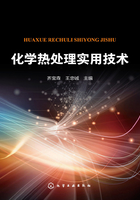
2.2 气体渗碳工艺及应用
2.2.1 气体渗碳工艺参数
气体渗碳工艺参数主要有渗碳温度、渗碳时间、炉气调节和冷却等,见表2.29。
表2.29 气体渗碳工艺参数的选择


2.2.2 气体渗碳法的分类、特点及渗碳剂的选择
2.2.2.1 气体渗碳法的分类及其特点
(1)滴注式气体渗碳 工作时把液体有机物(一般采用两种或两种以上有机液体,其中一种裂解产生的气体碳势较低,用作稀释气或称载气;另一种有机液体裂解产生的气体碳势较高,用作富化气,使炉内气氛的碳势提高至预定值)滴入渗碳炉中裂解,即可生成含有CH4、CO等供碳组分的气体,使用这些物质的气体渗碳方法称为滴注式气体渗碳。
调节这两种有机液体滴入量的比例,便可对气氛碳势进行控制。由有机液体分子中碳、氧的比值(C/O)可大致推断出其裂解气碳势的高低。甲醇(CH3OH)C/O=1,乙酸乙酯(CH3COOC2H5)C/O=2,丙酮(CH3COCH3)C/O=3。滴注式可控气体渗碳常用甲醇为稀释气的气源,用乙酸乙酯及丙酮作为富化气的气源。常把甲醇称为稀释剂,把乙酸乙酯和丙酮称为供碳剂。
进行滴注式可控气体渗碳时,稀释剂滴入量可保持恒定,通过调节供碳剂的滴量来控制气氛碳势。生产中常用露点仪及CO2红外仪测定气氛碳势,即根据气氛中脱碳组分H2O及CO2含量的变化分析气氛碳势的变化。为使气氛碳势易于调控,在供碳剂滴量变化时,气氛中CO及H2的含量基本不变。以甲醇为稀释剂、以乙酸乙酯或丙酮为供碳剂进行气体渗碳,能够满足上述要求。图2.16为滴注式井式气体渗碳炉及结构示意图。

图2.16 滴注式井式气体渗碳炉及结构示意图
1—滴量器;2—电机;3—炉盖;4—风扇;5—电热元件;6—炉膛;7—炉壳;8—保温层;9—装料筐;10—炉罐;11—支架;12—液压机构;13—限位开关;14—手动液压泵
(2)可控气氛气体渗碳 它包括吸热式气体渗碳、氮基气氛渗氮和直生式气体渗碳等。
①吸热式气体渗碳。它系由吸热式气体+富化气组成。常用吸热式气体有天然气、城市煤气、丙烷、丁烷等。富化气一般采用甲烷或丙烷。通过调整吸热式气体与富化气的比例即可控制气氛的碳势。它是以碳势较低的吸热式气体为载气,以丙烷等为富化气,在载气流量不变而富化气通向炉内的流量变化时,炉内气氛中的CO、H2含量基本不变,因而可用露点仪及CO2红外仪监测气氛碳势,进行可控渗碳。由于启动吸热式气体发生装置需要一段过程,故此法主要用于大批量生产。
②氮基气体渗碳。它系指以氮气为载体,添加富化气或其他供碳剂(如甲醇裂解气)的气体渗碳方法。该法具有能耗低、安全、无毒等优点。由于氮基气氛易得,在可控气氛渗碳中的应用相当普遍。
③直生式气体渗碳(即超级渗碳)。它是将燃料(或液体渗碳剂)与空气或CO2气体直接通入渗碳炉内形成渗碳气氛的一种渗碳工艺。随着计算机控制技术应用的不断发展,直生式渗碳的可控性也不断提高,应用正逐步扩大,图2.17为直生式渗碳系统简图。

图2.17 直生式渗碳系统简图
直生式气体渗碳的特点:
ⅰ.由富化气(天然气、丙烷、丁烷、异丙醇、煤油、丙酮、乙醇等)+氧化性气体(空气或CO2)组成。
ⅱ.气氛碳势可控,这得益于气氛监控装置和计算机控制技术在热处理领域的飞速发展。直生式渗碳气氛是非平衡气氛,CO含量不稳定,故应同时测量O2和CO含量,再计算出炉内碳势。调节富化气与氧化性气体的比例可调整炉气碳势。通常固定富化气流量,调整空气或CO2的流量(即当炉内的碳势高于设定值时,将增加空气的加入量;反之,当炉内的碳势低于设定值时,将减少空气的加入量)。
ⅲ.碳传递系数(表征碳从气相向工件表面转移速度的量,表示渗碳速度的快慢)较高。
ⅳ.设备投资小。
ⅴ.碳势调整速度快于吸热式和氮基渗碳气氛。
ⅵ.渗碳层均匀,重现性好。
ⅶ.对原料气的要求较低,气体消耗量低于吸热式气氛渗碳。
2.2.2.2 气体渗碳所使用的渗碳剂及选择(见表2.30)
气体渗碳所使用的渗碳剂及选择见表2.30,常用有机液体的渗碳特性见表2.31。
表2.30 气体渗碳使用的渗碳剂类型及其选择

表2.31 常用有机液体的渗碳特性

2.2.3 井式炉气体渗碳
2.2.3.1 渗碳工艺特点
目前在实际生产中,广泛采用的是在RJJ型井式渗碳炉(图2.16)中滴入渗碳介质进行气体渗碳。渗碳介质多为煤油或煤油加甲醇等,整个渗碳过程一般可分为排气、强渗、扩散和降温四个阶段。
(1)排气阶段 此阶段目的是尽快排净炉内的氧化性气氛(空气等)和使炉温重新升到渗碳温度,提高炉气的碳势,为渗碳做准备。在渗碳温度下将工件放入炉内时,不可避免会有大量空气进入炉罐,空气中O2与炉气中H2、CO、甲烷及炭黑反应,分别生成水及CO2等氧化性气体,会使工件表面产生氧化,形成的氧化膜阻碍渗碳过程的进行,使渗碳不均匀,影响工件的渗碳质量。工件吸热,炉温迅速下降,一般会降到800~850℃左右,而煤油在此温度下裂解不充分,若渗碳剂滴入量太大,会产生大量炭黑,因此该阶段采用较低的煤油滴量,炉温>850℃时,煤油的分解速度加快,应加大滴量,迅速排净炉内氧化性气体。到工艺温度后的前30~60min,仍为排气阶段,目的是提高炉内温度的均匀性和使工件内外温度趋于一致。排气结束的标准:有的以炉气中CO2含量小于0.5%作为排气结束的标准,也有的以炉气中CO与H2O的相对平衡量作为炉气恢复阶段的结束,表2.32列出了CO与H2O的相对平衡量,排气结束后炉内CO2、O2的含量应小于0.5%,以保证渗碳过程的正常进行。多采用以下方法进行排气:甲醇与煤油排气;保护性气体加煤油排气;只用煤油进行排气。排气方式不同,其结果有很大的差别,以甲醇与煤油排气效果最佳。
表2.32 不同温度下CO与H2O的相对平衡量

(2)强渗阶段 排气结束后进入强渗阶段。此阶段是吸收过程,需使炉内气氛保持较高碳势,使零件表面迅速达到较高碳浓度和浓度梯度,为加快扩散创造条件。故强渗阶段采用较大的煤油滴量。强渗时间主要取决于对渗碳层深度的要求,渗碳时间太长或滴油量过大,会使工件表面的碳含量过高,造成表层K聚集,相反则使渗碳速度减慢,无K的形成。炉气成分可参考表2.33,当试样渗层深度达到要求渗层深度的2/3左右时,应转入扩散阶段。
表2.33 渗碳炉保温后渗碳时炉气成分

注:880℃渗碳时,CO2的浓度为0.45%~0.52%;930℃渗碳时,CO2的浓度为0.11%~0.15%。
(3)扩散阶段 工件经长时间渗碳后,表面层内的碳浓度较高,此阶段是为降低表面碳含量,要求炉气的碳势较低,工件表面的碳向内部扩散,故应采用减少渗剂滴量的方法,一般煤油滴入量为强渗阶段的1/3~1/2。要获得理想的表面碳浓度和渗层深度,扩散时间与强渗时间基本一致。在实际渗碳过程中,通常将强渗阶段与扩散阶段合称为渗碳阶段或保温阶段,是渗碳层形成的关键环节,因此控制好渗剂的流量和渗碳时间至关重要,及时用试样来检查渗层质量是常用的控制质量的方法,当达到技术要求时即可降温,保温。
(4)降温与出炉阶段 渗碳工艺中规定的时间因受到渗剂成分波动等各方面因素的影响,会有所调整,因此应在渗碳结束前约1h抽检试棒,渗层符合技术要求后方可出炉,降温时渗剂滴入量与扩散阶段相同。对于直接淬火的渗碳件,随炉降温到淬火温度,并保温一段时间使工件内外温度一致后再淬火;对于需重新加热淬火的工件,为减少表面氧化、脱碳及变形,也应降至860~880℃,出炉放入有保护气氛的冷却炉或坑中,冷到一定温度后再重新加热淬火。表2.34列出了煤油加甲醇的分段渗碳时的用量情况。该工艺可实现可控气氛渗碳,获得高质量的渗碳层,具有表面光洁,渗碳速度快等优点。
表2.34 采用煤油为渗碳剂、甲醇为稀释剂的滴注式气体分段渗碳时的用量

为保证渗碳效果,可采用以下途径:ⅰ.用一种渗碳剂时,多采用在渗碳过程中改变渗碳剂滴量的方法来调整炉内的碳势;ⅱ.选择合适有机溶剂,混合成高效的渗剂,改变渗剂滴量,使碳势控制在要求范围内;ⅲ.同时滴入两种有机液体,一种是热分解后形成相当于稀释气氛的气体,另一种则热分解后形成强渗气氛(富化气)。前者多用甲醇,后者多用乙酸、丙酮、异丙醇等。典型的渗碳工艺见图2.18和图2.19。

图2.18 井式炉气体渗碳的典型工艺(RJJ-75-9T)

图2.19 煤油-甲醇滴注式通用气体渗碳工艺
注:q—按渗碳炉功率计算的渗剂滴速,q=f1P[f1为单位功率所需滴速,f1可取0.13mL/(min·kW);P为渗碳炉功率,kW]。Q—按工件有效吸碳表面积计算的渗碳剂滴速,Q=f2NS[f2为单位吸碳表面所需滴速,取f2=1mL/(min·m2);N为装炉工件数;S为每个工件的有效吸碳表面积,m2]
操作时工件宜到温入炉。炉温在880℃以下时,用甲醇排气,迅速排除氧化性气体;炉温高于880℃后滴入煤油,迅速提高炉内碳势,既可防止炭黑出现,又加速了渗碳过程。不同渗碳温度下的强渗时间t可根据所要求的渗层深度确定,见表2.35。图2.18所给出的扩散时间是指渗碳时的高温扩散时间,如采用降温淬火,则扩散时间应在此基础上加上降温时间及0.5h的保温时间。
表2.35 强渗时间、扩散时间与渗碳层深度的对应关系

生产实际中通常采用固定碳势法和分段控制法控制碳势,见表2.36。
表2.36 生产实际中两种控制碳势的方法及其特点

2.2.3.2 渗碳的操作规程
在渗碳过程中,需要做好如下工作。
(1)渗碳前的准备工作 检查设备的技术状况、零件试样的准备情况等(见表2.37)。
表2.37 渗碳前的准备工作

表2.38 几种常见防渗涂料

(2)渗碳工艺要求及注意事项 见表2.39。
表2.39 渗碳工艺要求及注意事项

表2.40 井式气体渗碳炉煤油滴量参考表

注:更换滴油器需测定“滴”的大小,一般为100滴=3.8~4.2mL。
用井式炉进行渗碳时,除用煤油作渗碳介质外,还可采用天然气、城市煤气或液化石油气等气态渗碳介质。
表2.41为20CrMnTi钢在RJJ-75-9T炉中的渗碳结果,可以看出提高渗碳温度能明显增加渗碳层深度,大大缩短了渗碳时间,但渗碳温度高于950℃以上会造成晶粒粗大,降低渗碳件的力学性能,一般不被采用。对于20CrMnTi钢在920~930℃进行的渗碳处理,利用回归方程式可知渗碳层深度(mm)与渗碳时间的关系为:
δ=0.4697+0.243t。
式中,t=3~10h,此公式可作为编制20Cr钢渗碳工艺的参考依据。
表2.41 渗碳层深度与渗碳温度的关系

强渗时间、扩散时间与渗碳层深度的关系,见表2.35。
(3)两种渗碳新工艺 为了提高渗碳质量和缩短渗碳周期,在分段控制法的基础上又发展了几种渗碳工艺。这里介绍其中两种较有成效的工艺,见表2.42。
表2.42 两种渗碳新工艺简介


图2.20 甲醇+煤油作渗剂的分段渗碳工艺
(RJJ-75-9T,每100滴煤油为4mL,渗层深度0.8~1.2mm)
(4)滴注式可控气氛渗碳 前述井式炉滴注式气体渗碳工艺中,碳势不能按需调节,质量不稳定。滴注式可控气氛渗碳的主要特点是把两种有机液体直接滴入渗碳炉内进行热分解,使其中一种滴液形成稀释气(载气),在渗碳初期用来排气,在渗碳阶段维持炉内正压,并构成恒定的炉气成分;另一种滴液形成富化气(渗碳气),起渗碳作用。根据炉内气氛反馈的信息,自动地调节两种液体滴入的比例,即可控制炉内碳势。通常选用甲醇产生稀释气,丙酮、乙酸乙酯、异丙醇、丙烷、煤油等有机液体产生富化气。应用滴注式可控气氛渗碳,可提高渗碳质量,加快渗碳速度。
几种常用渗碳介质在900℃经裂解后,碳势为1%的气体成分如表2.43所示。滴注式可控气氛渗碳的工艺过程、碳势控制等见表2.44。
表2.43 几种常用渗碳介质的裂解气成分

表2.44 滴注式可控气氛渗碳工艺过程及碳势控制


图2.21 红外仪碳势自动控制系统示意图
1—电磁阀;2—手动调节阀;3—红外线CO2分析器;4—流量计;5—标准气瓶;6—取样泵;7—过滤器;8—冷却器;9—井式渗碳炉

图2.22 碳势-CO2浓度的关系曲线(20CrMnTi)

图2.23 滴注式可控气氛渗碳工艺曲线(RJJ-60-9T)
(5)渗碳设备—井式气体渗碳炉 见图2.16。井式气体渗碳炉密封性较好,热损失小,所以应用广泛。其结构与低温井式电阻炉相近,一般用电阻丝分层环绕在四周炉壁上,并分段控制,炉门上设有使炉气循环的风扇。不同之处是井式气体渗碳炉中设置有耐热钢炉罐,并用炉罐密封,将电热元件与炉内气氛隔开。工作时,渗碳剂(如煤油)从炉盖上的滴量器滴入炉中,热裂解后经风扇搅动循环,均匀接触工件,废气从炉盖上的废气孔排出。为提高渗碳效果和改善渗碳质量,对传统井式电阻炉做了改进,见表2.45。
表2.45 对传统井式电阻炉的改进

2.2.4 密封箱式炉气体渗碳
它可采用吸热式气体渗碳、氮基气氛气体渗碳或直生式气体渗碳。
2.2.4.1 吸热式气体渗碳
吸热式气氛是将可燃性原料气,如丙烷、丁烷、天然气等烃类与较少的空气混合后,通入装有催化剂的炉膛中,在催化剂的作用下,并借助外加热,使混合气在950~1150℃的条件下进行反应,用这种方法制备的气氛称为吸热式气氛。其渗碳气氛、渗碳反应、碳势测量和控制及工艺实例见表2.46。
表2.46 吸热式气体渗碳气氛、渗碳反应、碳势测量和控制及工艺实例

表2.47 常用吸热式气体成分


图2.24 由甲烷制成的吸热式气氛中碳势与CO2含量之间的关系

图2.25 由丙烷制成的吸热式气氛中碳势与CO2含量之间的关系

图2.26 由甲烷制成的吸热式气氛中碳势与露点之间的关系

图2.27 由丙烷制成的吸热式气氛中碳势与露点之间的关系

图2.28 由甲烷制成的吸热式气氛中碳势与氧探头输出电势之间的关系

图2.29 由丙烷制成的吸热式气氛中碳势与氧探头输出电势之间的关系

图2.30 连续作业吸热式气体渗碳设备及工艺示意图
2.2.4.2 氮基气氛气体渗碳
系指以氮气为载体,添加富化气或其他供碳剂的气体渗碳方法,其特点为优质、安全、无毒和能耗低等。
(1)氮基渗碳气体的组成 几种典型氮基渗碳气氛的成分组成见表2.48。表中所列的氮基渗碳气氛中,CH3OH+N2+富化气最具代表性,其中40%N2+60%CH3OH的渗碳效果最佳,甲烷或丙烷作富化气多用于连续式或多用炉,丙酮或乙酸乙酯作富化气多用于周期式渗碳炉。
表2.48 几种典型氮基气氛气体渗碳成分组成

(2)氮基气氛渗碳的特点 见表2.49。
表2.49 氮基气氛渗碳的特点

表2.50 氮基气氛、吸热式气氛和滴注式气氛渗碳速度比较

注:8620钢(相当于我国的20CrNiMo钢)所测数据。
(3)氮基气氛渗碳工艺实例 见表2.51。
表2.51 氮基气氛渗碳工艺实例分析


图2.31 阀体、阀座氮基气氛渗碳工艺参数
N2流量单位为m3/h,A(甲醇)、B(烃类)流量单位为L/min
2.2.4.3 直生式气体渗碳(超级渗碳)
直生式气体渗碳又称超级渗碳,是将燃料与空气或CO2气体直接通入渗碳炉内形成渗碳气氛进行渗碳的一种工艺,随着计算机控制技术应用的不断成熟和完善,直生式渗碳的可控性也不断提高,应用正逐步扩大。图2.17为直生式渗碳系统简图。直生式气体渗碳的气氛、特点、碳势及控制见表2.52。
表2.52 直生式气体渗碳的气氛、特点、碳势及控制


图2.32 850℃和950℃下不同的直生式气氛
表2.53 不同气氛中的碳传递系数(β)的比较

注:渗碳温度为950℃,碳势为1.15%。
2.2.4.4 渗碳工艺操作规范
渗碳工艺操作规范见表2.54。
表2.54 渗碳工艺操作规范

表2.55 渗碳处理前的准备工序

2.2.4.5 多用炉渗碳的操作规程
在渗碳过程中,需要做好如下工作。
(1)渗碳前的准备工作 检查设备的技术状况、零件试样的准备情况等,详见表2.56。
表2.56 多用炉渗碳前的准备工作

(2)技术要求 见表2.57。
表2.57 多用炉渗碳技术要求

(3)多用炉操作规程 渗碳过程分为四个阶段,即排气、强渗、扩散及降温或直接出炉等。以TQF-17-ERM易普森多用炉直生式气体渗碳为例说明其操作时应注意的问题(见表2.58)。
表2.58 TQF-17-ERM易普森多用炉操作规程


(4)安全生产 操作人员在生产前要穿戴好工作服,其注意事项见表2.59。
表2.59 操作人员安全生产注意事项

2.2.5 连续气体渗碳炉
连续气体渗碳炉有推杆式连续气体渗碳炉(见图2.33)和网带式连续气体渗碳炉(见图2.34),不管是连续气体渗碳炉还是周期式气体渗碳炉,其渗碳的原理都是一样的。连续气体渗碳炉的最大特点就是能够将工件在一定时间内连续进行处理,除去一年的几次烧炭和几次维修时间外,通常都是24h的连续操作。因此生产效率高,适用于大批量生产的零件。

图2.33 推杆式连续气体渗碳炉示意图
1—推料机;2—炉门;3—炉门升降机构;4—热电偶;5—炉料;6—电热元件;7—悬挂叉

图2.34 网带式连续气体渗碳炉生产线示意图
1—上料机;2—清洗机;3—网带式淬火炉;4—淬火槽;5—中间清洗机;6—网带式回火炉;7—发黑槽
连续气体渗碳炉热处理工艺操作要点见表2.60。
表2.60 连续气体渗碳炉热处理工艺操作要点

零件入炉前的清理和设备、仪器、仪表、电气、电热元件、管路液压传动、机械传动、气动、润滑、密封的检查和井式气体渗碳炉相同。
2.2.6 真空渗碳(低压渗碳)工艺及应用
在低于1×105Pa的条件下于渗碳气氛中进行的渗碳,称为真空渗碳。它是近年来发展起来的一种气体渗碳工艺。图2.35为卧式双室真空渗碳炉简图。真空渗碳对提高产品质量和节约能源有显著效益,是一种极具发展前景的化学热处理新工艺。

图2.35 渗碳及淬火两用卧式双室真空渗碳炉结构简图
1—炉壳;2—加热室;3—拖车;4—淬火油槽;5—手推车;6—气冷室;7—电风扇
2.2.6.1 真空渗碳的特点
与普通气体渗碳相比,它具有如下特点。
①可在较高温度(980~1100℃)下进行,常用1030~1050℃。真空对工件表面有净化作用,有利于其吸附碳原子,因而能显著缩短渗碳周期,仅约为一般气体渗碳所需时间的1/3。真空渗碳温度及适用范围见表2.61。
表2.61 真空渗碳温度及适用范围

②工件在真空条件下渗碳,渗碳层均匀,表面不脱碳,不产生晶界氧化,有利于提高零件的疲劳强度。
③可直接将甲烷、丙烷或天然气通入真空炉内渗碳,无需添置气体制备设备。
④对于有不通孔、深孔、狭缝的零件,或不锈钢、含硅钢等普通气体渗碳效果不好甚至难以渗碳的零件,真空渗碳都可以获得良好的渗碳层。
⑤真空渗碳的耗气量(CO2排放量少)仅为普通渗碳的几分之一或十几分之一。劳动条件好、无公害,对环境基本上无污染;可间歇处理并可达到节能的目的。
⑥气氛管理比普通气体渗碳容易,如能确定渗碳时间和扩散时间,基本上即可获得所需要的质量。
⑦缺点是容易产生炭黑,设备投资大、成本高。
真空渗碳与普通气体渗碳工艺参数的比较见图2.36。

图2.36 真空渗碳与普通气体渗碳工艺参数的比较
2.2.6.2 真空渗碳工艺及操作
(1)工艺特点 见表2.62。
表2.62 真空渗碳工艺特点


图2.37 真空渗碳炉内温度与压力的关系

图2.38 碳势与甲烷含量、炉气压力之间的关系

图2.39 脉冲式真空渗碳工艺示意图

图2.40 真空渗碳淬火工艺曲线示意图
(2)操作程序及要求 详见表2.63。
表2.63 真空渗碳操作程序及要求

(3)注意事项
①清楚真空渗碳的应用目的。确定真空渗碳工艺的目的是通过高温下短时间处理来提高生产率,实施细孔内的表面渗碳,减轻表面氧化,利于环保等,根据目的加以有效应用。
②确立处理条件。目前,真空渗碳工艺像气体渗碳那样,根据热力学的平衡反应来控制炉内气氛是很困难的,故应考虑使用设备、渗碳用气体、处理零件等,以确立最佳的处理条件。
③根据零件形状(特别是拐角部、棱边部),应注意渗碳质量密度增高,容易产生渗碳体的情况。
④如果处理温度为高温(约950℃以上),有时会发生晶粒粗化,需要进行细化处理。
⑤关于设备,除了以往的分批式处理炉外,连续式、模块式等新型多品种、大批量生产用设备已经开发出来,不过,必须选择适合于处理零件的设备。真空渗碳炉可选用石墨或陶瓷材料制造。石墨炉允许更高的渗碳温度,而陶瓷结构则不需像石墨炉那样,要加强炉子的隔热保护措施。
2.2.7 深层渗碳工艺及应用
渗层渗碳系指工件渗碳淬火后,表面总硬化层深度达3mm以上的渗碳。其工艺处理多用于大型低速重载工件,往往需要渗碳层深度>3mm,有的甚至达8mm。深层渗碳工艺可显著提高工件表面承载能力。其设备多采用大型井式气体渗碳炉。
渗碳层要求一定时,提高渗碳温度可缩短渗碳时间。但是高温渗碳对深层渗碳并不适宜,因为长时高温渗碳,晶粒粗化,变形加大,甚至在淬火时有引起开裂的危险。尤其是含Mn钢,高温渗碳后产生裂纹的倾向明显加大。Cr在短期渗碳时能阻碍奥氏体晶粒长大,但在长时渗碳时,也会引起晶粒长大。表2.64为20CrNi2Mo钢在不同温度渗碳时晶粒长大的倾向。另外,渗碳温度的提高将缩短设备的使用寿命。
表2.64 渗碳温度对晶粒度(级别)的影响

2.2.7.1 深层渗碳操作规程
深层渗碳操作规程见表2.65。
表2.65 深层渗碳的操作规程

2.2.7.2 深层渗碳对热处理设备的要求
因深层渗碳在高温状态下和高碳势气氛中时间较长,因此在热处理过程中,对设备也提出更高要求。以氮-甲醇气氛在深层渗碳中的应用为例说明深层渗碳在温度的控制方式、碳势的控制方式等方面对热处理设备的具体要求(见表2.66)。
表2.66 深层渗碳对热处理设备的要求

表2.67 某公司采用不同控温方式的两台同类型设备的调试数据

2.2.7.3 深层渗碳工艺控制要点及应用
表2.68是深层渗碳工艺参数控制要点,图2.41为滴注式深层渗碳工艺曲线。
表2.68 深层渗碳工艺参数控制要点

注:参照图2.41。

图2.41 滴注式深层渗碳工艺曲线
2.2.8 高温渗碳工艺
渗碳是一种限制性的碳扩散工艺,即渗碳件要达到预期要求的渗层深度所需的时间,完全取决于碳渗入工件的扩散速率,碳扩散率是热力学温度的函数,呈指数变化,因此提高渗碳温度就能获得较高的生产率。渗碳温度从900℃提高到955℃,渗碳时间可缩短一半;从955℃提高到1010℃,渗碳时间可再缩短一半。然而理论分析认为,过高的渗碳温度可能带来一些不良后果,如会降低渗碳炉的使用寿命,渗碳件会因晶粒长大而降低其力学性能等。
因此,高温渗碳系指在950℃以上的渗碳。高温渗碳工艺及设备的特点、性能变化见表2.69。
表2.69 高温渗碳工艺及设备的特点、性能变化

表2.70 高温渗碳和普通渗碳后工件的性能对比

注:1.分子为普通渗碳温度920℃,15h;分母为高温渗碳温度1000℃,8h。
2.钢经渗碳后空冷,再850℃加热,一次淬火加低温回火。
2.2.9 化学催渗渗碳工艺
2.2.9.1 稀土催渗渗碳工艺
工件的稀土渗碳工艺是我国独具特色的一种渗碳工艺,其明显特点是具有催渗效果及细化碳化物的作用,这一工艺在齿轮生产中取得了良好效果。表2.71是稀土渗碳时的炉气成分,可看出由于稀土的加入,炉气中的烃类减少,CO增加,从而使气氛活化。图2.42是稀土对20CrMnTi钢气体渗碳渗层深度的影响,可以看出,稀土元素的催渗作用除可使渗速加快、缩短渗碳时间、节约电能外,还可将渗碳温度由常规930℃降至860℃左右,这对获得细晶组织、减小变形是有利的。
表2.71 稀土渗碳时的炉气成分(体积分数) 单位:%


图2.42 稀土对20CrMnTi钢气体渗碳渗层深度的影响
1—无稀土;2—加稀土
定碳及金相分析表明,低温(860~880℃)稀土渗碳后,表面碳含量(质量分数)即使高达1.5%,其渗层碳化物、残留奥氏体及马氏体组织均良好,而且试验表明所处理工件具有优异的综合力学性能。由于渗碳温度降低,工件的变形减小。
2.2.9.2 BH催渗渗碳工艺
快速BH催渗渗碳工艺以提高渗碳速度为主要目的。表2.72和表2.73给出了汽车后桥从动弧齿锥齿轮的普通渗碳和BH催渗工艺对比。表2.74给出了两种工艺处理后渗层深度、显微组织和硬度检验结果对比。
表2.72 从动弧齿锥齿轮普通渗碳工艺表①

①装载方法:齿面朝上平放。每盘两摞,每摞6件,每盘12件。下同。
表2.73 从动弧齿锥齿轮快速BH催渗工艺表

表2.74 两种渗碳工艺处理后渗层深度、显微组织和硬度检验结果

降温BH催渗渗碳工艺以减小齿轮畸变为主要目的。图2.43和图2.44给出了降温催渗和普通渗碳工艺对比,表2.75为其畸变测量结果对比。

图2.43 从动弧齿锥齿轮普通渗碳工艺图

图2.44 从动弧齿锥齿轮降温BH催渗工艺图
表2.75 普通渗碳工艺和降温BH催渗工艺渗碳淬火后从动弧齿锥齿轮的畸变情况

2.2.10 气体渗碳应用及实例分析
2.2.10.1 井式炉气体渗碳工艺实例
井式炉气体渗碳工艺实例见表2.76。
表2.76 井式炉气体渗碳工艺实例


2.2.10.2 汽车、拖拉机齿轮的微机控制井式炉滴注式气体渗碳实例
汽车、拖拉机齿轮的微机控制井式炉滴注式气体渗碳实例见表2.77。
表2.77 汽车、拖拉机齿轮的微机控制井式炉滴注式气体渗碳实例


图2.45 20CrMnTi齿轮微机控制气体渗碳工艺曲线
2.2.10.3 [实例2.1]20CrMo曲柄件的多用炉浅层渗碳表面强化实例
(1)零件名称及使用材料 某型号曲轴总成由左右曲柄、连杆和曲柄销等几种零件组成,见图2.46。可以看出,曲柄件等渗碳后进行磨削加工,磨削后的硬度需在要求的范围内。左右曲柄、连杆和曲柄销经压合后,有一定的扭矩要求,因此曲柄、曲柄销之间有一定的过盈量。连杆、曲柄销要求耐磨;曲柄不仅要求耐磨,还要求强度与韧性之间合适的配合。曲柄压合后,曲柄销受的是压应力,如果曲柄受的是拉应力,曲柄的强度与韧性配合将不好,曲柄容易开裂。曲柄件所使用材料为20CrMo钢。

图2.46 曲轴总成(左右曲柄、连杆和曲柄销)图
(2)技术要求 20CrMo钢热处理工艺为渗碳淬火。由于工件较小,要求的硬化层浅,成品要求0.6~0.9mm(514HV),表面硬度要求56~64HRC;热处理工序要求为0.8~1.0mm(514HV),表面硬度要求57~64HRC。可以看出,曲柄件的渗层均属于浅层渗碳。
(3)热处理工艺分析 根据以上曲柄件工作条件分析,要保证曲柄热处理项目合格,需解决以下几个问题:
ⅰ.设备能否保证一炉工件的硬化层都在要求的范围内。
ⅱ.热处理后的工件能否有一个合理的碳浓度梯度(硬化层硬度梯度),以保证磨后表面硬度。
ⅲ.曲柄压合后,其扭矩能否合格,与曲柄孔的表面硬度、心部硬度和硬化层深度有关。
这种曲轴总成中曲柄渗碳的主要目的为:
ⅰ.提高表层的强度,保证扭矩合格。
ⅱ.表面渗碳硬化后,提高疲劳强度。
ⅲ.表面有一个合理的硬度,以便于同其他零件的装配。
ⅳ.曲柄较小,有强度、韧性要求,对硬化层、碳浓度梯度(硬化层硬度梯度)、心部硬度、表面硬度和残余奥氏体等要求高。
(4)渗碳工艺分析 硬化层(渗碳层)、碳浓度梯度(硬化层硬度梯度)、心部硬度、残余奥氏体对于力学性能的影响如下。
①硬化层深度(渗碳层)。渗碳层深度主要受渗碳温度、渗碳时间和碳势等因素的影响。渗碳层深度的计算可以从F.E.Harris的公式中计算出:
式中,i为时间;T为热力学温度,K。当渗碳温度为900℃、930℃时,相应的A(T)值为0.540、0.647。
由公式可看出,碳在γ-Fe中的扩散系数随着温度的升高而急剧增加;当温度一定时,渗层深度与渗碳时间呈抛物线的关系,可见温度和时间对渗层深度起主要影响。在时间、气氛相同条件下,提高渗碳温度,可大大加快渗碳速度,使得表面碳浓度高,浓度梯度平缓降低渗碳温度效果则相反,因此提高渗碳温度对加速渗碳有利。
对于浅层渗碳,对时间的控制要求很高。浅层渗碳温度不宜太高,若温度太高,渗碳时间不宜控制,会影响渗层的深度;同时温度太高心部组织易于粗化,增加心部的淬透性,使心部硬度超差。浅层渗碳要求渗层浅,整个渗碳过程处在高速扩散期,在较短的时间内就会获得要求的层深。温度波动对渗碳层的影响也很大。对于浅层渗碳,更应提高渗碳温度的控制精度。温度高、扩散快,在浅层渗碳中处理的时间短,层深不易控制,极易产生偏差;温度降低后,碳的扩散速度减慢,增大了过程控制的余地,便于操作处理,降低了出现层深超差的概率。
渗碳层深度增加,其疲劳寿命会显著提高,随着渗碳层深度的增加,可以增加扭矩,但冲击韧度严重下降。渗层的紧束力增加,使心部材料塑性变形的可能性受到严重限制;渗层增加,相应的扩散层加深,造成心部碳含量升高,淬火后的心部硬度升高,强度增加,韧性减少,造成曲柄在压合后形成延迟裂纹。
②碳浓度梯度(硬化层硬度梯度)。硬化层硬度梯度与渗碳层碳浓度梯度有关。渗碳层碳浓度梯度与渗碳时的碳势和渗碳时间有关。对于浅层渗碳主要是提高零件表面的渗碳反应速度,由于渗层深度浅,碳原子活度大,扩散速度快,即使在前期高碳势气氛下,渗碳层也较难形成网状碳化物。渗碳层深度受碳势影响大,表层成分波动随气氛波动较灵敏。根据碳在奥氏体中的溶解度w(C)%=0.003T-1.47(850℃≤T≤950℃),计算得900℃碳的溶解度是1.23%;930℃碳的溶解度是1.32%。
控制炉气的碳势是为了零件表面达到最佳碳含量,对于低合金渗碳钢,表面要求wC=0.75%~1.00%,渗碳过程中可采用一段碳势(恒碳势),也可采用两段碳势(变碳势)的渗碳工艺。采用两段渗碳时,可以缩短工艺时间,提高渗层质量,但在实际渗碳过程中,气氛碳势与工件表面碳浓度存在一定差值。在薄层渗碳条件下,由于渗碳时间短,气氛碳势与工件表面碳浓度远未平衡,两者的差异相当大。因此对于这种热处理后需要进行磨削加工的零件,会造成表面硬度的不合格。
曲柄热处理后需要磨削,渗碳层中的碳浓度过高时,碳化物呈网状,造成表面脆化,力学性能降低。渗碳层中的碳浓度高,淬火后表面的残余奥氏体量多,在磨削的过程中,磨削热使残余奥氏体易转变为马氏体,形成磨削裂纹。表面硬度在能达到要求的前提下,采用高的回火温度,甚至回火两次,可减少残余奥氏体量和应力,以有利于磨削。表面碳含量高,淬火后形成孪晶马氏体,强度高,脆性大,韧性小,造成曲柄在压合后形成延迟裂纹。因此浅层渗碳应采用合适的碳势。
③心部硬度。渗碳钢的心部硬度对渗碳零件的力学性能有很大影响。大量的试验和使用证明,一些心部硬度过高的小件在使用的过程中易造成脆断;而且心部硬度过高,疲劳强度下降,韧性也不足,因此对于小件应加强对心部硬度的检测。优化钢材的使用(在保证心部硬度的前提下,采用碳含量低的材料),采用渗后空冷(细化心部组织)再加热淬火,能在很大程度上降低心部硬度。
④残余奥氏体。研究表明,表面适当的残余奥氏体不会恶化渗碳零件的抗疲劳性能,甚至有必要保留适当比例的残余奥氏体。残余奥氏体的量如果适当,可以抑制淬火显微裂纹的产生。曲柄与曲柄销在压合的过程中,其残余奥氏体在剪应力的作用下,会引起硬化、马氏体转变及渗碳体的析出,从而吸收一部分能量,防止曲柄由于应力过大而产生裂纹,而不发生转变的残余奥氏体可起到缓和裂纹尖端引起应力集中的作用。残余奥氏体本身较软,可承受拉伸应力产生的流变,有利于消除显微裂纹。浅层渗碳由于渗碳时间短,零件表面的清洁非常重要。表面的杂质对于浅层渗碳的影响比深层渗碳更大,会造成渗层不均,淬火后的表面硬度不足,因此渗碳前的清洁非常重要。既可进行预处理,预热工件,也可清洁工件表面,以提高渗碳零件表面的活性,加快钢表面吸附碳原子的速度,从而保证渗层的均匀性。
某公司采用UBE-600型滴注式可控气氛密封箱式多用炉,该设备采用了电子调控器、PID连续调节的辐射管加热,炉膛带搅拌风扇,0.75级的K型热电偶,用氧探头测碳势。设备技术要求渗层在1mm以下,渗层偏差在±0.075mm。由此看来,对于硬化层在0.20mm之内的要求,采用这种设备还有一定的难度。工件的渗层与硬化层是有区别的,硬化层还与淬火效果、淬火油的选用、工件的装夹方式等都有关。现采用的是德润宝729等温分级淬火油。
根据以上分析,工件的装夹方式见图2.47。某公司设计了两套工艺,工艺1见图2.48,工艺2见图2.49。工件在进炉前进行了(475±25)℃×1h的预处理。按9点测温的方法取件检验硬化层,见图2.50。工艺1、工艺2的检验结果见表2.78。工艺1验证了渗碳温度高时渗速快、渗碳时间难以控制的判断,渗层容易超差,硬化层均匀性差达到0.39mm。

图2.47 曲柄件的装夹方式示意图
(5)硬化层缺陷分析 采用工艺2,硬化层超差的现象稍有改善,但仍存在超差现象;硬化层均匀性也有所改善,达0.28mm。硬化层深的工件主要集中在加热室后半部分,硬化层浅的工件主要集中在加热室前半部分。出现此结果的原因如下:
①通过观察,在升温排气期不断滴入甲醇,不进行任何碳势控制,滴入甲醇仅起到气氛保护作用和气氛置换作用,升温过程中碳势最高可达1.30%Cp。对于深层渗碳,渗层的均匀性可能没有太大影响,但对于浅层渗碳,渗层均匀性影响就很大。一般冷工件进入多用炉吸热,炉内温度会骤然降至580℃,开始升温(升温速率4~6℃/min),经过约70~90min,达到930℃。在升温过程中,由于中门没有加热器,升温速度相对较慢,后室工件相对较快,因此后室的工件到温快,在同样的条件下,硬化层更深。
②工艺有降温要求,前室工件降温快,后室工件降温慢,因此在降温过程中后室工件的扩散层要比前室深一些。
③工件在淬火出炉过程中,前室工件首先接触空气,温度降得较多,淬火时温度相对低,硬化层也就较浅。
经过分析后对工艺进行修正,在升温的过程中控制碳势;渗碳温度恒定,不降温;在淬火时增加一个辅助工装,装在最上层靠近中门的工装上(见图2.47,箭头所指处),9点测温法取样示意图见2.50,辅助工装见图2.51。修改后的工艺见图2.52。

图2.48 工艺1的渗碳工艺曲线

图2.49 工艺2的渗碳工艺曲线

图2.50 9点测温法取样示意图

图2.51 辅助工装示意图
表2.78 工艺1、工艺2的硬化层检验结果 单位:mm


图2.52 修改后的渗碳工艺曲线
经修改后的工艺处理后,工件的检测结果见表2.79。硬度梯度见表2.80。工件磨后的表面硬度>56HRC。
表2.79 曲柄件的检测结果 单位:mm

表2.80 曲柄件的硬度梯度

(6)小结 通过对曲柄件浅层渗碳的分析和设备的研究,经过工艺的调整,最终生产出合格产品,为企业创造了效益。
2.2.10.4 [实例2.2]MIX主减速从动齿轮的低压真空渗碳热处理工艺实例
MIX主减速从动齿轮的低压真空渗碳热处理工艺见表2.81。
表2.81 MIX主减速从动齿轮的低压真空渗碳热处理工艺



图2.53 MIX主减速从动齿轮外形与热处理工装示意图
表2.82 材料化学成分(质量分数) 单位:/%

表2.83 材料的淬透性

表2.84 MIX主减速从动齿轮高压氮气淬火参数


图2.54 齿轮表面、心部硬度及有效硬化层深

图2.55 齿轮心部金相组织

图2.56 MIX主减速齿轮各部位的金相组织
表2.85 金相组织评判结果

2.2.10.5 [实例2.3]18Cr2Ni4W钢大型重载齿轮轴的深层渗碳工艺研究实例
18Cr2Ni4W钢大型重载齿轮轴的深层渗碳工艺研究见表2.86。
表2.86 18Cr2Ni4W钢大型重载齿轮轴的深层渗碳工艺研究



图2.57 大型重载齿轮轴外形及易发生畸变位置示意图

图2.58 大型重载齿轮轴深层渗碳工艺曲线图
渗剂每100滴为2mL,渗剂在渗碳各阶段的滴量如图所示

图2.59 大型重载齿轮轴球化退火工艺曲线图

图2.60 大型重载齿轮轴深层渗碳后淬火+低温回火工艺曲线图