶解。加入三种分子量PVP的比例为10∶25∶5。溶解后的溶液中H2O2含量为12.5%,PVP K15含量为7.1%,PVP K30含量为17.9%,PVP K90含量为3.6%,与H2O2络合物的稳定性顺序为PVP K15< PVP K30 <PVP K90。使用时用配制成的PVP-H2O2稳定溶液稀释即得到氧气的代替品——活性氧释放液。在溶液的配制过程中所使用的仪器要用玻璃仪器或搪瓷制品,而且要经过杀菌消毒处理。
对含有PVP和不含PVP的经过稀释的H2O2溶液的稳定性时间对照考察结果见表2-43。
表2-43 PVP对H2O2的稳定性效果考察

通过上表可以看出,2d放置后,不含PVP的H2O2溶液的分解率达到了接近90%,而加入PVP的H2O2溶液的分解率在50%左右,PVP对H2O2有着良好的稳定作用。
另外,利用PVP对H2O2的稳定作用,也可以制成固体的PVP-H2O2络合物,分散于食品中,缓慢释放活性氧,使细菌不能生存,进而延长食品的保质期,对于需要长期放置的熟食其意义更为重大。
PVP也是各种果汁、醋、酱油和其他液体食品、保健品良好的澄清剂和稳定剂。在很多情况下,由于一些液体食品中会含有少量的酚类和多元酸,放置时间过长会析出,进而出现浑浊现象。在生产和加工过程中只要加入微量的PVP,就可以改进它们的澄清度,防止发生浑浊现象,并可以稳定光泽、改善口味、延长储存时间。PVP与一定比例的糖类配合是优良的糖果食品包衣材料,使其容易成型成膜,且长期放置也不易破裂。
2.5.5 在涂料、颜料以及油墨中的应用
聚乙烯吡咯烷酮由于其分子结构具有亲水基团与亲油基团,以及对固体粒子表面的良好吸附能力,因而可以改变界面或溶液状态,是一种高分子表面活性剂。在不同的分散体系中,不同分子量的PVP可作为分散剂、稳定剂、乳化剂、增稠剂、流平剂、粒度调节剂、抗再沉淀剂、凝聚剂、助溶剂及洗涤助剂。在涂料、颜料、油墨、高分子合成及加工、洗涤剂、黏结剂、感光材料、药物、化妆品、食品等工业过程或工业产品中,PVP以其优良的溶解性、成膜性、生理惰性、络合能力等综合特点的发挥,而得到广泛的应用。
2.5.5.1 PVP在有机颜料中的应用
化学合成方法得到的有机颜料粒子具有较大的比表面积,比表面积达到8~100m2/g,通常的机械处理方法只能使颜料粒径达到70~100μm,还不能直接使用。于是人们通过表面处理技术来改变某些使用性能,如分散性、热稳定性、抗溶解性、化学惰性和光固性能等。实际上,对颜料进行表面处理就是在颜料聚集成大颗粒之前,用某种方法阻止其粒子的长大,最好的方法就是将颜料粒子保护起来,同时赋予其所需的使用性能。
PVP具有良好的成膜性,溶于水而不溶于某些有机溶剂。用于颜料溶剂的物质大多数都是有机溶剂,而PVP随着分子量的增大,成膜性更优异。在有机溶剂中的溶解性较差,利用PVP(Mw大于30000)处理颜料微粒,由于PVP与颜料分子的亲和性而在颜料微粒表面形成一层透明的薄膜,形成的膜不易溶于有机溶剂,所以不易被破坏,使用时不会产生色料的扩散现象,不会影响本色,并能提高颜料的光泽和分散性,隔断了有机颜料与外部环境的接触,进而间接地赋予了有机颜料化学稳定性与热稳定性,避免了与外部环境中某些物质或光热造成的化学反应,提高了颜料的光固性能。用于有机颜料表面处理的PVP一般为PVP K90,或者NVP与乙酸乙烯酯等乙烯类单体的共聚物,PVP的用量一般为有机颜料质量的5%~50%。可用PVP表面处理的颜料主要有:防护性和装饰性涂料,如清漆、油漆等;水溶液分散体系;印刷、墨水、织物着色和塑料上色;乳胶体等。我们以耐晒黄-10G为例,研究了PVP K90对其表面处理效果,结果见表2-44。
表2-44 PVP K90对耐晒黄-10G的表面处理效果

从上述实验结果可以看出,颜料的综合性能,并非PVP用量越多越好。事实上,对不同颜料处理所需PVP的最佳用量不一致,对于耐晒黄-10G而言,PVP K90用量与耐晒黄质量比在1∶10时,表面处理的颜料具有优良的着色力和光泽。
PVP优异的分散性能还可用于炭黑、酞菁颜料、钛白粉等多种颜料的分散。例如,用炭黑与适量的PVP制得的分散体在球磨时不易发生凝胶化现象,易于过滤,粒子细而均匀,黏度低,稳定储存期长,解决了炭黑包浆易絮凝、沉淀、结块等问题。由酞菁蓝或钛白粉与乙酰丁酸纤维素、PVP捏合、粉碎制成的颜料分散体稳定性好,用于聚氨酯溶液的着色时,不絮凝、不乏色,适用于织物处理。某些发光颜料,如与鸟嘌呤、柏林蓝等在溶剂中用PVP进行表面处理,经喷雾干燥后得到的粉状颜料,光泽及分散性能都很好,而且使用方便。
2.5.5.2 PVP在涂料中的应用
在乳液涂料和水溶性树脂涂料中,由于颜料的分散性不好和储存时的凝聚沉淀而使得着色效果降低,出现浮色、光泽差等不良现象。为此,需要合适的分散剂,一般的低分子量表面活性剂成膜性差,流变性能不稳定,而且对所采用的黏结料限制很大。高分子分散剂具有稳定性高、流变性能好、在颜料表面吸附性能好、提高着色力及改进光泽等优点,是颜料分散剂发展的方向。而中高等分子量PVP的添加可以显著解决上述问题,提高着色力,消除浮色现象,分散和稳定颜料成分,改进光泽,避免颜料的絮凝沉淀。
在苯乙烯、甲基丙烯酸酯为主体的乳液涂料中,由于乳液黏度很低,以往采用水溶性高分子添加法、溶剂添加法、碱性增稠法、蒸发浓缩等方法增稠。其最大缺点是,乳胶黏度难以控制,随时间而变化,且涂料层抗水性降低。而在这类乳液中加入适量的PVP,经蒸发浓缩可使其黏度提高10倍以上,得到高黏度的稳定性的合成树脂溶液。用PVP增黏的涂料乳液配成的涂料具有不流挂、涂层耐水好、皮膜硬、不脱落、耐污等优点。近年来有研究表明,在颜料与水组成的悬浮体系中进行NVP的聚合,在NVP聚合的同时使颜料粒子分散,再引入乙酸乙烯酯单体与丙烯酸丁酯继续在颜料粒子表面聚合成膜,最终得到稳定的涂料分散体,用该涂料获得的涂层可防止食物被污染。
2.5.5.3 PVP在特种涂层中的应用
在喷印用纸张表面,一般涂有一覆盖层。含有PVP的透明涂层使喷印墨水在其上快速干燥。该透明层具有良好的吸墨水性,不溶于水,有较好的凝固性、扩散性,并且因透明而高速成像,尤其适用于多色彩的墨水喷印。
除此之外,PVP在其他涂层,如导电性涂膜、电极涂料、防漏电涂层中都有重要的用途。如在导电性材料外的绝缘层,经过反复的骤热、骤冷、日晒雨淋,会老化或破裂,或者因为渗水而漏电。在绝缘层的外部形成一层PVP薄膜(PVP K90或某些高分子量共聚物),一方面PVP薄膜是透明的,不影响绝缘层的本色;另一方面,PVP薄膜与绝缘层黏结在一起,把绝缘层与外界光、热、雨等隔离开来,避免了渗水破裂而引起的漏电现象,降低了因光、热而引起的老化速度,延长了电线的使用寿命,同时也适当增加了电线的硬度。另外,为防止静电危害而制造的导电性塑料薄膜,是在塑料薄膜上薄薄地涂上含有炭黑和黏结剂的导电性、透明涂料,再于其上涂一层透明保护层而制成。PVP在此作为炭黑的黏结剂及分散剂,采用分子量为10000的PVP,得到了导电性、透明性好,能涂布均匀,易干的导电涂层。若需要提高涂料含量,则可通过添加高分子PVP来调节。
2.5.5.4 PVP在油墨、墨水中的应用
书写钢笔用墨水和喷射印制用油墨必须具有良好的稳定性和黏附性,这样才能保证字迹牢固不褪色,墨水不沉淀堵笔,而且打印机在长时间连续运行喷射印刷时,不堵塞喷嘴。此外,也要求在停止喷射或印刷时,没有因残留在喷嘴中的油墨干燥硬化而堵塞喷嘴的现象发生,不妨碍重复喷射,不影响喷射方向,能保持流畅的再喷射状态。为满足这些要求,过去使用乙二醇、二乙二醇、甘油等多元醇作为墨水、油墨的湿润剂成分,在一定程度上能控制停止喷射时喷嘴中的干燥固化。但长时间运行或长时间停止(一周左右),在喷嘴出口处仍有残留物沉积,改变了喷射方向或者使字迹线条粗细不均匀,甚至完全堵塞喷嘴,以致得不到满意的结果。
PVP具有好的黏结性能,可作黏合剂,用于墨水、油墨可使书写和印刷的字迹牢固地附着于纸张上而不易脱落和褪色。再者,PVP对无机颜料、有机颜料分散体有良好的分散稳定效果,用于墨水和油墨可得到均一的分散体系,不易沉淀,不堵塞钢笔和各类喷嘴,得到的字迹深浅均匀一致。而且PVP具有不挥发性,其作用和功能持久,尤其是印刷或打印设备长期停止运行也不会堵塞喷嘴,具有流畅的重复喷射书写性能。用于墨水、油墨的PVP一般为分子量较低的PVP K12到PVP K30产品。
作为印刷品,如邮票、打印机色带等使用的喷印墨水,由于需要长期使用,所以需要耐光性和耐水性优良的颜料作为墨水的着色成分,要求作为颜料微粒子的主要成分能均匀分散,避免分散不好引起的凝集,喷印墨水在分散稳定性和黏度等方面性能如果不好,就会使喷印画像和字迹不满意。另外由于喷印设备长期使用会导致局部升温,还要求墨水具有一定的温度稳定性。
圆珠笔用墨水、油墨中加入PVP K30,起到保护胶体、增稠、增黏的作用,使书写流利,不溢流、不褪色,还可以减少球珠的磨损,延长其使用寿命。
身份证和其他各类证件这类特殊的物体是通过上面的条形码来鉴别的,为了使证件不致出错,以致造成误会或发生严重的错误,条形码的制作必须精良,精确无误,使用时间有时超过几十年。为满足这些要求,证件的制作是通过一种特殊的磁性油墨实现的,这种油墨的主要成分为磁性体粉末、黏合剂及有机溶剂,作为黏合剂成分加入其中的PVP可增加条形码的附着稳定性,而且在作为条形码基材的合成纸、人造胶片上形成均匀的条形码皮膜,使条形码边缘整齐牢固,不易损坏。PVP与聚乙二醇复合使用效果更佳。
PVP在喷印墨水、涂料、照相乳液等行业作为分散稳定剂、流变调节剂等的总用量并不是很大,但是在某些产品中则一直是不可或缺的,历经几十年不变。
2.5.6 在纺织印染及洗涤工业中的应用
2.5.6.1 PVP在纺织印染中的应用
由于PVP分子中存在的内酰胺结构,与羟基、氨基、羧基之间有很强的结合力,而染料中往往就含有这些官能团,所以PVP与一般的有机染料都有很强的亲和力,有时这种亲和力甚至超过染料与纤维的结合力,故而PVP有“液体纤维”之称。利用PVP的这一性质可以增加一些疏水性纤维与染料间的亲和力,进而改善这类纤维的可染性,例如,在合成纤维过程中将适量PVP掺入其中,使合成纤维可以均匀地染色,并提高着色力和提高染色深度,对染色比较困难的聚丙烯纤维,在其中掺入7.5%左右的NVP/苯乙烯共聚物,可使纤维对酸性染料的染色深度增加10倍左右,对分散性染料可增加5倍左右。在掺合PVP的工艺中,使它均匀分布于纤维中,可大大降低染色后织物的色差,提高染料在织物上的附着力。得到色泽均匀、耐光耐热、不易褪色的纺织染色品。
PVP除可改善某些纤维的可染性外,还可改进其吸湿性、防晒性等性能,大大提高合成纤维的质量和档次,例如合成纤维中的聚酰胺纤维、聚酯纤维等以高强度、高细度、耐摩擦性、热可塑性及良好的光泽和鲜明的染色而深受欢迎,但是吸湿性却比天然纤维差,导致其作为衣物使用时常在衣物的表面附着一层来自空气中的水蒸气而影响穿着的舒适感,尤其在夏天高温潮湿的天气,吸湿性差的衣物很容易被体汗或高湿度的空气湿透而紧贴于皮肤上,甚至对皮肤产生刺激性。解决这一问题的方法之一就是在纺丝前熔融聚酰胺中加入4%~8%的PVP,然后在低氧环境中进行熔融纺丝,加入的PVP K值在30~70,其中残留单体含量需要小于0.1%,这样得到的聚酰胺纤维和聚酯纤维等合成纤维具有高吸湿性、耐洗涤性、热可塑性,而且如前所述,PVP的加入也可以改善一些染色性能,控制纺丝速度可以得到不同细度的纤维。值得一提的是,如果加入的PVP K值低于30,由于低分子量的PVP与聚酰胺络合能力较差,在水处理的工序中就会有部分的PVP溶解于水中而得不到高吸湿性的纤维。另一方面,如果所加PVP分子量大于70,炼丝时熔融体系黏度增大,使纺丝时吐丝困难,影响生产效率,而且PVP分子量太大,所得纤维硬度太大,达不到合成纤维柔软舒适的要求。用PVP K60改善的聚酯纤维吸湿率最高可达纤维本身质量的20%。PVP对合成纤维主要性能的影响[35]见表2-45。
表2-45 PVP对合成纤维主要性能的影响

注:1.黄色度指加入 PVP 经纺丝后未经染料的纤维的黄色度,低于 10 为合格。
2.导致生产效率低的因素有两个:一是PVP溶解率增大,二是出丝速度慢。
3.表中溶解率数据为合成纤维在沸腾的水中处理30min时PVP的溶解率。
PVP与不同染料的结合能力是有差异的,利用这一性质,对聚酰胺纤维、聚丙烯纤维进行防染法印花时,可用PVP作局部防染剂,得到图案鲜明、轮廓清晰的印花织物。
增大PVP对金属络合染料的比例(至少1∶2)时,就可制成标记色料——暂印染料。这种染料对羊毛、腈纶、尼龙、涤纶、黏胶纤维染色后,其颜色很容易用水洗掉,仍然留下白色的纤维。
大部分水溶性高分子化合物具有胶体保护作用和增溶作用,但PVP在这方面性能尤为优异,故可作为分散染料高温染色用的结构型匀染剂,以提高分散染料的稳定性和染色速度。这种分散染料是将PVP与染料在溶剂中一起喷雾干燥加工而成的,染料与PVP呈固溶态,粒度<0.1μm。
分散性染料在溶剂染色中因染料不溶于溶剂,通常需用大量的表面活性剂,溶剂回收量大,上染率、色牢度较低。如用PVP(常为其衍生物)作染料加工的分散剂,可得到一种储存稳定的分散染料。这种染料对聚酯纤维进行溶剂染色,可得到耐湿、耐磨、耐热、耐光的均匀染色织物。1%~3%的PVP可以防止还原染料、分散染料储存时的触变和降解作用,数周后仍然保持染料糊剂的流动性。在羟甲基类的防皱防缩整理剂中加入<3%的PVP(以固含量计),就可提高这类助剂的储存稳定性。储存数月后,再制成的水溶液一周后仍不会沉淀。
转移法染整工艺具有速度快、助剂用量少、加工质量好等优点,关键是需要一种对纤维有亲和力、溶剂相溶性好、成膜性好、适宜涂布的糊料;还要求它对染料和整理助剂有分散、稳定的作用和一定的黏结性;配制容易;溶于水,染整后易用水洗去。由于PVP符合上述各种要求,故在转移法染色、漂白、净洗、整理(防皱、防水、抗静电等)中,PVP有较广泛的适应性和良好的效果。
通常在织物整理中,阳离子型的整理助剂与阴离子型的荧光增白剂互不相溶,不能同浴对织物加工。如果在浴中添加0.1%~2%的PVP,则可将柔软剂或抗静电剂、树脂整理剂与荧光增白剂同时在一浴中对织物进行加工整理。处理后织物的白度、荧光度、柔软性、静电带电量、强度等都达到或超过其性能指标。
2.5.6.2 PVP在净洗剂中的应用
在纺织印染工业中,织物经印花后,要经过水洗(或皂洗)退浆,目的是洗去织物上未固着的染料和用毕的浆料及其他印染助剂,以提高色牢度,恢复手感,得到图案鲜艳清晰的印花织物。为此,要在水洗和退浆过程中使用一定的净洗剂。对净洗剂的一般要求是能有效地洗去未固着染料和浆料,又不产生过分的剥色;对织物无损伤;用量少,用水省。但是,在净洗过程中随着未固着的染料从织物上逐渐转移到浴中,形成了具有一定染料浓度、一定温度和一定时间的染色浴条件,使染料在被净洗织物的不同染色部分之间,通过净洗浴而相互转移,特别是从有色部分向无色部分的颜色转移,即所谓白地玷污。
因此,研制并生产能防止白地玷污的印染洗涤剂和家用洗涤剂是解决上述净洗问题的关键。防白地污染剂必须同时具备一定的净洗能力和防染能力。这种净洗能力要与染料的湿牢度相适应;这种防染能力必须足以抑制在这种净洗条件下所具有的污染速度。
由于PVP具有优异的胶体保护性能和染料亲和力,在印染工业中作为净洗剂组成引人注目。它与一定的表面活性剂、漂白剂和其他助洗剂相结合,可以制得适合某种要求的高效净洗剂、防白地玷污剂或匀染剂。研究表明,以PVP和硅酸铝酸钠为主要成分的印染工业用净洗剂具有明显高于不含PVP的净洗剂的净洗能力,而且可以防止净洗过程中颜色的转移或白地沾污。
2.5.7 在化学反应及聚合物制备中的应用
在乳液聚合、悬浮聚合、本体聚合等高分子合成反应中,通常可用PVP作为增稠剂、分散剂、稳定剂或者粒径调节剂。在乳液聚合中,可以用分子量比较大的PVP(K值>60)作为保护剂防止悬浮体沉淀,阻止反应体系中较大粒子的聚集,使体系稳定;而低分子量PVP(K值<30)更适宜于作分散剂,特别是对低密度物质的分散,前提是其分子量及其分布必须与分散体的粒径及其分布相适应。
PVP与NVP共聚物在苯乙烯均聚及共聚,氯乙烯、甲基丙烯酸酯、聚氨酯的悬浮聚合,丙烯酸酯、羧酸乙烯酯的乳液聚合中均能发挥优良的分散稳定和控制粒径、调节黏度、改善树脂性能的作用。
在粒状聚氨酯脲的悬浮聚合中,以往的技术有的采用有机溶剂,有的只能得到水分散体或使其凝固后得到大块状体,给使用、运输等带来不便,增加了加工成本,影响了产品质量。因此迫切要求开发能得到小粒径聚氨酯脲的一步法合成技术。PVP特别适宜于作这种一步法聚合时的悬浮稳定剂。其添加量为水相的2.5%~5.0%,其分子量取K值为60。当反应结束后,蒸出甲苯-水共沸物,冷却、过滤、洗涤、干燥即可得到粉体聚氨酯脲。当PVP K60用量为2.5%时,所得聚合物粒径为800~1000μm。聚合物中异氰酸酯含量小于0.5%,基本上无孔,可用于涂料、黏结剂、絮凝剂、层压复合材料,制成薄膜,厚度为100μm,作为涂料,厚度为10μm。
甲基丙烯酸甲酯、醋酸乙烯、聚乙烯、氯丁二烯等单体聚合时,所得产品往往只有在120~150℃温度下具有高弹性,且含有未反应的引发剂等杂质。但当引入PVP K30或PVP K15作为乳化剂时,所得甲基丙烯酸甲酯聚合物的高弹温度范围为120~280℃;在50℃下进行乳液聚合,可在20~100min内使聚合单体完全转化,所得聚合物流动温度为270~280℃。
氯乙烯的悬浮聚合如采用PVP作为分散稳定剂,所得聚合物热稳定性较好,采用NVP共聚物作稳定剂,可改善PVC的扩散性。而采用由NVP与醋酸乙烯共聚物为组分之一的混合悬浮剂,则所得聚合物的热稳定性、吸油率、粒径、鱼眼、残单都有较大的改善,结果见表2-46。
表2-46 采用不同分散剂时聚合物性能比较

①混合悬浮分散剂,其余组分为乙酰化PVA或者甲基羟丙基纤维素。
②NVP与乙酸乙烯酯比例为3∶7。
③NVP与丙烯酸异辛酯共聚物,NVP/IOA为9∶1。
在丁苯乳液聚合中,采用PVP与表面活性剂配合,能起共稳定作用,最终得到低黏度、高固含量的乳胶,且粒径小、抗水性能好、干燥速度快、不起泡,固含量高达60%~65%。产品可用于涂料、地毯胶等许多使用聚合物乳液的地方,PVP的用量为0.5%~1.0%。分子量以PVP K15为最好,用不同配合的表面活性剂所得乳胶配制成地毯层压涂料进行实验,结果见表2-47。
表2-47 使用表面活性剂的丁苯乳胶的性能比较

北京东方化工厂在醋-丙乳液聚合中,采用PVP K30作为保护胶和增稠剂,产品质量优良稳定。该厂对浙江省化工研究院中试PVP K30产品进行了高固体份醋丙乳液聚合试验,并与进口PVP K30作了相同条件下的对比试验。结果证明,采用国产PVP K30,乳液的性能与采用进口PVP基本一致,而且乳液加工应用证实,涂料的耐水、耐冻融稳定性等方面较进口产品有所提高。
除了在聚合物反应中的应用广泛以外,PVP在分析化学及催化剂中也有一定的作用。PVP 的水溶液在不同量的(NH4)2SO4存在下,能分成液-液或液-固两相。该体系用于某些金属离子具有较好的萃取效果,如含20%PVP的PVP-(NH4)2SO4-H2O体系中,以偶氮胂(Ⅲ)为萃取剂与含Zr(Ⅳ)、La(Ⅲ)离子的溶液反应形成络合物,在一定条件下,Zr(Ⅳ)与偶氮胂的螯合物在PVP相中萃取率很高,而La(Ⅲ)的萃取率很低,进而达到分离Zr(Ⅳ)、La(Ⅲ)的目的[36],另外,PVP与某些金属本身有良好的络合性,如PVP与微量的Cd即可络合生成PVP-Cd,利用此性质可成功地测出微量镉[37]。另据相关研究报道,对于甲醇气相羰基化反应,碳负载胶体金属铑催化剂(PVP-Rh/C)的活性和选择性远远大于单纯的碳负载金属铑催化剂,这是因为铑与PVP形成的胶体金属催化剂颗粒粒径分布窄、分散度高,比表面积增大,在提高催化活性的同时也提高了反应选择性。
2.5.8 在黏合剂中的应用
PVP具有优良的亲水性、分散稳定性、无触变性、增稠性等特点,并且对玻璃、金属和塑料表面具有特别的黏结力,使它广泛用于各种黏合剂配方中。第一种应用是将PVP作为胶黏剂的主要成分,第二种应用是将PVP的黏结性能用于需要黏合剂组分的其他产品中,如涂料、油墨、上光剂、各种片剂、颗粒剂、烧结材料、釉料等。
(1)在胶黏剂中的应用 PVP作为胶黏剂的主要成分,在工业上应用最广泛的有固体胶棒、压敏胶及再湿性胶等。
固体胶棒是新型办公胶水,克服了液体胶水的种种缺点,其使用方便,初黏力强,适用于各种纸张,黏合后平整无皱,因此近20年来成为世界流行的办公用品。作为固体胶棒的黏合剂应具有黏结能力强,特别是初黏力好;涂布性好,涂层薄而均匀;固形性,在涂布时不变形,且能适应各种气候条件;储存期长,无毒。研究证明,在各种水溶性高分子中,PVP是能全部满足上述要求的极少几个品种之一。近年来,市场上也出现了以PVA为主要黏结成分的固体胶水,但它们一般都难以克服PVA的凝胶化倾向,保质期短,最终失去黏结力。表2-48为浙江省化工院的样品与同样采用PVP为原料的德国三家公司产品的黏着强度比较。
表2-48 固体胶水黏着强度比较

注:基材为湖蓝全棉纱绸,40支×40支,测试方法GB/T 532—1989。
应用试验证明,固体胶水适合于各种书写纸、蜡光纸、拷贝纸、胶版纸、凸版印刷纸、皱纹纸,特别是对小件纸品的粘贴可以操作自如,即贴即写;还可以粘贴织物及聚苯乙烯材料如装饰用发泡纸等。因此,已在国内迅速推广,出口前景良好。
以NVP聚合物为主要成分的另一种胶黏剂是压敏胶。在压敏胶配方中加入PVP可提高胶带的初黏力、强度和硬度。丙烯酸酯与NVP的共聚物可以作为精细材料的保护性膜,具有反复黏着与剥离的性能。医用皮肤压敏胶广泛采用包括PVP在内的水溶性高分子作为黏结成分,特别在皮肤给药膜上,这是一种全新可控释放给药方式。药膜本身含有可通过皮肤吸收的药物,NVP聚合物作为一种黏结剂,成为凝胶状的药物基质,促进药物的扩散。治疗心肌梗死的硝酸甘油酯就可以做成这样的药膜。又如NVP与丙烯酸酯的共聚物就可以作为杀菌剂碘的载体,通过其压敏黏结性固定在皮肤上,成为局部防感染的皮肤给药膜。另一类医用压敏胶的作用是将医疗器械的电极固定在皮肤上,它往往是具有压敏黏结性可以反复利用的,而且能吸附电解质溶液的水凝胶,PVP可以增加水凝胶的强度,提高其在电解质中的稳定性。
第三种以NVP聚合物为主要成分的黏结剂是再湿性胶,所谓再湿性胶是指在干燥状态不具有黏结性,而在吸水的状态下可以发挥黏结作用。PVP特别是PVP/VA,由于其可调节的吸湿性,成为这类黏结剂的主要成分。一种热熔涂布、再湿使用的黏结剂就是由PVP/VA、聚乙二醇组成的,其配方见表2-49。
表2-49 再湿性黏结剂配方

(2)在其他产品中作为黏结剂的应用 由于PVP对玻璃有优良的黏结性,所以被用于玻璃纤维的上光剂,使玻纤表面更光滑,减少在拉伸过程中的磨损,增加纤维束的抱合力。酚醛树脂、饱和聚酯树脂纤维素衍生物、乙酸乙烯/甲基丙烯酸甲酯树脂都可与PVP共同组成玻纤上光剂。某些配方已在国内一些大玻纤厂得到应用。
据以相同的原因,PVP还可用于许多无机纤维如碳纤维、Al2O3纤维、钛酸镁纤维的制备和加工,增加纤维与树脂复合时的黏结力。
在用玻璃、陶瓷、石英、石棉、云母等无机材料制备高柔性、特种纸时,PVP往往可以起到分散、黏结的作用,提高纸张的强度。
PVP在精细陶瓷加工、高尺寸精确度烧结陶瓷、可控磁性烧结陶瓷、柔性陶瓷、陶瓷表面涂层、陶瓷玻璃用印刷油墨、瓷器釉料、镀镍钢搪瓷釉药中都可作为浆料、颜料等分散剂、黏结剂而受到广泛的重视和应用。在陶瓷加工中,PVP可在烧结时完全燃烧。因此,对陶瓷本身无任何影响。PVP K90 还可防止陶瓷制品在烧结前的破裂,还可消除陶瓷坯体表面起皮现象。
在釉料和油墨中,PVP对颜料和染料的亲和性可保证釉料和油墨的均匀、稳定和高附着力。
PVP是所有类型工业或民用片剂、颗粒剂的成型黏结剂,例如用于义齿的清洁片和儿童用绘画涂料片。
PVP K30 和PVP K90 是制造石膏绷带的良好黏结剂,将PVP溶于有机溶剂如甲醇中,生成甲醇-PVP溶液。将石膏分散于其中,然后将悬浮液施于绷带上,干燥后即可得到塑性好、均匀一致的石膏绷带,减少碎粉,增加弹性和牢度。
PVP K17可以作为照相纸的黏结剂。
各种需用黏结剂的产品都有其特别的要求和使用条件,只要充分了解PVP的各种性质及其相互关系,就可以在许多新产品的开发中发挥PVP的作用。
2.5.9 在新材料领域中的应用
PVP对感光胶的光敏性能、黏结性能、流平性能的提高起了很大作用。国内外许多大彩管厂均采用PVP-叠氮化合物作为水溶性感光胶的重要组分。由于感光胶显影后对黑白条纹界面不均度要求较严(小于0.01mm),因此对用于感光胶的 PVP K90的质量要求,特别是对分子量、黏度及杂质的要求较一般工业级规格产品为高。为了保证彩管生产质量的稳定,对PVP K90的聚合体系和聚合工艺应作专门的研究和调整。除了水溶性感光胶之外,PVP还用于彩管阴罩涂料,导电涂料及荧光屏用的光敏材料中,在这些彩管材料中。PVP主要作为活性组分的分散剂和黏结剂。
PVP可以用于光电池或太阳能电池中用来稳定光氧化/还原染料,也可以用于铝电解电容器中作固体电解质的黏结剂或平板玻璃、离子电极的黏结剂。PVP 与 Cd2O3在加热和加压条件下混合可作为蓄电池的电极。75%~98% Ni粉、2%~2.5% PVP在1700℃下烧结10min 可以制成自支撑多孔 Ni-Cd 和Ni-Fe 碱性电池的电极。也可用PVP将镁粉固定在不锈钢纤维板上作为电池电极。在这些场合,PVP都作为金属粉末的黏结剂和分散剂。
PVP可用于各种功能膜材料的制造中,以改进膜的选择性。例如,在乙酸纤维素中加入1%~4%的PVP,所制成的血液透析膜只能透过旋复花粉(C6H10O5)(insulin)而不能透过血浆。在羟丙基纤维素中增加PVP的含量,可增加水蒸气的透过率,乙酸邻苯二酸纤维素与PVP制成的膜可以作为过滤有机溶剂的反渗透膜,用PVP也可以改进海水脱盐的反渗透膜,提高其透过率。
PVP可用于重氮和卤化银乳液,蚀刻涂料和印刷板的上胶剂中,形成光固化的水溶性胶体,可增加胶体的覆盖力、密度、反差和速度。在金属感光板中,使用PVP可省去深蚀刻,而在非成像区保证黏度均匀、温度稳定、附着牢固。对于卤化银乳液,PVP胶体显影时的加工助剂,用以除去重铬酸成盐的锈斑。
在减阻涂料、光导纤维、激光视盘等新技术领域,PVP的优异性质也受到重视和研究。NVP与甲基丙烯酸的羟甲(乙)基酯或乙二醇酯的共聚物或者后者在PVP上的接枝聚合物可制成高吸水性软接触镜,其吸水率可高达90%,具有很好的透水、透气性及机械强度。
PVP与活性金属络合物用作加氢催化剂的研究引人注目。如以二氧化硅为载体的PVP-钯络合物,可在常温、常压下催化芳香族硝基化合物的加氢还原反应,其催化活性高于常规催化剂。对硝基苯及间二硝基苯的加氢反应收率可达100%。该体系加入适量乙酸,可显著提高其催化活性,回收使用几乎不降低催化活性。
2.5.10 在纳米材料制备领域中的应用
纳米材料的制备关键在于制备粉体材料,以纳米陶瓷粉体为例,纳米陶瓷粉体的尺寸介于原子、分子与宏观物质之间,具有显著的量子尺寸效应、表面与界面效应、小尺寸效应等,呈现一系列特殊的光、电、磁等物理化学性质,同时纳米陶瓷粉体还保持了陶瓷材料的高硬度、耐高温、耐磨损、耐腐蚀等性能,因此纳米陶瓷粉体在电子信息、航空航天、环境保护和能源、生物医药领域均有广阔的应用空间。但是由于纳米陶瓷粉体粒子的比表面积大,表面能高,具有很高的活性,处于非热力学稳定状态,且在使用过程中分散性差,易于团聚,所以在应用上还存在着技术瓶颈。对于纳米聚晶材料,由于团聚会引起颗粒异常长大,引起性能的劣化;对于纳米发光和纳米催化等直接利用纳米粉末的场合,团聚更是直接降低了材料的发光性能和催化效率。只有解决好纳米陶瓷粉体粒子在材料中的团聚问题,纳米陶瓷粉体的特殊效应才会在材料中得到很好的体现,从而使材料的力学、光学、热学等方面的性能得到较大的提高。近年的研究表明,通过PVP材料的表面修饰作用,在各种纳米粒子材料制备过程中显现出特别的效应。
有研究报道,通过用PVP作为表面改性剂,在液相共沉淀方法制备氧化铟锡[In2O3(SnO2)](ITO)材料时,可以制得分散性非常好的ITO纳米粉体材料,该纳米材料在液晶显示(LCD)、等离子显示(PDP)、有机发光二极管(OLED)、触摸屏等方面都有非常广泛的应用。
2.5.11 在其他领域中的应用
PVP在采油工业中可作为泥浆添加剂,增加黏度和固化时间,降低失水率。它是非常稳定的酸凝胶剂,用于酸裂操作。由于它对盐的浓度较不敏感,它可以在含有对水敏感的地方在高盐浓度下用作聚合物驱油的工具。在用表面活性剂驱油的地区,如在注入表面活性剂前注入PVP的水溶液,可以大大减少表面活性剂的损失。随着今后石油资源的日渐减少,三次采油技术的推进,PVP作为优良的助流剂(页岩抑制剂)将会日益得到广泛的应用。天然气开采方面,PVP作为首选的天然气水合物抑制剂,对于天然气管道内减少结晶和阻塞的形成,起到十分重要的作用。
PVP在各种类型的造纸技术中都得到了应用,不管其造纸原料来自什么。它的用途范围很大,包括改进湿强度、染料的溶解性、颜料的分散性,是脱墨、打浆、着色的优良助剂,涂料的防结块剂和助流剂,使最终纸产品光滑、防油、印刷性能好。对那些纸张涂布后仍要打湿的场合,PVP可防止纸的卷曲起皱。
PVP 是聚合物淬火剂的主要品种。聚合物淬火剂可以改善水的冷却特性,其主要优点是:
①减少发生火灾的危险性。用PVP作淬火剂可避免因用油浴而易引起的火灾。
②操作可有弹性。由控制PVP溶液的浓度、温度和搅拌等,可相应地控制一系列的冷却速度,从而使一系列的物质得以较好地完成淬火。
③用PVP作淬火剂还可降低成本。商售PVP一般是高浓度溶液,价格高于淬火用的油类,但由于淬火时只需很低浓度的PVP溶液,实际价格比用油类低得多。
④保持清洁的环境。普通的热处理车间由于有油类的残渣、淤泥,释放出有毒气体,而污染环境。用PVP作淬火剂后,仅放出水蒸气,而无上述污染。在美国,环境保护委员会已禁止许多公司使用油类淬火剂。
⑤降低操作成本。由于降低了火灾的隐患,从某种意义上来说,也就是降低成本。另外,PVP淬火溶液的比热容几乎为油类的两倍,所以PVP淬火剂的温升只需相同体积油类的一半,这样可提高淬火产量。
美国的Meszaros 在1975年首次提出PVP水溶液可用作淬火剂,最佳平均分子量为160000(即 PVP K60),最佳浓度为10%,从此PVP产品作为淬火剂在美国得到了应用,并在世界各地得到推广。
由于PVP是非植物毒性的,因此可用于植保喷雾剂、肥料和可湿性农药中。PVP的薄膜可保护在移植时叶子的葳蔫病,减轻风和霜冻的伤害。PVP可减轻种子的浸泡伤害,保护其生理机能。PVP-碘是对植物低毒的有效杀菌剂和杀虫剂。特别是在水产养殖中,可以对养殖水和养殖器具进行杀菌消毒,大大减轻细菌对鱼、牛蛙、虾等水产品造成的病害。
由于PVP的优异性能,近年来不断发现PVP有许多新的应用;采用新的聚合技术和共聚方法,聚合物的性质能进一步改进,从而打开了一些全新的应用领域。每年大约有20种出版物和25篇专利涉及这个领域,这说明PVP仍然具有不断增长的潜力。
2.6 制造企业及市场情况
2.6.1 国际制造商
PVP是水溶性高分子材料中最具特色的全合成品种之一,可以称呼其为水溶性高分子皇冠中的一颗明珠。凭借技术难度与门槛,它仅被欧美中等国家和地区所掌握,是标准的垄断型高附加值产品。同时,由于其应用领域的不断拓展,它的研究层出不穷,焕发出勃勃的生机与活力。目前已经发展到非离子、阳离子、阴离子三大类,工业级、医药级、食品级三种级别。其品种包括均聚、共聚、交联、络合等系列。PVP在长达70多年的历史中基本被德国BASF与美国ISP(后被ASHLAND收购)垄断。全球上百个国家与地区都有他们的销售。现在仍然占据着全球70%左右的份额,同时世界上其他几个国家也有少量的PVP系列产品的生产。
BASF(Badische Anilin and Sode Fabrik)公司是世界上最大的跨国化工公司之一。20世纪30年代后期化学家 Walter Reppe 发明了以Reppe法命名的PVP生产工艺并成功获得专利。同期BASF在德国路德维希港本部投产以乙炔为原料的五步法PVP生产工厂,随后陆续建设了三个从单体合成到聚合物生产的全流程工厂,奠定了BASF在PVP的领军地位。其中路德维希港本部是目前为止世界上最大的PVP生产厂;1992 年,BASF在美国盖斯马基地也开始生产NVP,投资约6500万美元建成其第二大全流程工厂。
随着中国企业的崛起,BASF在第二次世界大战后确立的全球垄断地位受到强烈冲击。在低端市场基本被中国企业所击败,在中高端市场凭借其稳定的质量与优良的品牌仍然占据世界霸主的位置。但高端市场美国ASHLAND(原ISP)步步紧逼,中国企业又强劲向中高端的化妆品、食品、医药等市场挺进,陆续蚕食BASF原有的版图。更有以宇昂科技为代表的中国新生企业,不仅在产品的品种、成本、质量、品牌上充分竞争,更在成立行业协会、建立产学研联盟、牵头制定国家标准等更多维度上展开争夺话语权的全面竞争。
在这种新形势下,BASF不甘人后积极求变,一改前70多年的沉稳保守的打法,主动出击,创新发展。
在沉寂多年后,2015年年初BASF重磅出击,宣布对已有两个主要的PVP生产基地进行改建扩容,同时宣称在中国上海建立全新的PVP生产基地。一方面降低生产成本,缩短生产周期,加快物流中转速度,规避之前被客户所诟病的大象病(行动迟缓,决策冗长,服务傲慢)。另一方面紧盯中国市场,加紧中国的本土化,规避未来因中国PVP国家标准出台所带来的潜在风险。
至此BASF的PVP系列产品总产能估计可达到2.5万吨/年以上。
美国国际特品(ISP)公司前身是GAF(General Aniline and Film Co.),1990年改名为ISP(International Specialty product Co.)。它是美国500家大公司之一,也是世界上唯一可以与BASF竞争的以PVP系列产品为主要经营方向的专用化学品生产商。它于1956年在美国德克萨斯州德克萨斯市(Texas City,Texa)建立了该公司第一套,也是世界第二套从乙炔开始的PVP全流程工厂;1969年在美国肯塔基州卡尔弗特市(Calvert City,Kentucky)建立第二套生产PVP的装置;2011年6月22日ISP被亚什兰集团以32亿美元收购,并将其与已收购的亚跨龙功能性添加剂(AAFI)合并,成立亚什兰特种添加剂(Ashland Specialty Ingredients,ASI)部门。2016年10月,亚什兰宣布鉴于中国市场需求量的不断增加,以及新的质量监管的要求决定开启中国南京的辅料生产基地,主要生产维生素和PVP产品。亚什兰PVP的预计总产能已经高于BASF,估计可达3万吨/年。
值得强调的是,美国ISP与德国BASF在进入中国长达30年的时间里,仅仅将中国作为一个低端产品的销售市场,从来不考虑在中国投资设厂并将PVP技术转让给中国。但在中国企业依靠自己实力强势崛起并建立起自己的PVP国家标准时,他们却不约而同将PVP工厂建立在中国,希望在中国的经济发展中争得一席之地。这说明中国只有自身强大才有话语权。
美国另有2家生产企业Hichson Danchem公司和Thatcher公司,其中Hichsom Danchem公司几乎停止了PVP的生产,而Thatcher公司在PVP领域中主要以生产PVPI为主。
德国主要是BASF公司在德国路德维希港的生产基地。
日本有1家BASF和ISP公司的合资企业,此外还有日本触媒(Nippon Shokubai)和DKS(Dai-ichi Kogyo Seiyaku)公司也生产PVP,其中日本触媒于2003年开始生产PVP,也采用GBL法生产NVP单体,但催化剂始终有问题。主要生产高分子量的PVP K90产品,2007年扩产后产能为3500t左右,随后日本触媒公司与住友化学工业股份有限公司交换产业,接受其丙烯酸产业(设立爱媛工厂)后逐渐退出了PVP市场,到目前为止已经停止生产PVP产品。
俄罗斯Sintvita公司早期生产小分子量的PVP K15和PVP K17产品,生产能力约850t/年,由于设备老化、装置闲置已不再进行新的大规模投入。
伊朗也有小的生产装置,主要是Rahavard Tamin Co公司通过购买NVP来进行后续生产,于2010年获得了GMP,形成了较为稳定的PVP供应,产能大约800t/a。伊朗的NVP主要购买于中国。
印度2000年以后从中国购买了PVP的生产技术也开始进入PVP市场,其中Balaji公司于2013年进行PVP产品生产,基本形成全流程化生产,产能大约800t/a。另外,印度有将近七家PVPI粉的生产商,其中最大的为GAL 公司,年产能约350t;总计产能约750t/年;印度PVPI粉70%用于直接出口,另外30%多用于当地PVPI乳膏及溶液的生产。值得注意的是因为中国PVP受到海关出口退税问题制约,出口增速远低于印度。目前PVPI的国际低端市场基本被印度所垄断。上海宇昂公司的高稳PVPI目前在中国出口额占第一,但与BASF、ASHLAND相比还有相当大的差距。
2.6.2 中国制造商
我国PVP的生产与应用起步相对较晚,在产品的技术开发和市场应用的研究方面与国外存在较大的差距。1987年,浙江省化工研究院以吴稼祥教授为代表的PVP项目组承担了国家“七五”重点科技攻关项目,将PVP的合成技术在小试阶段取得的成功经验应用于工业化生产,这对于我国的PVP事业具有里程碑的意义。
1997年,东胜精攻石油开发集团股份有限公司、浙江省化工研究院和上海浦发企业发展有限公司合资在上海浦东新区成立了上海胜浦新材料有限公司,并在山东东营市建立了一套500t/a PVP的GBL法生产装置。该装置为中国第一个以GBL为原料合成单体NVP的工业化生产装置。这代表着中国有了不同于BASF和ASHLAND乙炔法生产工艺的专有技术。
21世纪初,上海胜浦新材料有限公司、博爱新开源和杭州南杭工贸有限公司这三家企业逐渐发展壮大。2004年上海胜浦新材料有限公司改制关闭,一大批从事PVP行业的精英纷纷从该企业中走出来,成为我国PVP行业技术、营销以及应用领域的主要力量,支撑起了整个PVP行业的发展和进步。其中原胜浦公司的总经理王宇励精图治在上海浦东的金苹果民居创业,历经十一年拼搏,不仅创造了一个上市企业宇昂科技的奇迹,而且联合中国PVP主要企业制定了PVP的两项国家标准。至此,中国PVP有了自己的核心自主知识产权,与欧美巨头的竞争从单纯的成本、质量之争上升到品牌及标准之争。
在全球市场强劲需求的推动下,我国PVP的生产、研发和应用都取得了新的进展,品种不断增多,产品质量也得到了更进一步的提高,成为全球除德国BASF和美国亚什兰以外最主要的PVP生产国。
随着国内顺酐常压气相加氢和BDO脱氢环化生产GBL的技术开发成功和推广使用,上游原材料的生产厂家不断增多,我国GBL的产量逐年增加,从而为我国PVP的生产提供了稳定而充足的原料供应。
2002年我国PVP的主要生产企业有5家,当年全国总的生产能力将近5000t,实际产量约3500t,开工率为70%。
2003年我国PVP的主要生产企业有7家,新增的企业均为直接购买NVP单体进行聚合生产PVP系列产品,或购买PVP进行PVPI生产。全国总生产能力近6500t,同比上一年产能增长率为30%,实际产量约4700t,开工率为72.3%,同比上一年产量增长率为34.3%。
2004年我国PVP的主要生产企业有9家,新增的企业不仅拥有PVP的生产装置,还可以提供PVP的聚合原料。全国总的生产能力近9000t,同比增长38.5%,实际产量约6700t,开工率为74.4%,同比产量增长42.6%。开工率和产量同时增长的原因主要是市场需求量的增加从而促进了国内PVP的产量增加。
2005~2010年期间新增3家企业,其中2家可提供PVP生产原料,到2010年我国主要的PVP生产企业有12家。全国总的生产能力约1.3万吨,比2004年同比增长44.4%,实际产量约8300吨,开工率为63.8%,产量比2004年增加23.9%。开工率下降的原因主要是我国PVP生产厂家增加,供大于求,同时2008年金融危机也造成市场需求量下降。
截至2016年,我国PVP的主要生产企业有21家,2012年以后新增生产企业中只有一家生产NVP单体,其余均为直接生产PVP聚合物的企业。至此,全国PVP设计产能估计可达5.23万吨,但2016年全年产量仅有约1.5万吨,按PVP生产厂家设计产能计算开工率仅为28.7%。近年来,中国PVP的整体行业呈现明显的产能过剩的局面,究其原因主要是越来越多新的生产企业看中PVP市场的巨大用量及前景纷纷投入生产。BASF和ASHLAND也放下高傲的身段觊觎中国PVP的巨大市场潜能,纷纷在中国建立新的生产线抢占市场份额,这造成了中国PVP产能无序增长过快,从而生产厂家开工率大幅下降的局面。
这种完全市场化的充分竞争一方面对PVP生产企业提出挑战,要求他们从生产成本、生产工艺、产品质量上加强控制。另一方面这也是个优胜劣汰的自然选择过程。现阶段中国PVP市场呈现出强者恒强,弱者旋弱的局面。相信年轻的中国PVP行业还有个重组兼并螺旋上升的时间和过程。这是发展过程的阵痛,也是发展的必然规律。我们相信中国的PVP领军企业会在不远的将来与BASF、ASHLAND三足鼎立,在全球发出中国的声音。
与此同时,我们也应该看到PVP新的应用领域的实际容量还没有完全打开,除医药、化妆品、工业等传统应用领域发展稳健外,其他新兴应用领域,例如:医药新产品、环保水处理、新能源开采、新型特种涂料、酿酒和饮料、印刷、养殖、纳米科技、陶瓷应用等均是PVP未来将广泛应用的领域,但要实现大规模推广和应用还需要一段时间的市场过渡,因此,供应过剩只是暂时表象,PVP未来的发展无可限量。
2.6.3 市场情况
从全球产量占比来看,BASF与ASHLAND一直垄断着全球70%左右的市场份额,但其份额呈逐年递减的趋势。2014年以后,随着中国PVP产业的升级,以及中国药品管理规范GMP实施的逐渐严格,中国PVP产品质量不断提高,已经赢得越来越多海内外客户的认可,凭借质优价廉、灵活主动的优点,中国PVP逐渐扩大着全球PVP市场份额。到2016年,全球PVP市场份额见图2-25。

图2-25 2016年全球PVP销售占比
2016年全球PVP应用领域分布情况见图2-26。

图2-26 2016年全球PVP应用领域分布情况
因为数据取得的不完整性,我们初步预估2015~2020年全球PVP消费量年均复合增长率为7.6%左右,2020年全球PVP消费量将达到约12.5万吨。
其中,以最具发展潜力的聚维酮碘产品来看,预计2020年,全球聚维酮碘的需求量将达到2.5万吨/年,实现直接产值约5亿美元。在中国市场,它不仅将成为出口创汇的主要高附加值PVP产品,也将同步带动国内聚维酮碘相关产业,如医疗消毒、器械消毒、水产养殖业消毒、环境消毒等各终端领域,中国将占领超过全球40%的聚维酮碘份额,原料产值将达20亿元,预计实现终端联动产值约500亿元,如图2-27和图2-28所示。

图2-27 预计2020年全球聚维酮碘市场份额

图2-28 预计2020年中国聚维酮碘市场份额
参考文献
[1]Haaf F,Sanner A,Straub F.Polymers of N-Vinylpyrrolidone:Synthesis,Characterization and Uses[J].Polym J,1985,17(1):143-152.
[2]严瑞煊.水溶液性高分子[M].北京:化学工业出版社,2010:217.
[3]崔英德,易国斌,廖列文.聚乙烯吡咯烷酮的合成与应用[M].北京:科学出版社,2001.
[4]曹军.N-乙烯基吡咯烷酮的合成工艺研究[D].杭州:浙江大学,2015.
[5]JP 40792[P].1972.
[6]崔英德,易国斌.Catalysts for synthesis of N-Vinylporrolidone[J].化工学报(英文),2000,51(4):443-445.
[7]BrunoP,Leon K,Lester H.Process for theproductionofn-vinylpyrrolidone-2:US,2775599[P].1956.
[8]崔英德.聚乙烯吡咯烷酮(PVP)合成新工艺的研究[D].广州:广州华南理工大学,1996.
[9]张光华,康正等.N-乙烯基吡咯烷酮聚合反应的研究[J].山东化工,2001,30(06):10-11.
[10]Senogles E,Thomas R.J Polymer Science:Symposium,1975,49:203-210.
[11]Chi-san W,Larry S,James C,et al.Vinyl pyrrolidone homopolymer and copolymers:SEC analysis [M].Encyclopedia of Chromatography,2005.
[12]马丽.乙烯基吡咯烷酮均聚物与共聚物的制备新方法研究[D].合肥:合肥工业大学,2003.
[13]Dirk H,Bernd R.Pulverulent styling composition:US,233071A1 [P].2008.
[14]Fikentscher H,Die Messung der Viskosität solvatisierter Sole[J].Mordern Plastics,1945,23(3):157.
[15]Sugiura M,Fujii E.Chem Abstr,1964,60:9369.
[16]Tan Y,Challa G.Polymer,1976,17:739.
[17]Miller M.The Structure of Polmers[M].New York:Reinhold,1966:291.
[18]李卓.非晶高聚物粉体玻璃化转变特性及分散稳定性[D].大连:大连理工大学,2005.
[19]Fikenscher H,Herrle K.Polyvinylpyrrolidone,1945.
[20]Kaori Takikawa.C hem Pharm Bull,1978,26(3):874.
[21]徐桂英.日用化学工业,1998,5:1.
[22]Arai H,Shinoda K.J Colloid Interface Sci,1971,37:231.
[23]Jeresa Gaicia Lopez de Sa,Luis M Garrido Fernandez,Js Allende Riando.J British Polym,1988,20:39.
[24]周志永.新编药物手册[M].上海:金盾出版社,1992:389.
[25]Chem Pharm Bull,1979,26:1223.
[26]施丽西.稳定的硝酸甘油舌下片的进展Ⅱ.含PVP片剂的处方和评价[J].国外医学参考资料药学分册,1977,01.
[27]罗云,马红斌,蔡鸿生.扑热息痛分散片制备及质量控制[J].现代应用药学,1996,13(3):34-35.
[28]Ludwigshaten.Soap/Csmetic/Chemical Specialties,1989,4:42.
[29]Vogel F.Cosmetic and Toiletries,1985,43:100.
[30]汪立德.现代化工,1995,9:21.
[31]俞剑飞.食品与发酵工业,1987,3:55.
[32]特开昭62-61 569.1987.
[33]特开平 9-220 055.1997.
[34]U S,5587 191.1996.
[35]崔英德.聚乙烯吡咯烷酮(PVP)合成新工艺的研究[D].广州:华南理工大学,1996.
[36]李步海等.高等学校化学学报,1990,11(4):336.
[37]Chavanne P,et al.Anal Chim Acta,1958,19:377.