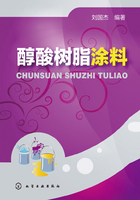
第四节 无油醇酸(饱和聚酯)树脂制造
一、概述
由多元醇与多元酸经酯化缩聚反应得到线型结构的热塑性高聚物,与不饱和聚酯相对应的是分子结构中不含非芳香烃的不饱和键,习惯上称为饱和聚酯树脂。饱和聚酯树脂是树脂行业非常重要的一大类产品,在人们的日常工作和生活中应用很广,如纤维用聚酯、薄膜用聚酯、塑料用聚酯等用量都很大,涂料用饱和聚酯树脂仅仅是其中用量较少的一种。
饱和聚酯树脂也是以多元醇与多元酸的酯键为主链,和醇酸树脂分子结构有相似之处,不同之点是饱和聚酯树脂侧链上一般不含植物油脂肪酸,业内多称之为无油醇酸树脂,可看成是不干性醇酸树脂的特例,在应用理论与工艺实践上和醇酸树脂也很相似。
1847年Berzelius用甘油和酒石酸通过化学反应合成了最早的聚酯树脂,1901年Watson Smith采用邻苯二甲酸酐与甘油制成了聚酯树脂,1925年前后才由不饱和脂肪酸改性的甘油和苯酐反应合成了最早的醇酸树脂,从而迎来了醇酸树脂在涂料行业的应用,并得到了飞速发展。
涂料用的饱和聚酯树脂有羟基型聚酯树脂和羧基型聚酯树脂,本身是热塑性树脂,一般要用其他的固化剂交联成热固性涂膜。羟基型聚酯树脂多用氨基树脂和聚氨酯树脂交联剂固化成膜,涂膜的耐候性、保光保色性优良,这就是行业内用量大、性能优良的两大类主流工业涂料:氨基聚酯树脂涂料和聚酯聚氨酯涂料。广泛用于轻工、家电、汽车、卷材、食品罐头。羧基型聚酯树脂用以制粉末涂料,用环氧树脂和专用固化剂交联成膜,分别为聚酯-环氧粉末和纯聚酯粉末,也是国内粉末涂料的主流产品。
我国从20世纪70年代早期发展了生产溶剂型涂料的饱和聚酯树脂,由于原料来源的限制和工业发展缓慢,饱和聚酯树脂品种和应用范围长期受到局限。1985年上海振华造漆厂为了与上海宝山钢铁总厂的卷材生产流水线配套,从美国引进PARKER CO的预处理技术和RELANCE UNIVERSAL CO系列卷材涂料,使国内聚酯树脂和涂料进入了一个新的发展阶段。现阶段国内各大钢厂和一些经济发达地区建设了许多卷材生产线,卷材涂料的需求大幅度上升,大大推动了相关的聚酯树脂的生产与技术的进展,从而也带动聚酯树脂生产原料的特殊多元醇、多元酸及功能性单体开发成功,使饱和聚酯树脂的原料来源极为丰富,使聚酯树脂品种能够满足国内轻工、家电、汽车、罐头、卷材、粉末涂料等产业迅速发展的要求。这主要是指羟基型聚酯树脂的发展概况,羧基型聚酯树脂是随粉末涂料兴起而发展的。不饱和聚酯树脂将在第九章介绍。
二、羟基型饱和聚酯树脂
(一)原料
饱和聚酯树脂所用的基本原料是多元醇、多元酸、溶剂和助剂,和醇酸树脂大同小异。
1.多元醇
饱和聚酯树脂生产过程中,一般选用含有伯羟基的多元醇。饱和聚酯树脂常用多元醇及其参数见表3-23。
表3-23 饱和聚酯树脂常用多元醇及其参数

聚酯树脂生产中,需要使用三官能团多元醇时,一般采用三羟甲基丙烷而不用甘油,其原因在于保证所有羟基都是伯羟基,活性一致,而且活性比较高。
2.多元酸
饱和聚酯树脂常用多元酸及其参数见表3-24。
表3-24 饱和聚酯树脂常用多元酸及其参数

设计聚酯树脂配方时,若要满足性能的要求,应综合考虑树脂柔韧性、硬度、耐候性、弯曲等性能的平衡,并结合成本因素,一般选用两种或两种以上的多元醇和多元酸。
3.溶剂
聚酯树脂生产中,酯化阶段也需溶剂共沸脱水,将酯化反应产生的水带出体系之外,使酯化反应得以继续进行;还有就是溶解与稀释树脂,和在醇酸树脂中起的作用一样。
饱和聚酯树脂常用溶剂及其参数见表3-25。
表3-25 饱和聚酯树脂常用溶剂及其参数

注:乙二醇丁醚是禁用产品,可用丙二醇丁醚代替。
4.催化剂和抗氧剂
(1)催化剂
生产饱和聚酯树脂,有时需用催化剂,以缩短工时,减少副反应。选择的催化剂应符合以下要求。
①接近中性,对设备无腐蚀作用。
②催化剂不参与到反应产物中,但残留在体系之中,要考虑其与聚酯树脂的相容性,不能影响最终产品质量。
③能明显缩短酯化反应时间,但要在可控的范围内。
④选择性要好,能使反应向酯化反应方向进行,减少多元醇间的脱水及氧化等副反应。
⑤反应生成水不会使其失效。
⑥选定某种催化剂后,一般不宜轻易更换,不同企业生产的同一类型催化剂,会有一些差异,没有通过试验,不可直接替代,以免造成生产控制的困难。
目前国内外酯化反应催化剂大多数是采用有机锡化合物。一般采用的是丁基氧化锡或丁基氧化锡的衍生物,是一类抗水解、用量少、催化活性高的酯化反应催化剂,目前国内常用的有以下几种。
①二丁基二月桂酸锡,是浅黄色或无色油状液体,低温呈白色结晶体,溶于甲苯、乙醇、丙酮等有机溶剂,不溶于水,锡含量17%~19%,一般使用量为反应物的0.20%~0.25%。
②单丁基氧化锡,是白色粉末,不溶于水和大部分有机溶剂,但溶于强碱和矿物酸中,锡含量≥56%,一般使用量为反应物的0.05%~0.10%。
上述两个酯化催化剂,目前的市场价格单丁基氧化锡约为二丁基二月桂酸锡的1倍,但单丁基氧化锡在使用量为二丁基二月桂酸锡1/3~1/2情况下,其酯化反应时间可比使用二丁基二月桂酸锡缩短1/4~1/3。
生产过程中,可以根据聚酯树脂的生产状况,选择合适的催化剂,并确定加入量,在一般情况下,以选择单丁基氧化锡为主。但有机锡类是要逐步禁用的产品,需要开发低毒高效品种来代替。
(2)抗氧剂
抗氧剂是一种可降低氧化速率,进而减缓聚合物老化的化学助剂,通常只要加入微量的抗氧剂就非常有效。树脂合成中引入抗氧剂主要能减缓氧化反应速率,从而可达到降低树脂色泽,提高树脂贮存稳定性,也能提高涂料的稳定性。
目前饱和聚酯树脂使用的抗氧剂类型如下。
①酸性抗氧剂 主要有硼酸、亚磷酸、次磷酸等,以次磷酸的效果为优。次磷酸抗氧效果明显,价格相对低廉,但次磷酸的酸性较强,要考虑对设备材质的腐蚀性。
②亚磷酸酯类抗氧剂 常用的有亚磷酸三苯酯、亚磷酸三(2,4-二叔丁苯基)酯(168)、三壬苯基亚磷酸酯(TNPP)等,具有分解过氧化物产生结构稳定物质的作用,有抗氧效果。
从实际生产情况看,将亚磷酸酯类抗氧剂、酸性抗氧剂单独或复配使用,效果理想。
选择聚酯树脂抗氧剂时要注意其减色效果,小试和车间生产会有差异,需要仔细确认。
抗氧剂最后会残留在体系之中,因此需要考虑与聚酯树脂的相容性,即不能影响树脂的过滤性和最后的涂料性能。若同时使用催化剂与抗氧剂,要考虑催化剂与抗氧剂的性能是否相互抵触。例如,单丁基氧化锡和次磷酸若同时使用时,会影响聚酯树脂的透明度,导致涂膜光泽下降。
(二)羟基型饱和聚酯树脂合成的基本问题
1.酯化缩聚反应
酯化缩聚反应的特点和醇酸树脂一样,即每一步反应的速率和活化能大致相同,反应过程中生成的二聚体、三聚体、四聚体及多聚体上的官能团等活性,反应体系中分子是逐步聚合增长成大分子。为获得线型树脂,要控制体系的平均官能度(平均官能度计算方法见本章第一节)。溶剂型醇酸树脂主要是用一元脂肪酸(植物油)调节平均官能度,如用四元醇,还要增加醇超量调节官能度。
2.聚酯树脂的重要参数
(1)醇超量
醇超量表达式为:
式中,R为醇超量;eA为配方中多元醇当量数;eB为配方中多元酸当量数。
从理论上说,平均官能度为2的配方体系不会胶化,若有3官能团或以上的原料存在,理论平均官能度大于2,试验时应注意反应速率。树脂的羟值是饱和聚酯树脂的关键参数,可调节体系平均官能度,保证生产工艺稳定,再者,因为树脂中的羟基要与氨基树脂或异氰酸酯树脂交联。羟值的大小、分布情况、种类是影响交联情况的关键因素。从实际生产的饱和聚酯树脂分析羟值大小,用于制备的树脂考虑到反应过程中多元醇的升华损耗等,理论设计时的羟值应大于上述推荐的实测羟值,通过大量的树脂生产积累了理论羟值与实测羟值的偏差。一般实测羟值/理论羟值≈70%~80%,若升华损耗小些,实测羟值/理论羟值>80%,若升华损耗大些,实测羟值/理论羟值<70%。
从羟基分布来看,分子链两端的羟基具有更高的反应活性。从羟基的种类分析,伯羟基具有更高的反应活性。根据树脂的应用方向,合理设计树脂的羟值,是我们在设计配方时要考虑的问题。
聚酯容易合成,单体来源也很丰富,因而性能具有很大的可调性,然而酯基不耐水。聚合时,二元醇中以新戊二醇较为理想,与乙二醇比较,可以大大改善树脂的耐水性,它们的结构如图3-13所示。

图3-13 新戊二醇聚酯和乙二醇聚酯的结构
将其结构中羰基上的氧作为起点,逐次将原子标上位数,数出6位和7位的原子数,然后按下式计算立体因子:
立体因子=4×(6位的原子数)+(7位的原子数)
新戊二醇聚酯6位和7位的原子数分别为3个和9个,立体因子为21;而乙二醇聚酯只有3个6位原子和1个7位原子,立体因子为13。根据6位和7位经验规律,立体因子值越高,水解稳定性越好。因此,新戊二醇聚酯的耐水性远超过乙二醇。同理,如果使用其他支化的二元醇,如2,2,4-三甲基-1,3-戊二醇,其水解稳定性也会大大提高。
(2)分子量
聚酯树脂大量用作涂料成膜物,要求有一定的强度,聚合物强度随分子量的变化如图3-14所示。A点是初具强度的最低分子量,A点以上的强度则随分子量的增加而迅速增加,到临界点B以后,强度的增加逐渐减慢;C点以后,强度不再显著增加,过高的分子量反而会影响涂料的工艺性能。在平均分子量相同的情况下,较宽的分子量分布,会有较好的工艺性能,而强度可能下降。一般来说,使用在面漆中的饱和聚酯树脂其数均分子量一般在10000以内,而用于底漆的饱和聚酯树脂其分子量一般在10000以上,有的可达15000以上。

图3-14 聚合物相对强度与分子量的关系
(3)聚酯树脂的玻璃化温度(Tg)
树脂的玻璃化温度是影响涂料韧性、硬度、耐划伤性的关键因素。高的玻璃化温度能赋予涂膜较好的硬度和耐划伤性,较低的玻璃化温度能为树脂提供抗冲击性。一般来说,玻璃化温度在20~40℃的树脂用于生产卷材涂料,其中,面漆所用的树脂玻璃化温度较底漆用树脂稍高,这是因为面漆要考虑涂膜的硬度和耐划伤性,而底漆的柔韧性则较为关键。
3.配方估算
缩聚终点预测、配方的计算与验证和醇酸树脂相同,采用卡氏公式。
【例8】设计一个快干型的饱和聚酯树脂,其指标要求:固含量60%,酸值≤6mg KOH/g,分子量5000~7000。
原料的确定:根据涂料快速固化及耐候性、柔韧性和硬度的要求,首先确定合成树脂需要的原料。
新戊二醇:耐水解性好,耐候性好。
甲基丙二醇:溶解性好,价格相对低廉。
间苯二甲酸:羧基位阻小,有利于提高分子量,耐候性好。
己二酸:具有较长的无支链的直链结构,分子链旋转角度大,柔韧性与耐候性好。
苯酐:溶解性好,价格相对低廉,也有利于硬度。
偏苯三酸酐:形成体型缩聚产物,能提高交联密度,有利于硬度和耐甲乙酮擦洗性。
催化剂:单丁基氧化锡。
回流与稀释用溶剂:回流脱水与调整树脂含量、黏度用。
树脂参数的确定:按前面提供的经验数据,羟值取中间值70mg KOH/g,按实测羟值/理论羟值≈70%~80%经验值,理论羟值按90~100mg KOH/g计,平均官能度按2.075计,醇超量按1.20计。
配方的确定:整个配方中多元酸的当量按1.0计,则多元醇当量按1.2计;根据聚酯树脂柔韧性和硬度平衡性方面的要求,采用己二酸、偏苯三酸酐、间苯二甲酸与苯酐各自的性能和特点确定其配比,间苯二甲酸和苯酐总当量数可按60%~70%计(间苯二甲酸/苯酐按60/40考虑),己二酸、偏苯三酸酐当量数分别在15%~20%和10%~15%的范围内选择。
(三)羟基型饱和聚酯树脂合成的工艺过程
1.分阶段酯化工艺
(1)多元酸的二次投料
多元醇分子链上的羟基与多元酸分子链上的羧基,需要达到一定温度,才会发生酯化反应,不同烃基结构的多元酸与多元醇反应活性不同,发生反应的温度也不同,饱和聚酯树脂合成中常用的多元酸是对苯二甲酸和间苯二甲酸等,与多元醇的起始反应温度都高于与苯酐的反应温度。合成聚酯树脂所采用的各种结构不同的多元酸,与多元醇反应的竞聚率不同,因此与多元醇反应时,竞聚率高的多元酸与多元醇反应快,而竞聚率低的多元酸与多元醇反应慢,难以顺利地接到聚酯分子链上,当然多元酸的反应活性与多元酸所占比例也有关系。
为得到均衡的树脂分子链,保证树脂有优异的性能,根据树脂所采用的多元酸的情况,为保证竞聚率低的多元酸与多元醇的充分反应,一般可采用将竞聚率高的多元酸后投料(二次投入)的方式,这样刚开始反应时,没有竞聚率高的多元酸参与竞争,可保证竞聚率低的多元酸与多元醇反应顺利进行,反应达到一定程度后再加入反应性强的多元酸,可得到分子链结构分布适宜的饱和聚酯树脂。
根据配方中多元酸反应活性的差异情况,多元酸可采用一次投料或二次投料,使用对苯二甲酸的配方,多元酸大多采用二次投料。
(2)熔融(聚合)反应
熔融反应是指无溶剂状态下进行酯化反应与缩聚反应,生产饱和聚酯树脂时,起始投料时,回流溶剂并不投入,多元醇、多元酸升温熔化成为均相后,体系是在无溶剂的熔融状态下反应,等熔融反应进行到一定阶段,聚酯树脂达到一定分子量后,再加入回流溶剂进行回流反应阶段,直至反应达到要求。
聚酯树脂合成常用的新戊二醇、甲基丙二醇等多元醇,升华温度较低,若反应起始时采取熔融酯化的工艺,没有沸腾的溶剂,直冷凝器中的气相温度可通过控制冷却水来控制,可减少多元醇的升华损失,避免不必要的原料消耗。若反应起始就采用将回流溶剂与多元醇、多元酸同时投入的工艺,在回流反应时,溶剂处于沸腾的状态,气相温度较高,且受沸腾溶剂的影响,难以下降,多元醇很容易升华而损耗,影响了与多元酸反应的状况,难以得到清澈透明的树脂,要解决这个问题,只有增加多元醇的投料量才有可能,这势必增加聚酯树脂的原料成本,从技术经济的角度看,极不合理。
在熔融酯化阶段要通入惰性气体(CO2或N2)。反应釜与大气通过平衡管(放空管)连通,维持压力平衡,保证熔融反应在常压下进行。熔融反应开始前,已有较高的温度,反应物与大气直接接触,易产生氧化聚合反应,造成物料色泽变深。为避免这种情况,可在投料完毕后,升温的同时通入惰性气体,利用惰性气体来隔绝反应物与空气的接触,防止氧化的发生。同时通入惰性气体可以帮助带出反应生成的水。直到加入回流二甲苯后,才停止通入惰性气体。为保证隔绝空气效果,通入惰性气体前,反应釜先抽真空,以尽量排除空气,然后再通入惰性气体。
①气相温度的控制 在熔融反应的温度下,总有些易升华的原料会升华损耗,若升华量加大,气相温度会升得很快,显然,控制好气相温度是减少升华的必然措施,但气相温度与反应釜的釜内温度是有关联的,气相温度控制得越低,会导致釜内温度越无法升高,从而对反应造成影响。考虑到起始反应时,原料浓度高,升华倾向大,反应剧烈,开始生成的反应水从反应釜内脱出,也会对升华有帮助,因此起始反应时的气相温度应控制得低些。而随着反应进行,树脂分子逐渐形成,原料浓度逐渐降低,升华倾向逐渐减少,反应水也逐渐减少,此时,气相温度可控制得高些。如果将熔融反应气相温度的控制分为三段,建议按如下温度分别控制:99~102℃,102~105℃,105~108℃。
②釜内熔融反应温度的控制 工艺条件会设置一个熔融反应允许的最高温度,反应温度的过低会直接影响反应进程,温度过高会使反应速率过快,导致气相温度失控,这个温度要通过小试验证,平衡各方面因素,确认合适的熔融温度,一般将最高允许温度设置为比适宜的熔融反应温度高5℃,实际生产时,随着反应水脱出,釜内温度会逐渐上升,整个釜内温度的变化控制趋势与气相温度的控制趋势是同步的。
(3)回流(聚合)反应
回流反应是指在有回流溶剂(最常用的是二甲苯)存在的情况下,进行酯化反应与缩聚反应。熔融反应达到一定分子量后,加入回流溶剂,反应进入回流反应阶段。由于树脂合成的反应为可逆反应,若采用全部熔融反应的工艺,没有回流溶剂沸腾的帮助,反应生成的水从反应物中分离比较困难,对于反应的进程不利,会影响反应产物的品质,延长聚酯树脂达到规定要求的时间。
加入回流溶剂后,由于溶剂的沸腾,整个反应体系——反应釜、冷凝器、分水器等形成一个循环,反应生成的水通过回流溶剂的循环,从反应系统中分离出来,使可逆反应可以顺利地向正反应方向移动,有利于反应进程。由于溶剂的存在,反应物流动性好,容易成为均匀的液相,反应温度及聚酯树脂的黏度容易控制,反应进展顺利,树脂质量可以得到保证。
2.生产过程控制
饱和聚酯树脂的生产是由几个相对独立的单元操作所组成的,一般可分为以下几个单元操作。
①投料 是开始生产的第一步,这个步骤最重要的是投料准确,按工艺要求的顺序投料。同样的配方、不同的投料次序会对产品造成影响,多元醇和多元酸熔点各异、熔化快慢不同,最合适的次序是将容易熔化的多元醇分为两份,分别投在反应釜底部和上部,多元酸投在物料的中间,升温时多元醇与多元酸可尽快融合为均相,使反应顺利进行。
②中控 通过取样后的检验来衡量反应是否达到了规定的要求,这一过程要求取样后用来稀释的溶剂,与生产时稀释溶剂成分完全相同,以保证测试准确,样品溶解时,溶剂会挥发,溶解后应复称,减少的分量用稀释溶剂补足,可提高测试的准确性。
③稀释 反应达到终点后,放料到兑稀釜中稀释,另外,反应釜中应加入部分强溶剂洗锅,将黏附在反应釜内壁的树脂洗下,这一步骤的要求是搅拌均匀。
④过滤 原料引入与反应产生的杂质,都留在树脂体系中,但聚酯树脂加工的涂料都有细度要求,因此要用过滤的方法将树脂中的杂质滤掉,保证树脂产品清澈透明。
3.生产设备与使用工序
生产饱和聚酯树脂的主要设备有反应釜、稀释釜、过滤机,根据工艺特点,采用单釜间隙式生产工艺。以反应釜为主,配套有直冷凝器、横冷凝器、分水器、压滤机及稀释釜。加热方式与设备等,基本和醇酸树脂生产设备相同。
在聚酯树脂反应过程中,有需要加热的工序,也有需要冷却的工序,从工艺控制上说,要求加热与冷却的速度都要快,以减少过程时间,尽快达到工艺控制要求。根据工艺的要求,一般采用间接加热方式,配置高温导热油炉,采用适当的燃料,将导热油加热,依靠循环供热系统强制循环,达到加热反应釜内物料的目的。
反应釜可采用夹套通导热油、内置盘管通冷却水方式,也可采用夹套内进冷却水、内置盘管通导热油的方式。加热和冷却设置方式对加热和冷却效果有一定影响,在聚酯树脂生产过程中,需要冷却的工序有:反应结束后的终止反应;熔融反应向回流反应转换时的冷却,无论采用何种方式,都能满足工艺要求。
主要考虑的是工艺对加热的要求,生产开始时,要尽快将多元醇、多元酸熔化并形成均相,使反应顺利进行;采用夹套加热方式,热量通过反应釜壁传递给釜内的物料外围,再逐渐向内传递,而采用内置盘管方式加热,盘管处于物料中,热量传递较快,物料容易熔化。因此生产时采用内置盘管加热、外部夹套或半管冷却的方式更好。若生产一些后阶段黏度上升很快,需要及时冷却来终止反应的聚酯树脂,可考虑采用内置盘管冷却的方式。
不同聚酯树脂由于分子量、黏度等有较大差距,同样的搅拌很难适应不同的工艺状况,若有多个反应釜生产树脂,宜采用不同的搅拌形式,来适应不同的工艺要求。多元醇、多元酸熔化需要一个过程,为防止开始时过快的转速对搅拌造成损坏,搅拌电机应采用变频电机。常用的桨式搅拌器有单层式或双层式,一般采用倾斜安装,可产生一定轴向液流,搅拌效果较好,适应树脂黏度或分子量不是很大的品种。若合成高分子量、高黏度的线型聚酯,反应后阶段黏度很大,斜桨式搅拌器难以使釜内物料形成均相,产生中控黏度与兑稀后黏度的较大偏差,影响生产正常进行。
为解决高黏度聚酯树脂生产中出现的后阶段物料不均匀状况,采用结合旋桨式搅拌器和框式搅拌器特点的复合搅拌器是很好的方法。除由三片花瓣形桨叶组成的旋桨式搅拌器外,加上平置的有一定宽度的框组成,框外沿基本接近反应釜内的浸入式盘管,一般安装在反应釜筒身与下封头接口略下一些的水平面上,与常用的旋桨式搅拌器不同的是,桨叶采用将轴向液流向上扫的形式安装,比将轴向液流向下扫的安装形式效果要好。
目前在树脂生产企业,液体树脂过滤一般都采用垂直网板式过滤机(即前面介绍的阿玛过滤机),为保证过滤效果,避免一些机械杂质对不锈钢丝网造成影响,可在反应釜和过滤机之间安装袋式过滤的装置(内置不锈钢丝网),分离掉比较大的固体颗粒,以避免损坏过滤机。
考虑饱和聚酯树脂生产特点和工艺操作要求,聚酯树脂反应釜的直冷凝器,上半部设置成冷凝器,经过分水器的回流溶剂从冷凝器上进入,下半部设置为有一定数量填充料的分馏柱,上半部分流出的冷凝液,流到下半部分放置了填充料的分馏柱内,进行传质和传热,有利于共沸液的分离,加快酯化反应,减少热量消耗,减少升华引起的原料损失,避免因升华造成的冷凝器堵塞。
在直冷凝器与横冷凝器连接处,应安装监控温度计来显示气相温度、控制升华情况。考虑到有些树脂合成时,分馏柱中的填充料会造成沸腾困难,可在蒸出管的下部开手孔,必要时,可将填充料从手孔处取出。
冷凝器下的分水器,用于收集冷凝下来的反应水和回流溶剂共沸物,依靠各自密度不同进行分层,上层回流溶剂,经回流管重新进入反应釜,水则从分水器底部排出。一般分水器为立式圆筒状贮罐,顶部采用平顶或椭圆形封头,底部为锥形结构,分水器中部有两个对称圆形视镜,一个放置视镜灯,一个供观察使用,为方便观测,视镜中心部位与回流管低点等高,保持分水器液面高度处于圆形视镜的中间部位。
分水器进来的水和溶剂共沸物直接落在液面上,可能发生未充分沉淀,即走近路从回流管返回反应釜,回流溶剂中挟带过多的水,会对聚酯树脂的酯化反应造成不良影响,使反应有向逆反应方向进行的倾向。为使溶剂在分水器中有充足的时间沉降分层,且不直落在液面上,可通过一个漏斗将冷凝液引至液面下一定深度,延长了回流溶剂在分水器内停留时间,有利于水与溶剂分离。而分水器的容积以略大于反应釜内酯化反应所能产生的水量为宜。
饱和聚酯树脂生产所用设备基本和醇酸树脂生产设备相同。
(四)羟基型饱和聚酯树脂合成举例
饱和聚酯树脂用氨基树脂为固化剂,制备烘干涂料,用于卷材、家电、汽车的涂装;用聚氨酯树脂为固化剂制备常温固化涂料,用于汽车修补涂料、家具涂料等。但羟基型饱和聚酯树脂多已专业化生产,市场上不仅外企有许多商品化品种,国内企业聚酯树脂商品也不少。要根据用户要求选用合适的产品。为了解聚酯树脂的生产工艺过程,下面列举几个实例。
配方1:用氨基树脂交联固化、可用于快速固化的卷材及汽车面漆的聚酯树脂
配方(份): 新戊二醇 3800 间苯二甲酸 2400
己二酸 960 偏苯三酸酐 800
回流二甲苯 430 对苯二甲酸 480
单丁基氧化锡 5.0 乙二醇丁醚 780
100#溶剂 1300 150#溶剂 2400
指标: 固体分/% 58~62 加氏黏度(25℃)/s 15~20
色泽(Fe-Co) ≤1 酸值/(mg KOH/g) 2~5
操作步骤如下。
①将新戊二醇、间苯二甲酸、对苯二甲酸、偏苯三酸酐、己二酸投入反应釜,通氮气,升温。
②加热到能搅拌时,开动搅拌,投入单丁基氧化锡,打开直冷凝与横冷凝冷却水,反应出水后,停止通氮气。
③逐步升温,控制气相温度≤105℃,釜内温度最高≤235℃。
④当釜内温度达到230℃后,取样放在玻璃上,冷却到室温后,要达到透明,釜内树脂透明后维持30~45min。冷却到180℃以下,加入二甲苯。
⑤关闭直冷凝冷却水,边脱水边升温进行回流酯化反应,控制反应温度≤220℃。
⑥回流反应1h后,进行中控,检验黏度、酸值(注意反应后阶段黏度上升趋势)。
取样比例:12.7g样品+7.3g稀释溶剂
要求控制:加氏黏度(25℃)/s 15~20 酸值/(mg KOH/g)2~5⑦中控符合要求后,冷却到180℃以下,放料到稀释釜中(稀释釜中先加入部分兑稀溶剂);反应釜中加入剩余的兑稀溶剂,回流一段时间后放入稀释釜中,搅拌均匀后复测黏度,达到要求后过滤包装。
配方2:0T弯卷材面漆的聚酯配方实例
配方(份):新戊二醇 2080
三羟甲基丙烷 240
BEPD 630
己二酸 1320
单丁基氧化锡 5.0
回流二甲苯 250
乙二醇丁醚 780
150#溶剂 3200
1,6-己二醇 240
间苯二甲酸 2760
指标:固体分/% 58~62
加氏黏度(25℃)/s 25~35
色泽(Fe-Co) ≤1
酸值/(mg KOH/g) 2~6
操作步骤如下。
①将新戊二醇、间苯二甲酸、三羟甲基丙烷、1,6-己二醇、BEPD(乙基丁基丙二醇)投入反应釜,通氮气,升温。
②加热到能搅拌时,开动搅拌,投入单丁基氧化锡,打开直冷凝与横冷凝冷却水,反应出水后,停止通氮气。
③继续缓慢升温,气相温度按如下要求控制:第1小时,气相温度102~105℃;第2~3小时,气相温度108~112℃;第4小时,气相温度105~108℃。
釜内温度按如下要求控制:前1.5小时,釜内温度≤190℃;后2.5小时,釜内温度190~210℃。
④熔融酯化反应4h后,取样放在玻璃上,冷却到室温后,要达到透明,透明后维持30~45min。冷却到170℃以下,加入己二酸和二甲苯。
⑤关闭直冷凝冷却水,边脱水边升温,进行回流酯化反应,控制反应温度≤220℃。
⑥回流反应2h后,进行中控,检验黏度、酸值(注意反应后阶段黏度上升趋势)。
取样比例:12.7g样品+7.3g稀释溶剂
要求控制:加氏黏度(25℃)/s 25~35 酸值/(mg KOH/g) 2~6⑦中控达到规定要求后,冷却到180℃以下,放料到兑稀釜中(兑稀釜中先加入部分150#溶剂);反应釜中加入剩余150#溶剂,回流一段时间后,放入兑稀釜中,搅拌0.5~1.0h后,加入乙二醇丁醚,搅拌均匀后复测黏度,达到要求后过滤包装。
配方3:可用于慢速线卷材面漆的聚酯配方实例
配方(份):MPD 2880
季戊四醇 380
己二酸 760
苯酐 3150
回流二甲苯 380
乙二醇丁醚 1230
150#溶剂 3320
间苯二甲酸 975
单丁基氧化锡 5.0
指标:固体分/% 58~62
加氏黏度(25℃)/s 20~30
色泽(Fe-Co) ≤1
酸值/(mg KOH/g) 3~ 8
操作步骤如下。
①将MPD、季戊四醇、苯酐、间苯二甲酸、己二酸投入反应釜,通氮气,升温。
②加热到能搅拌时,开动搅拌,投入单丁基氧化锡,打开直冷凝与横冷凝冷却水,反应出水后,停止通氮气。
③继续缓慢升温,控制气相温度≤105℃,釜内温度最高≤200℃。
④熔融酯化反应3h后,取样放在玻璃上,冷却到室温后,要达到透明,透明后维持30~45min。冷却到180℃以下,加入二甲苯。
⑤关闭直冷凝冷却水,边升温边脱水,进行回流酯化反应,控制反应温度≤200℃。
⑥回流反应2h后,进行中控,检验黏度、酸值(注意反应后阶段黏度上升趋势)。
取样比例:12.7g样品+7.3g稀释溶剂
要求控制:加氏黏度(25℃)/s 20~30 酸值/(mg KOH/g) 3~8
⑦中控符合要求后,冷却到180℃以下,放料到兑稀釜中(兑稀釜中先加入部分兑稀溶剂);反应釜中加入剩余兑稀溶剂,回流一段时间后,放入兑稀釜中,搅拌均匀后复测黏度,达到要求后过滤包装。
配方4:用于聚氨酯树脂交联固化的聚酯树脂
配方(份):MPD 2890 苯酐 2500
单丁基氧化锡 6.0 回流二甲苯 500
间苯二甲酸 2300
环己酮 970 丁醇 120
100#溶剂 2920
指标:固体分/% 58~62 加氏黏度(25℃)/s 15~25
色泽(Fe-Co) ≤1 酸值/(mg KOH/g) 2~6
操作步骤如下。
①将MPD、间苯二甲酸、苯酐投入反应釜,通氮气,升温。
②加热到能搅拌时,开动搅拌,投入单丁基氧化锡,打开直冷凝与横冷凝冷却水,反应出水后,停止通氮气。
③继续缓慢升温,气相温度按如下要求控制:第1~3小时,气相温度95~98℃;第4~5小时,气相温度98~102℃;第6~7小时,气相温度102~105℃。
釜内温度要求≤220℃,一般熔融反应6~7h,可达到透明。
④熔融酯化反应5h后,取样放在玻璃上,冷却至室温后,要达到透明,透明后维持30~45min。冷却到180℃以下,加入二甲苯。
⑤关闭直冷凝冷却水,边升温边脱水,进行回流酯化反应,控制反应温度≤200℃。
⑥回流反应1h后,进行中控,检验黏度、酸值(注意反应后阶段黏度上升趋势)。
取样比例:13.0g样品+7.0g稀释溶剂
要求控制:加氏黏度(25℃)/s 15~25 酸值/(mg KOH/g) 2~6
⑦中控符合要求后,冷却到180℃以下,放料到稀释釜中(稀释釜中先加入部分稀释用溶剂);反应釜中加入剩余稀释溶剂,回流一段时间后,放入稀释釜中,搅拌均匀后复测黏度,达到要求后过滤包装。
三、羧基型饱和聚酯树脂
羧基型饱和聚酯树脂是粉末涂料主要的成膜物树脂之一。粉末涂料即为粉末状态的涂料,它的含义不仅在于粉末涂料的产品为粉末状态,即使在涂装过程中也是以粉末状态来使用的,只有在烘烤成膜时它才有一个熔融形成液态的过程。粉末涂料在理论上没有挥发分,成膜物为100%的涂料,可减少VOC对环境的污染,其发展受到重视。自它问世以来,发展很快,国内外有专著发表。
常用多元醇有新戊二醇(NPG)、乙二醇(EG)、一缩乙二醇(DEG)、三羟甲基丙烷(TMP)、1,4-丁二醇(BDG)、1,6-己二醇(HDO)、环己烷二甲醇(CHDM)等,多元羧酸有精对苯二甲酸(PTA)、精间苯二甲酸(IPA)、己二酸(ADA)、偏苯三甲酸酐(TMA)等。
粉末涂料用的端羧基饱和聚酯树脂是酸过量,一般是引入芳香族三元酸(如偏苯三酸酐)实现树脂分子中游离羧基(端羧基)过量。单体醇和羧酸的选择依据是配合固化剂、交联剂要求,线型支化或者刚性、柔性分子链,耐候性要求,以及经济成本、产品玻璃化温度等因素。配方设计、计算举例见表3-26。
表3-26 热固性粉末涂料用聚酯树脂配方

采用熔融法生产工艺,即本体聚合工艺。在反应器中加入新戊二醇、1,4-环己烷二甲醇、对苯二甲酸二甲酯和乙酸锌,开动搅拌混合,升温至150℃反应1h,除去由醇解反应所生成的甲醇,升温至210℃反应2h,加入三羟甲基丙烷、对苯二甲酸和二丁基氧化锡,仍在210℃下反应4h,温度升到240℃,高温脱水反应10h。然后降温至180℃,加入偏苯三甲酸酐,并在180℃下反应3h,即得聚酯树脂,其软化点为125℃,酸值为62mg KOH/g。
合成工艺是先部分醇解,因羟基大量超量,对苯二甲酸二甲酯中的羧基重新分配,甲醇被置换出并逸出体系外被除去;加入三羟甲基丙烷、对苯二甲酸和二丁基氧化锡后,产生酯化反应,生成端羟基较多的分子量较大的聚酯预聚物;加入偏苯三甲酸酐,首先是其分子中的酐基先开环(酯化)反应,可能还剩下两个羧基,根据最后树脂酸值的要求而设计的配方,使树脂较易达到较高酸值的要求,这是引入偏苯三甲酸酐的益处。原料中采用了对苯二甲酸二甲酯为原料,不是典型的端羧基饱和聚酯树脂配方,在这里只是用作说明问题的例子,其优点是可作为使用涤纶废丝为原料的技术路线的参考。较典型的端羧基饱和聚酯树脂的配方在一般涂料配方集或粉末涂料配方集中可以得到。
用精对苯二甲酸为主要羧酸时,合成工艺仍采用熔融直接酯化法,酯化温度可以高达250~255℃。酯化的催化剂选择有机锡类。不同催化剂的催化活性及催化酯化缩聚阶段不同。
缩聚时通氮气保护既可防止氧化,又可以带走副产物水。为使产品颜色浅,减少氧化反应,要加入不同温度阶段的抗氧剂。反应缩聚后期要抽真空,以帮助缩聚脱水。产品中一般还加入粉末涂料固化催化剂。
在粉末涂料中用的聚酯树脂有环氧/聚酯,混合型粉末涂料用的聚酯树脂和纯聚酯树脂粉末用的聚酯树脂有些区别,前者与所选用的环氧树脂规格有关,后者要与所用的固化剂如异氰尿酸三缩水甘油酯(TGIC)或β-羟烷基酰胺(HAA)相匹配,有关问题可参见第六章。