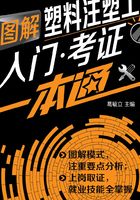
第2章 塑料成型基础
2.1 塑料的成型性能
2.1.1 吸湿性
吸湿性是指塑料对水分的亲疏程度。按照吸湿或黏附水分能力的大小,可将塑料分为吸湿性塑料和不吸湿性塑料两大类。前一类塑料能够吸湿或黏附水分,如聚酰胺、ABS、聚碳酸酯、聚苯醚和聚砜等。后一类塑料的吸湿或黏附水分很小,如聚乙烯、聚丙烯、聚苯乙烯和氟塑料等。
吸湿性塑料在注射成型过程中极易发生水降解,成型后塑件上容易出现气泡、银丝、斑纹等缺陷。因此,在成型前必须进行干燥处理,必要时,还可以在注塑机料斗内设置红外线加热装置,以免干燥后的塑料进入机筒前在料斗中再次吸湿。
2.1.2 收缩性
塑件从温度较高的模具中取出冷却到室温后,其尺寸或体积会发生收缩变化,这种性质称为收缩性。收缩性的大小以单位长度塑件收缩量的百分数来表示,称为收缩率。由于成型模具与塑料的线膨胀系数不同,收缩率分为实际收缩率与计算收缩率两种,其计算公式如下:
(2-1)
(2-2)
式中 Ss——实际收缩率;
Sj——计算收缩率;
a——模具或塑件在成型温度时的尺寸;
b——塑件在室温时的尺寸;
c——模具在室温时的尺寸。
实际收缩率表示塑件实际所发生的收缩。由于成型温度下的塑件尺寸不便测量以及实际收缩率和计算收缩率相差很小,因此生产中常采用计算收缩率,但在大型、精密模具成型零件尺寸计算时则应采用实际收缩率。
引起塑件收缩的原因除了热胀冷缩、脱模时的弹性恢复以及塑性变形外,还与注射成型时的许多工艺条件和模具因素有关。此外,塑件脱模后残余应力的缓慢释放和必要的后处理工艺也会使塑件产生后收缩。因为影响塑料收缩率变化的因素很多,而且相当复杂,所以收缩率是在一定范围内变化的。在模具设计时,应根据上述因素综合考虑选取塑料的收缩率。
2.1.3 相容性
相容性是指两种或两种以上不同品种的塑料,在熔融状态不产生相互分离现象的能力。如果两种塑料不相容,那么混熔后塑件会出现分层、脱皮等质量缺陷。不同塑料的相容性与其分子结构有一定关系,分子结构相似的塑料比较容易相容,如高压聚乙烯、低压聚乙烯和聚丙烯彼此之间容易混熔。分子结构不同的塑料很难相容,如聚乙烯和聚苯乙烯之间的混熔。
塑料的相容性又称为共混性。因为塑料的这一性质,可得到类似共聚物的综合性能,这是改进塑料性能的重要途径之一,例如聚碳酸酯和聚丙烯塑料混熔,就能改善聚碳酸酯的脆性,提高熔体的流动性。
2.1.4 热敏性
热敏性是指塑料的化学性质对热量作用的敏感程度,热敏性很强的塑料称为热敏性塑料。热敏性塑料在成型过程中极易在不高的温度下发生热降解,从而影响塑件的性能、色泽和表面质量等。同时,塑料熔体发生热降解时会释放出一些具有挥发性的气体,这些气体对人体、模具和注塑机都有刺激、腐蚀作用或毒性。为避免热敏性塑料在成型过程中出现降解现象,应采取相应的措施,如选用螺杆式注塑机;流道截面取大一些,以避免产生过大的摩擦热;注塑机料筒内壁、流道和模腔表壁镀铬;模具内禁止有死角,以避免熔体在模内流动时发生滞料;生产时严格控制成型工艺条件等。必要时可在塑料中加入热稳定剂。常见的热敏性塑料有硬聚氯乙烯、聚氯乙烯、醋酸乙烯共聚物、聚甲醛和聚三氟氯乙烯等。
2.1.5 流动性
塑料在一定的温度、压力作用下充填模具型腔的能力,称为塑料的流动性。塑料的流动性差,就不容易充满型腔,易产生缺料或熔接痕等缺陷,所以需要较大的成型压力才能成型。相反,塑料的流动性好,能够用较小的成型压力充满型腔。但流动性太好,会在成型时产生严重的溢边。
流动性的大小和塑料的分子结构有关。具有线型分子而没有或很少有交联结构的树脂流动性大。塑料中加入填料,则会降低树脂的流动性,而加入增塑剂或润滑剂,则可增加塑料的流动性。
设计模具时,设计人员习惯通过塑料的溢料间隙来确定浇注系统的尺寸、模具零件间的配合间隙等。所谓溢料间隙是指熔体塑料在成型高压下不得溢入的最大间隙值。根据溢料间隙大小,塑料的流动性分为好、中等、差三个等级。表2-1是常用热塑性塑料溢料间隙与流动性的关系。
表2-1 常用热塑性塑料溢料间隙与流动性的关系

热固性塑料的流动性通常以拉西格流动值来表示,拉西格流动值越大,则表明流动性越好。表2-2是热固性塑料流动性等级及应用。
表2-2 热固性塑料流动性等级及应用

2.1.6 比容和压缩率
比容是指单位质量的松散塑料所占的体积,单位为cm3/g;压缩率是指塑料的体积与塑件的体积之比,其值恒大于1。比容和压缩率均表示粉状或短纤维状塑料的松散性,它们都可用来确定模具加料室的大小。另外,比容和压缩率较大时,塑料内充气增多,排气困难,成型周期变长,生产率降低;比容和压缩率较小时,压缩、压注容易成型,而且压锭重量也较准确。但比容太小,则影响塑料的松散性,以容积法装料时引起塑件重量不准确。
2.1.7 水分和挥发物
塑料中的水分和挥发物,一方面来自塑料自身,另一方面则来自成型过程中塑料发生化学反应的副产物。塑料中水分和挥发物的含量对塑件的物理、力学和介电性能都有很大的影响。塑料中水分及挥发物含量大时,塑件易产生气泡、内应力以及塑性变形,使机械强度降低。压制时,由于温度和压力的作用,大多数水分和挥发物会逸出,但尚未逸出时,它将占据着一定的体积,这会严重阻碍化学反应的有效发生,其结果是当塑件冷却后,会导致组织疏松。当逸出时,挥发物气体又像一把利剑一样割裂塑件,使塑件产生龟裂,降低机械强度及介电性能。此外,水分及挥发物含量过多时,会促使流动性过大,容易溢料,成型周期变长,收缩率增大,使塑件容易发生翘曲、波纹及光泽不好等现象。但是,塑料中水分和挥发物的含量不足,也会导致流动性不良,成型困难,同时也不利于压锭。水分和挥发物在成型时变成的气体必须排出模外,因为有些气体对模具有腐蚀作用,对人体也有刺激作用。为此,设计模具时应对这种特征有所了解,并采取相应的措施。
2.1.8 硬化速度
硬化是指塑料成型时完成交联反应的过程。硬化速度通常以塑料试样硬化每1mm厚度所需的秒数来表示,此值越小,硬化速度越快。硬化速度和塑料品种、塑件形状、壁厚、成型温度及是否预热、预压等有密切关系。例如,采用压锭、预热、提高成型温度以及增长加压时间等措施,都能显著加快硬化速度。此外,硬化速度还应满足成型方法的要求。例如,压注或注射成型时,应要求在塑化、填充时化学反应慢,硬化慢,能够保持长时间的流动状态,但当充满型腔后,在高温、高压下应快速硬化。硬化速度慢的塑料会使成型周期变长,生产率下降;硬化速度快的塑料,则不能成型复杂的塑件。