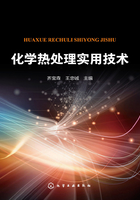
1.3 化学热处理技术的新发展
先进化学热处理技术的主要控制目标应是少或无污染、少或无氧化和节能的绿色化学热处理技术。化学热处理技术的发展,应从以下几个方面入手。
1.3.1 采用新工艺,不断优化化学热处理技术
通过采用新工艺,不断优化化学热处理技术,如表1.7所示。
表1.7 采用新工艺及其说明

1.3.2 稀土元素在化学热处理中的作用
稀土元素电子结构特殊、原子半径大、电负性低、化学活性极强,因此稀土元素在化学热处理中的加入能显著提高元素渗入速度,改善渗层组织,提高渗层性能,充分显示了稀土元素在化学热处理领域应用的良好前景。例如对稀土渗碳及碳氮共渗、稀土渗氮及氮碳共渗、稀土多元共渗、稀土渗硼及硼铝共渗、稀土渗金属等,均可净化金属表面,起到催渗作用。
鉴于我国稀土资源丰富,应充分利用这一优势,研究和开发出更多、更优异的稀土化学热处理工艺,并全面拓展其应用领域,使稀土化学热处理应用的巨大潜力发挥出来。
1.3.3 化学催渗在化学热处理中的作用
化学催渗是在渗剂中加入催渗剂,促使渗剂分解,活化工件表面,提高渗入元素的渗入能力。化学催渗在化学热处理中的作用:
①通过化学反应来洁净和清除钝化膜,改善零件表面的状态。
②通过化学催化剂作用或降低有害气体的分压来改变反应过程,以提高渗剂的活性。
1.3.4 物理催渗在化学热处理中的作用
物理催渗在化学热处理中的作用,见表1.8,其典型示例如等离子体化学热处理,脉冲离子渗氮与活性屏离子渗氮技术,双层辉光离子渗金属技术,流态床化学热处理,真空化学热处理,真空渗碳与真空渗碳高压气淬,真空脉冲渗氮与真空离子渗碳,机械能助渗化学热处理,可控气氛化学热处理分别见表1.9~表1.19。
表1.8 物理催渗及其在化学热处理中的作用

表1.9 等离子体化学热处理的分类、特点和基本原理

表1.10 脉冲离子渗氮和活性屏离子渗氮技术


图1.1 克罗克诺尔公司离子渗氮模型

图1.2 活性屏离子渗氮装置示意图
表1.11 双层辉光离子渗金属技术及其基本原理、技术特点、性能与应用

表1.12 流态床化学热处理及其工艺特点、发展趋势

表1.13 真空化学热处理及其物理和化学过程、优缺点和应用

表1.14 真空渗碳及其工艺特点、工艺方式、应用与真空渗碳高压气淬


图1.3 一段式(a)、脉冲式(b)、摆动式(c)真空渗碳工艺流程示意图
表1.15 真空脉冲渗氮与真空离子渗碳的工艺特点

表1.16 机械能助渗化学热处理技术的原理、机理、工艺优点及应用

表1.17 可控气氛化学热处理及其工艺特点

表1.18 可控气氛化学热处理常用的几种可控气氛的名称、特点及应用


表1.19 常用的可控气氛化学热处理工艺类型的名称、特点

1.3.5 表面工程与化学热处理复合处理技术的应用和发展
将表面工程技术与化学热处理工艺合理组合,以便更有效地改善工件使用性能的复合处理工艺,称为表面工程与化学热处理复合处理技术。
复合处理技术是通过最佳协同效应使工件表面体系在技术指标、可靠性、寿命、质量和经济性等方面获得最佳效果,克服了单一表面工程技术存在的局限性,解决了一系列工业关键技术和高新技术发展中特殊技术问题。如电镀与化学热处理的复合、化学热处理与喷丸强化的复合等。伴随复合处理技术的发展,梯度涂层技术也获得了较大发展,以适应不同涂覆层之间的性能过渡,从而达到最佳的优化效果。
1.3.6 金属表面自纳米化对化学热处理过程的影响
金属表面自纳米化对化学热处理过程的影响,见表1.20~表1.22。
表1.20 金属表面自纳米化及其实现方法与原理


表1.21 金属表面自纳米化的结构特征及其对性能的影响


图1.4 表面自纳米化层的组织特征和应变及应变率分布示意图
表1.22 金属表面自纳米化对化学热处理过程的影响

1.3.7 化学热处理过程的计算机模拟与智能化
1.3.7.1 化学热处理过程的计算机模拟
CAD(计算机辅助设计)作为计算机集成化学热处理系统的单元技术,近年来异军突起。热处理专家系统可以使化学热处理工艺参数的制定真正由“经验”定量转变为“科学”定量,实现最优化,并能够准确预测化学热处理后的组织与性能。应用化学热处理辅助技术,进行计算机模拟仿真和虚拟生产,以实现化学热处理计算机智能化控制。
微型计算机动态可控渗氮与渗碳技术已列入国家级科技成果重点推广计划。利用计算机控制渗碳、渗氮以及工艺气氛、参数、程序等应用近五年将达到或超过30%。在我国,氧探头的出现和计算机在可控气氛热处理中的应用是汽车工业热处理技术发展的里程碑,这项新技术的应用已逐步由自动化向智能化转变,由单一参数控制向多元素最优化系统控制转变。渗碳工艺过程模拟控制系统的成功应用就是典型代表,此系统不仅可快速模拟生产过程、优化工艺设计、准确预测结果,还可精确控制生产过程。随着可控气氛设备自动化程度的逐渐提高和渗碳过程模拟控制系统的成功应用,国产热处理可控气氛设备已成为汽车工业热处理主要生产设备,如连续式气体渗碳自动生产线、密封箱式渗碳炉生产线、转底炉和网带炉等,其功能和控制精度已接近或达到国际先进水平。
1.3.7.2 化学热处理过程的智能化
智能化学热处理是采用数学建模(数值模拟)、物理模拟、实验测试相结合的方法,在准确预测材料组织性能变化规律的基础上,优化化学热处理工艺的多学科交叉集成技术。其基本要素包括化学热处理工艺的设计与优化,化学热处理装备的设计与优化,化学热处理工艺过程的智能控制,这三者之间是相互联系又密不可分的。化学热处理计算机模拟是智能化学热处理的核心技术,它是使化学热处理从传统经验技艺跨越为科学计算机技术的重要手段;而智能化学热处理装备是实现智能化学热处理的物质基础。因此,智能化技术是我国发展清洁、节能、精密、高效的化学热处理不可或缺的技术。
总之,现代科学技术的飞速发展为实现“绿色环保,节约能源”创造了条件。从发展前景来看,必须强调的是,一定要运用高科技、采用高新技术来武装化学热处理技术,还要加快研究开发和推广应用诸如高能束化学热处理,真空、离子化学热处理,流态床化学热处理等新工艺、新技术、新装备,逐步淘汰能耗大、有污染的传统化学热处理工艺技术。
1.3.8 化学热处理发展的总目标与发展趋势
化学热处理的总目标可概括为8个字:“优质、高效、低耗、洁净”。其发展趋势包括以下几个方面。
①稳定与提高传统化学热处理工艺的质量、强化工艺过程、缩短处理周期、节约能源与降低成本。
②传统工艺中引入新技术,探索新工艺,以满足制造工业对零件越来越高的质量、外观和经济效益的要求,如激光、离子与电子束等新技术的引入,多种元素复合渗、多层薄膜复合、多种工艺复合等。
③智能技术与计算机的应用和发展,如各种化学热处理过程数学模型的研究与控制,计算机应用于能源、自动控制过程参数、产品质量与车间管理,从而全面改变化学热处理生产面貌。
④加强工艺基础理论的研究,如在化学热处理过程中,固相、液相、气相间的化学反应,吸附与扩散的热力学与动力学,材料与工艺因素对化学热处理过程、渗层组织、应力状态与性能的影响等。